Guidelines and Design Considerations for Flex PCB Electronic Manufacturing
Flexible printed circuit boards (PCBs) provide several advantages for the designer and the electronic manufacturer. Flexible PCBs provide the unique benefit of bendability for challenging application areas requiring constant flexibility. To allow the flex PCB to mold and bend without breakage results in smaller designs that are more lightweight and consume less space.
Benefits of a Flexible PCB
Flex PCBs offer a multitude of advantages for both designers and manufacturers. Here are a few benefits of flex PCBs:
- The ability to bend – the primary benefit is obvious, but also the most important.
- Improved reliability – the low number (or elimination) of connectors, solder joints, and other interface connections are the reasons why these boards are more reliable.
- Thin and light – while ensuring flexibility, the manufacturers also found a way to reduce the size and weight of flexible PCBs, making it easier to fit in constrained spaces.
- Suitable for high temperatures – flexible materials are better at dissipating heat than the materials used for rigid boards. Improved thermal management also occurs because of resistance to acids, oils, and UV exposure.
- Affordable cost – the math is simple. A smaller board will usually cost less.
Even though many flex boards have a higher density, the overall cost is usually more affordable.
- Durability – it always depends on your chosen materials, but flexible PCBs can be extremely durable. That is why they are often used in medical and military applications.
- Bendability-several applications demand high flexibility from PCBs, so bendability becomes a crucial factor in some instances.
Guidelines and Considerations
Flex PCB design requires a slightly different process than rigid PCBs. Here are a few guidelines and considerations to be aware of when designing a flex PCB.
Features of Bend Radius
The bend radius implies the minimum bend amount of the flex area, so it’s important to identify the bend radius early in the design phase to allow the design to accommodate any bends without subjecting the copper to damage. The features of the bend radius like slots, cutouts, and mounted components should not be located on the bend radius.
Material
The appropriate material must be selected to achieve a specific desired amount of flexibility. Often the materials used for flexible PCBs have low to moderate dimensional stability. The material must sustain the size and shape of PCBs without reducing flexibility. Depending on the material, some small modifications to the design may be required including inserting spurs and anchors to stabilize the material layers.
Trace Routing
The circuitry on a flex PCB is a challenging task. The higher the bend radius, the lesser the stresses introduced on the board. The traces of mounted components must run through the low-stress regions to achieve safety in the PCB design. Trace routing assists in preventing electrostatic discharge in the PCB and can also help in preventing short circuits.
Flex PCB Layer Stacking
Since multiple layers are stacked on one another in flex PCB, strategic layer stacking is crucial. To avoid slippage, the most flexible layers must be stacked at the center.
Risk of Delamination
Delamination, also known as detachment of layers, is a frequent problem in PCB fabrication and applications. The layers frequently delaminate, causing abrupt damage to the circuitry and even occasional PCB failure. To prevent delamination, an application of solder paste is required. The solder paste material must be selected according to the requirements for flexibility. Features must be introduced to the design to prevent delamination.
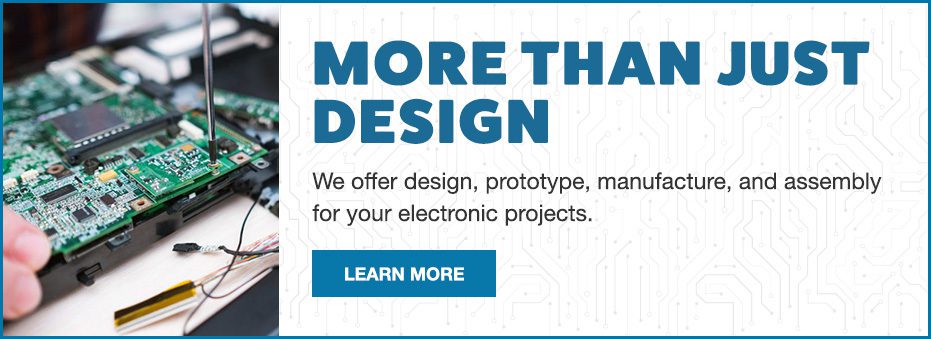
Hire a Reliable Flexible PCB Manufacturer
To ensure a smooth assembly process, consider a PCB manufacturing partner who can meet your flexible PCB requirements. An ECM with years of experience in designing simple and complex printed circuit boards is a good start. From PCB design to prototype and assembly, Levison Enterprises has the experience necessary for all of your PCB needs, so contact us today for a quote on your next flex PCB assembly project.
Start Your Quote Now!