5 Tips To Save You Time and Money On Your Next Electronic Assembly
Producing a printed circuit board is no easy feat and it’s also not an inexpensive one. When it comes to your electronic assembly you want to get the most bang for your buck without compromising your product.Luckily, there are many factors that go into PCB assembly that can be considered for cost savings without cutting quality corners. Here are five tips that can help you reduce your PBC assembly costs:
1. Use Quality Materials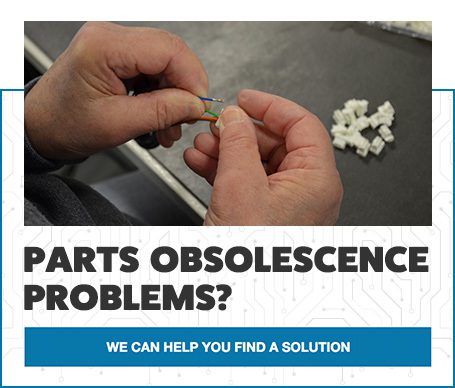
You may pay more up front for higher quality materials, however, they will absolutely be worth the money. Inexpensive parts are inexpensive for a reason. Cheaper materials will not stand up over time and you may end up with a product that will only last a few months, weeks, or even days. If you use sub-par materials now, it could cost you in the long run when you realize you need to send your PCB back to the drawing board.
2. Stick to Industry Standard Sizes for Boards & Parts
It might be tempting to go with a fancy, unconventional board shape, but doing so could easily send the cost of your PCB through the roof. This is especially true if you have a limited or oddly shaped space for the PCB in your final product. It’s best to stick with a standard square or rectangular shape. The size of your PCB is something to consider as well. If all things are equal in terms of number of parts and layer count, generally, the bigger the board – the higher the cost. Keeping your design simple and as small as possible will cut down on your expense.
The same consideration should be made for your components. Stick with standard sizes. Anything outside the norm can drive up the cost of assembly. Industry standard parts are easily assembled with automated equipment. Other parts must be assembled by hand, which can be more expensive. Unusual shapes and sizes will skyrocket your production costs.
3. Stay Within Space Requirements
Check with your PCB assembly manufacturer for information regarding their specific spacing requirements. Typically, the cost will increase as the space between your pads and tracks decreases. The more space you have between your copper objects, the easier the fabrication process will be. More precise assembly methods are required for smaller spacing, and that is more expensive. Most assemblers have spacing requirements of around 8-10 mils minimum spacing between pads, tracks, and track widths.
4. Limit Layers
You will want to maximize the power and performance of your PCB, but you might want to think twice if that means adding additional layers. Depending on materials and layer thicknesses, you could add significant cost with each layer you add to your PCB. Only use the layers you need to get the job done.
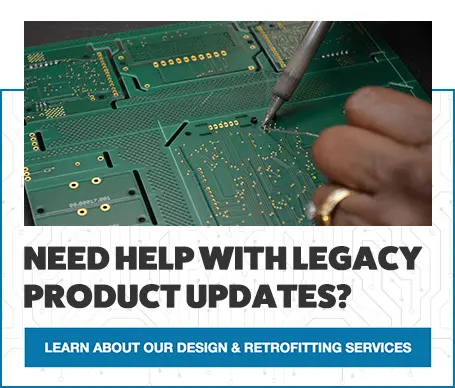
5. Get A DFM Now
You want to make sure you get a design for manufacturability (DFM) before production starts. DFM is a proven process to save time and cost by making sure your design meets the requirements of manufacturing processes to actually produce the PCB. You will want to re-work or engineer your PCB early in the process for maximum savings. It becomes much more expensive to re-design your PCB to fix issues that are discovered in later stages of the development cycle. A DFM can also lead to fewer revisions and can speed up the time to production. This means your end product can go to market sooner, and we all know that time is money.
Levison Enterprises works closely with every customer that entrusts us with their PCB project. We will work to help you reduce costs without skimping on quality to bring you a high quality PCB assembly for your project. We take customer satisfaction very seriously. To find out how we can help you save money on your PCB assembly, contact us today.