An Electronic Manufacturers Guide to Electronic Enclosure Design
Once you have given your design to an electronic manufacturer, you need to make sure that your build is protected. A custom electronic enclosure is vital to ensuring your device will have the functionality and longevity your users expect. When designing a custom enclosure, there are many considerations.
Considerations for Enclosure Design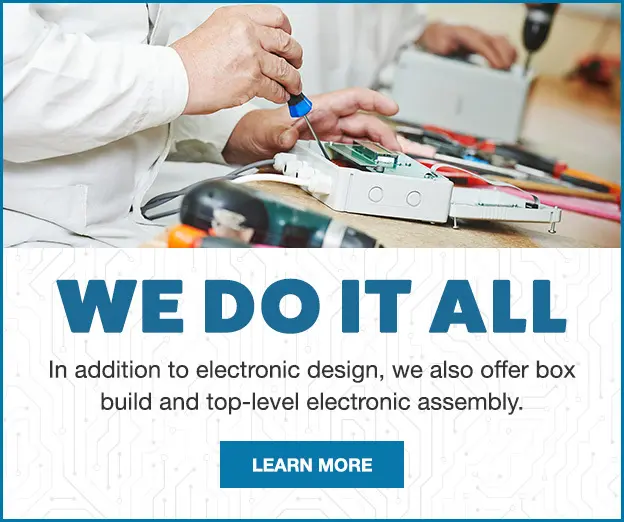
-
Metal Thickness
Experience is often necessary for choosing metal thickness, as they can all look very similar to the unfamiliar eye. The in-house engineer at your ECM partner shop can assist you in finding the right metal thickness for your custom electronic enclosure.
-
Custom Cutouts
With a custom enclosure design, you can choose any cutout you wish. There are functional cutouts for connectors, displays, and switches, but there are also creative cutout designs. These will allow you to include your company logo, brand, or product name.
-
Bending Radius
There are functional considerations regarding bending radius. Metal typically can not be formed into a true 90-degree corner. When you design your enclosure, you will specify a bend radius. There are two key factors when making this specification. Functional considerations are that no flat service for fasteners, components, or cutouts are applicable until you are clear of the bend radius. Aesthetics must also be considered. “Retro” styles often have large radii for a curvier feel.
Material Selection
Choosing the right metal and thickness is one of the first decisions you will make when designing your custom electronic enclosure.
-
Aluminum
Aluminum is a lightweight corrosion-resistant metal. It can be powder coated or left unfinished. Aluminum can be chem-filmed when electrical contact is required and can also be anodized to put on a hard, durable protective oxide coating. Aluminum has lower thickness than steel. 5052 Aluminum is ideal for sheet metal enclosures and parts, and 6061 aluminum is easy to machine but more susceptible to cracking.
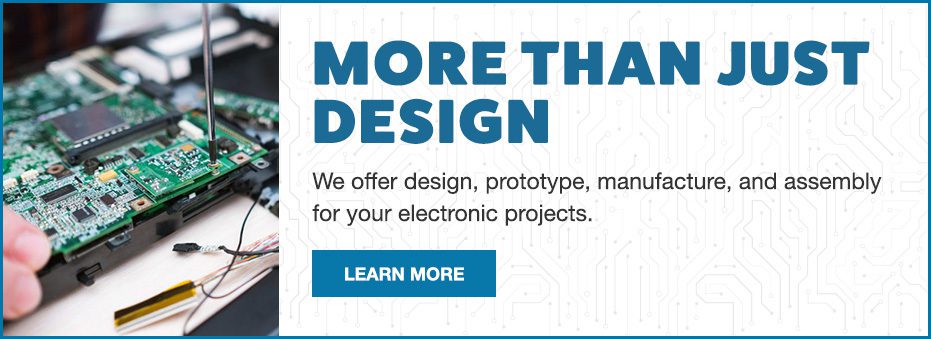
-
Cold Rolled Steel
Cold rolled steel is used about as often as aluminum for general purpose enclosures. It has long-term durability when finished with a powder coat. The drawback to cold rolled steel is that it is not corrosion resistant.
-
Stainless Steel
Stainless steel has high strength and stiffness and is highly corrosive resistant because of the chromium and nickel content. Stainless steel can be powder coated or left unpainted as bare metal.
-
Galvanneal
Galvanneal is a low-carbon steel coated with zinc and then annealed so the zinc bonds via diffusion. Galvanneal is not as durable as stainless steel or aluminum.
-
Copper
Copper is soft, flexible, and ductile. It has high thermal and electrical conductivity. Although fastening must be done with care due to the softness of the metal, the high conductivity makes it ideal for electronic applications.
Fasteners and Welding
Fastening points and welding are a crucial part of the enclosure design. Welding can be used to solve problems such as creating complex parts, creating watertight joints, or adding strength.
-
Self-Clinching Fasteners
Self-Clinching fasteners are threaded nuts, studs, and other styles that are pressed into sheet metal.
-
Spot Welding
Spot welding is fast, efficient, and inexpensive. It will permanently join two pieces of metal in one or more spots and will leave little trace of the joint.
-
Seam welding
Seam welding will join two or more pieces of sheet metal, so they appear seamless. This style of welding is useful for weatherproofing.
-
Tack welding
Tack welding is performed in exactly the same way as seam welding, but in discrete segments.
Finishing
-
Powder Coating
A dry thermoplastic powder will be applied electrostatically and fused to the metal in an oven. It is available in a variety of colors, glosses, and textures and is the industry standard for painting metal.
-
Digital Printing and Silkscreening
These are finishing techniques that will give your enclosure a professional look and feel. These techniques will allow you to clearly label your enclosure, but also excellent for company logos and artwork.
-
Chemical Conversion Coating
Chemical conversion coating creates a corrosion-resistant and durable surface that exhibits stable electrical conductivity.
-
Anodizing
Anodizing is an electro-chemical process to prepare the surface of non-ferrous metals, such as aluminum, which will make them harder and more resistant to corrosion. The anodized surface will become part of the aluminum, meaning it will never peel, chip, or flake off.
-
Tin Plating
Tin plating is an immersion technique that deposits pure tin onto copper, which will improve corrosion resistance, conductivity, and solderability.
-
Bare Metal Finishing
Bare metal finishing is offered in three basic types. In a no finish, the part is de-burred with no additional finishing and may exhibit small scratches or swirl marks. This is cost effective but only useful for functional parts that will not be on display. A grained finish means that the part is deburred and then given a specific linear grain direction via brushing. Finally, a tumbled finish smoothens and imparts non-directional finish via tumbling in an abrasive medium, providing a similar aesthetic to frosted glass.
Start Your Quote Now!Designing a custom electronic enclosure requires many choices and specifications. Fortunately, when partnering with a turnkey electronic manufacturer, the in-house design engineers are there to help you through the process and find the right enclosure to protect your build. Levison Enterprises is your one stop turnkey partner. We have a wide array of industry experience and with in-house engineering, assembly, and shipping all under one roof we are the clear choice for your next build. Contact us today for a free quote.