Sustainability in Medical Device Manufacturing: Eco-Friendly Practices
When it comes to concerns about medical device manufacturing, environmental concerns may not be the first thing that comes to mind. Patient safety and device effectiveness are usually at the top of the list. However, the truth is that medical device manufacturing and its effect on the environment is becoming an increasingly bigger problem.
Patient care should always come first, but for many manufacturers of medical devices, including Levison Enterprises, sustainability and the environment are becoming increasingly bigger concerns.
Sustainability in Medical Device Manufacturing
Sustainability has become a major concern in medical device manufacturing for a number of reasons. Currently, their production accounts for 4.4 percent of net emissions globally, and that number will only continue to grow. An increasingly older population, coupled with greater access to healthcare and device innovation will continue to drive demand for the foreseeable future. Medical devices are resource-intensive, both in composition and manufacturing.
Because of this, sustainability in medical device manufacturing is a growing priority as the world confronts the challenges of climate change and resource depletion. At the same time, medical devices can be difficult to recycle and also consume vast amounts of energy to manufacture.
This has made innovation in sustainability a priority for those who manufacture medical devices. Manufacturing being more efficient and economical will not only have positive effects on the environment but on your bottom line as well.
Challenges and Opportunities
The materials utilized in medical device manufacturing are mainly plastics, ceramics and metals, many of which are derived from non-renewable resources. Additionally, devices can contain hazardous materials, such as lead or mercury.
On top of that, the regulatory landscape for medical device manufacturing can also become an obstacle. Such devices must meet rigorous standards for safety and effectiveness, making switching to more sustainable materials a challenge, especially if those materials may introduce new, unknown risks.
With the push within the medical community to reduce hospital-acquired infections (HAIs), the rise of single-use devices (SUIs) contribute greatly to the amount of medical device waste created everyday. However, studies show that devices designed for multiple uses may have a higher carbon footprint due to the sterilization process.
Other industries may have the option to turn to bio-degradable plastics or alternative materials. With medical devices, such an option could introduce concerns over durability, sterility, or overall effectiveness.
To be clear, there are no easy answers for medical device manufacturers pursuing greater sustainability.
There has been a slow and steady shift towards integrating sustainability practices in manufacturing, and the regulatory framework has recognized that and started changing with it.
The FDA has acknowledged the environmental impact of worldwide medical device manufacturing and has started encouraging environmental consciousness where it can. Packaging waste reduction, material recycling, and overall energy efficiency have found a place at the table. This shift has offered the opportunity for manufacturers to align sustainability goals with compliance requirements, bringing improvements to the design and production process.
Innovation in Design and Materials
The shift to more sustainable practices has led to a number of improvements in materials used in medical devices. Polylactic acid (PLA), for instance, is a plant-based plastic that can be used in certain medical applications and is compostable under certain conditions. There have also been efforts to increase the use of recycled plastics and metals in devices in an attempt to lower the carbon footprint of manufacturing.
In addition to material innovation, designing for longevity and recyclability has become a crucial strategy. Devices can be designed with modular components that are easy to replace or upgrade as needed, rather than disposing of the entire unit. Some implantable medical devices are now designed to have replaceable parts, reducing the waste created over the life of the device. Another example is the use of smart medical devices that can be recharged or repurposed, extending their life cycle and reducing the need for replacement.
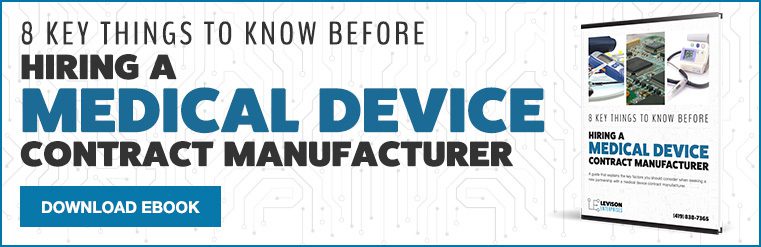
Efficiency in Manufacturing
A large part of the negative environmental impact of medical device manufacturing is hardcoded into the transport and actual manufacturing process. In pursuit of greater efficiency across the board, attention is being paid to optimizing factory operations, transitioning to renewable energy sources, and incorporating energy-efficient technologies into manufacturing devices.
3D printing has gained popularity in the medical device manufacturing field as a method for producing custom devices or components with less waste. Traditional methods such as injection molding or machining often resulted in material waste and high energy consumption.
These strategies can help lower the overall environmental impact of the production process, leading to significant reductions in carbon emissions and resource consumption.
Impacts on the Economy and End-of-Life Management
The idea of a “circular economy” is growing in popularity as a more sustainable alternative to the conventional linear model, which follows a make-use-dispose pattern. This innovative approach focuses on reducing waste by rethinking how materials are used, encouraging reuse, and promoting recycling to extend product life cycles and lessen the environmental impact.
For medical device manufacturers, this approach could involve designing devices for disassembly so that materials can be more easily separated and recycled at the end of their life cycle. Companies could also explore options for device refurbishment, where used devices are collected, cleaned, and reconditioned for use.
Establishing take-back programs where used devices are returned to the manufacturer for recycling or proper disposal can contribute to a more sustainable end-of-life strategy. This can be particularly important for devices that contain hazardous materials or those that are difficult to recycle.
At Levison Enterprises, we combine innovative solutions with a commitment to sustainability, setting a new standard in medical device manufacturing. Our dedication to quality and environmental responsibility ensures your products are made to exceed expectations while making a positive impact. Contact us today to discover how our experience can bring your vision to life with precision, reliability, and purpose.
Start Your Quote Now!