Successful ECMs Streamline with a Continuous Improvement Process
Remember the proverb “waste not, want not?” It means if you use a resource carefully and without extravagance, you will never be in need. Now, look at that philosophy from an electronic contract manufacturing standpoint. Could you trim some fat from your bottom line?
There is nothing quite as frustrating as wasting time, money, and resources. This is especially true in electronic contract manufacturing. This is why top ECMs use a continuous improvement process. This approach to manufacturing identifies inefficient processes that lead to waste. Every member of the team works toward the common goal of reducing waste by identifying and correcting ineffective processes. Eventually, the savings will trickle down to you.
Benefits of a Continuous Improvement Process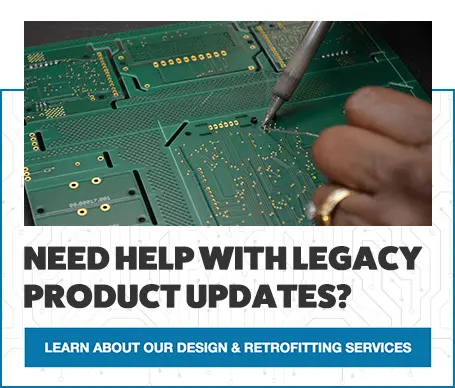
A continuous improvement approach can assist manufacturers to operate on a higher level while constantly seeking out new opportunities to add value to their products, services, and processes.
Manufacturers that employ a continuous improvement process will not only see a positive impact on their business, but will pass the benefits along to their clients. Some of these benefits include:
- Increased productivity
- Improved quality
- Lowered costs
- Decreased delivery times
- Improved employee satisfaction/morale
- Reduced employee turnover rate
Overall, companies that use a continuous improvement process tend to work very efficiently. They recognize and seize opportunities that benefit their business effortlessly without interrupting daily tasks. It also results in the elimination of waste in systems and processes while resulting in total quality management.
Plan-Do-Check-Act
The Plan-Do-Check-Act (PDCA,) or Deming Cycle, is one of the most widely used tools companies adopt to implement a continuous improvement process. Plan-Do-Check-Act is a four–step model for carrying out change. It is basically a continuous loop of planning, doing, checking or studying, and acting. It works as follows:
- Plan – Identify and understand your problem, and account for any potential risks.
- Do – Test a solution on a small scale to try it out.
- Check – Check your work for quality and see that improvement has occurred.
- Act – Fully implement the solution and make adjustments as necessary.
The PDCA cycle is continuously repeated for ongoing improvement. It is done over and over as modifications and changes are made for the betterment of the end result. PDCA is a proven methodology and is also included as part of the AS9100 Quality assessment.
Clients depend on their electronic contract manufacturing company to do what they say they are doing, identify gaps in procedures, and provide efficient services to produce their products. That’s why Levison Enterprises believes in a continuous improvement process. We regularly utilize the Plan-Do-Act-Check Cycle and our clients enjoy the benefits. Contact us today and find out more about our partner benefits, and how we can work with you to create your next project.
Start Your Quote Now!