Streamlining Aerospace Manufacturing for Optimal Performance
Aerospace manufacturing leads the way in innovation, where precision, efficiency, and reliability are not optional but essential for success. The stakes are high when designing and producing components that will traverse the skies and beyond. The industry is embracing groundbreaking technologies to meet these demands, with digital twin technology emerging as a game-changer. This cutting-edge approach bridges the gap between physical production and digital precision, unlocking new ways to streamline processes, reduce waste, and optimize performance.
What is Digital Twin Technology?
Digital twin technology generates a virtual model that mirrors a physical product, system, or process, allowing real-time monitoring and simulation.
This isn’t just a static model; it’s a dynamic, real-time simulation that evolves as the physical counterpart does. Imagine a jet engine being designed and produced. A digital twin of that engine can simulate its performance under various conditions, monitor its production in real-time, and predict how it will behave over its lifecycle.
In aerospace, where the slightest inefficiency can have massive implications, the ability to digitally mirror and monitor every aspect of manufacturing is revolutionary. By leveraging these virtual replicas, manufacturers can anticipate challenges, refine designs, and make sure each component meets exacting standards before it’s ever built.
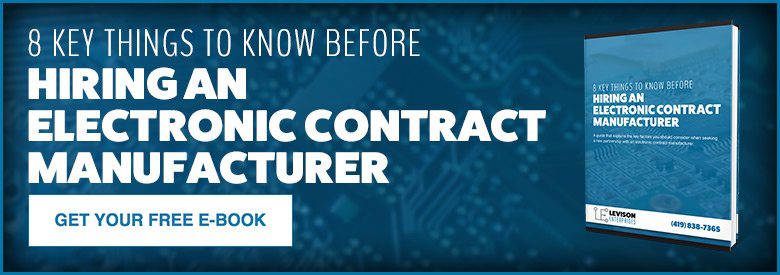
The Role of Digital Twins in Production
The complexity of aerospace systems demands precision manufacturing and assembly. From intricate materials to sophisticated geometries, the production line is a high-stakes environment where errors can be costly. This is where digital twins shine.
Digital twins allow manufacturers to monitor each step in real-time during production. For example, if a variation occurs during the machining of a turbine blade, the digital twin can immediately detect and flag the discrepancy. This proactive insight prevents minor errors from cascading into more significant problems, ensuring consistency and quality.
Digital twins enable process optimization. Manufacturers can simulate production scenarios to determine the most efficient workflows, minimizing downtime and maximizing throughput. Whether scheduling maintenance or reallocating resources, these simulations ensure production lines operate at peak efficiency.
Improving Component Performance
Aerospace components must perform flawlessly in extreme conditions. Whether enduring the high temperatures of engine combustion or the icy void of space, their reliability is paramount. Digital twins are proving indispensable in predicting and enhancing component performance.
Take the example of an aircraft wing. Engineers can use its digital twin to simulate how the wing will behave under various aerodynamic forces. By analyzing this data, they can refine the design to reduce drag, improve fuel efficiency, or enhance structural integrity. These continuous enhancements take place in the digital space, conserving time and resources compared to traditional physical testing methods.
Digital twins are essential for predictive maintenance, enabling proactive monitoring and early identification of potential issues. Instead of relying on fixed maintenance schedules, sensors embedded in components feed real-time data to their digital counterparts. This allows manufacturers and operators to predict when a part will likely fail and address the issue before it becomes vital. The result? Reduced downtime, lower costs, and safer operations.
Sustainability Through Digital Innovation
In addition to boosting performance, digital twin technology is helping aerospace manufacturers address growing sustainability concerns. Traditional manufacturing processes often generate significant material waste and consume substantial energy. Digital twins provide a more innovative way to approach production, cutting waste at its source.
Manufacturers can optimize designs by simulating processes and materials digitally to use fewer resources. For instance, they can identify areas where lighter, more substantial materials might replace heavier ones, reducing the environmental impact of the final product. These insights contribute to the broader goal of creating greener, more fuel-efficient aircraft.
Digital twins facilitate circular manufacturing by tracking component lifecycles, ensuring they are reused without compromising quality or safety. This aligns with the industry’s commitment to reducing carbon footprint and fostering sustainable innovation.
Overcoming Implementation Challenges
Although digital twin technology offers clear advantages, its implementation in aerospace manufacturing presents several challenges. Creating a digital twin requires enormous data from sensors, simulations, and real-world operations. Ensuring the accuracy and reliability of this data is essential, as even minor discrepancies can lead to flawed predictions.
There’s also the question of cost. Implementing the sensors, software, and computational infrastructure needed for digital twins can represent a significant upfront investment. However, the long-term savings and performance gains often outweigh these costs. By reducing errors, improving efficiency, and extending the life of components, digital twins often pay for themselves over time.
Another hurdle is the cultural shift required within organizations. Adopting digital twin technology means rethinking traditional workflows and embracing a more data-driven approach. This may require extensive training and adaptability, but the benefits far outweigh the challenges.
The Future of Aerospace Manufacturing
As digital twin technology continues to evolve, its impact on aerospace manufacturing will only grow. Integrating AI and machine learning with digital twins unlocks the potential for more sophisticated and intuitive systems. These advancements allow for better predictive capabilities, deeper insights, and enhanced automation across the production line.
In the coming years, we may see digital twins that monitor, predict, and autonomously adjust production processes in real time. This level of sophistication could redefine what’s possible in aerospace manufacturing, making the process more agile, efficient, and responsive than ever.
As more manufacturers adopt digital twins, collaborative opportunities will emerge. Entire supply chains could be integrated through shared digital twin ecosystems, creating a seamless flow of data and insights across companies. This would drive innovation and enable manufacturers to tackle industry-wide challenges together.
A Leap Forward in Aerospace
The aerospace industry has always been synonymous with pushing boundaries. From the first powered flight to exploring other planets, it thrives on innovation. Digital twin technology represents the next leap forward, offering a brighter, more efficient way to design and build the aircraft and spacecraft of tomorrow.
By bridging the gap between the physical and digital worlds, digital twins are transforming aerospace manufacturing. They empower manufacturers to optimize production, enhance component performance, and achieve sustainability goals while maintaining the precision and reliability the industry demands.
As aerospace companies continue to explore this technology’s potential, one thing is clear: the future of manufacturing is digital, with digital twins leading the way. The sky, quite literally, is no longer the limit.
The Future of Aerospace Manufacturing Starts Now
Digital twin technology is revolutionizing aerospace manufacturing, offering unparalleled precision, efficiency, and sustainability. By bridging the gap between the physical and digital worlds, manufacturers can streamline production, enhance component performance, and reduce waste—all while maintaining the reliability and safety the industry demands.
At Levison Enterprises, we are skilled in cutting-edge solutions that help aerospace manufacturers stay ahead of the curve. Whether you’re looking to future-proof your design or optimize your production workflows, our team has the expertise to bring your vision to life. Contact us today for a quote and take the first step toward a smarter, more efficient future in aerospace manufacturing.
Start Your Quote Now!