Risk Mitigation and Continuity Strategies in Aerospace Manufacturing
With supply chain shortages still a concern, proactive risk mitigation and continuity strategies are more important than ever. Even a short delay can have serious consequences, and trying to mitigate supply chain shortages on the fly can result in ineffective, expensive, and even non-compliant choices. Having supply chain risk mitigation processes in place is the best way to safeguard operations.
Is Supply Chain Still a Problem?
Components used in aerospace manufacturing depend on a complex, multilayered network of suppliers and raw materials. While supply chain issues were worse several years ago, particularly during and after the pandemic, things are still not back to pre-pandemic status. Global supply chains faced multiple disruptions at once, including a surge in demand, pandemic-related manufacturing slowdowns, raw material shortages, and industry restructuring. Supply chain issues remain a significant problem in aerospace manufacturing, with key components in short supply and ongoing disruptions affecting production timelines. Future demand, as well as shortages, have been difficult to predict. Because there is no real predicted end to supply chain challenges, aerospace manufacturers need to focus on ways to work around the problems, rather than trying to wait them out.
The Benefits of Enhancing Supply Chain Resilience
Addressing supply chain resilience strategies should not be something left to when the problem arises. Proactive supply chain strategies are the key to enhancing resilience. It is well known in aerospace manufacturing that product traceability and the use of vetted suppliers is necessary to meet the strict quality standards and regulatory requirements. Addressing supply chain issues will help mitigate risk and avoid disruption. In addition, devoting time and resources to risk mitigation and continuity strategies at the beginning of the manufacturing process will help guarantee part quality.
Inventory Management is Key
Technology now enables analytics to provide insights into inventory management and predict potential shortages allowing aerospace manufacturers to address these potential disruptions before they become problems that will delay production and impact operations. AI-driven tools can assess the current inventory against projected needs and potential for risks and suggest mitigation strategies, such as sourcing components earlier than usual, looking for alternate suppliers, or redesigning components that will work with readily available components. Inventory management can also address shortages that are likely to cause issues in the future. This allows the design and manufacturing teams to begin their work to source options that meet regulatory compliance. As analytics capabilities advance, more can be known sooner, which means that any potential issues can be addressed early in the process.
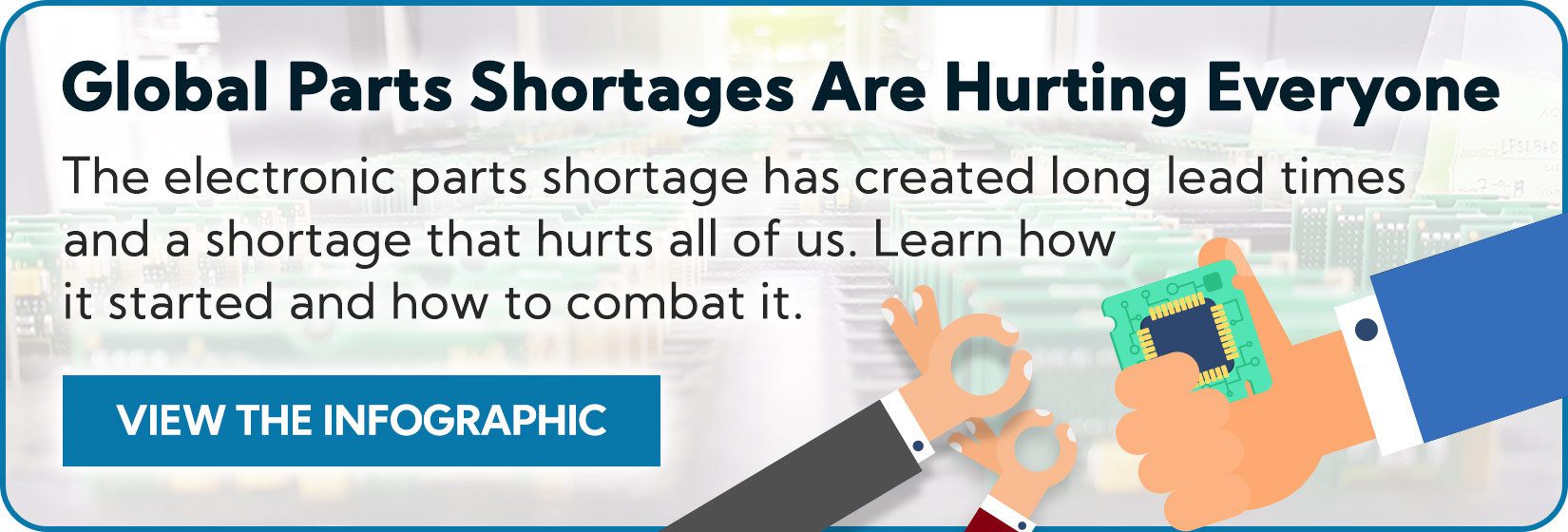
Supplier Diversification Allows for Continuity
Diversifying your list of suppliers is one of the most important things you can do. While it has been shown that supply chain issues can strike multiple suppliers at once, the reliance on an individual supplier is one of the most significant risks in the aerospace and defense supply chain. Having a broad pool of suppliers with diverse capabilities and resources reduces that risk.
All suppliers not only need to be able to provide the components, but also need to consistently meet quality and delivery standards, as well as regulatory compliance. Aerospace manufacturers know the rigorous vetting process to find suppliers and tracing processes to ensure that every component has been tracked is extensive. When supply chain issues arise, it’s not always as simple as finding a new supplier. This is why aerospace manufacturers need to make supplier diversification a priority. Relying on a single supplier leaves your operations far too vulnerable. By vetting and maintaining relationships with multiple suppliers, you will have options when faced with supply chain disruptions. Instead of scrambling to vet a new supplier—risking delays or regulatory issues—you will already have backup options in place. While there are some issues that can cause issues with multiple suppliers, often it is that one supplier is facing a localized production or geographical disruption, and having a strong network can solve the problem easily.
Have Contingency Plans in Place
If the last few years have taught manufacturers, developers, and designers anything, it is that having a robust contingency plan in place is the most critical part of supply chain management. The question is no longer ‘if’ the supply chain could be an issue during the process, but ‘when’ it will impact the timeline.ƒ Quality manufacturers in all industries, but particularly in aerospace manufacturing, need to outline contingency plans that address responses to any component shortage. These plans can be as simple as moving on to another vetted supplier, to redesigning the product to work with readily available components. Not only should contingency plans be in place, but they should be regularly updated to make sure they remain relevant and effective.
Strengthening Aerospace Manufacturing Resilience
In the highly regulated aerospace manufacturing industry, supply chain resilience isn’t just a best practice—it’s a necessity. Proactively managing inventory, diversifying suppliers, and implementing robust contingency plans are essential steps to mitigating risk and for uninterrupted production. With ongoing supply chain challenges showing no clear end, aerospace manufacturers must stay ahead by adopting strategic solutions that safeguard operations and maintain compliance.
At Levison Enterprises, we understand the complexities of aerospace manufacturing and the critical importance of reliable supply chain management. Our team is committed to delivering high-quality, traceable components while helping you navigate supply chain challenges with confidence. Contact us today for a quote and discover how we can support your manufacturing needs.
Start Your Quote Now!