Reducing Weight and Enhancing Performance with Aerospace Electronic Manufacturing
In aerospace, every ounce counts. Engineers know that shaving off even a small amount of weight from a component can make a world of difference in performance, fuel efficiency, and overall mission success. Finding ways to make components lighter while keeping them reliable and up to strict standards is no easy task. Advances in electronic manufacturing have opened new doors for weight reduction, offering materials and designs that maintain the integrity and functionality essential in aerospace applications. Yet, in a field where safety is paramount, these innovations undergo rigorous testing to ensure that any reduction in weight doesn’t come at the cost of reliability. It’s a high-stakes balancing act—one where every innovation is carefully engineered to support safe, high-performing aerospace systems.
Benefits of Lightweight Design
It is no surprise that lightweight design is essential for optimal aviation, and as environmental concerns continue to grow, reducing aviation emissions has become a priority for designers and manufacturers. The lighter the aircraft, the more efficient it can be. The most effective way to increase energy efficiency and reduce fuel consumption is to reduce the plane’s mass since simple physics tells us that lower mass requires less lift force and thrust during flight.
A 20% weight savings can result in a 10% improvement in fuel efficiency, which is a substantial savings. In addition to a lower carbon footprint, lightweight design improves flight performance, like better acceleration, safety performance, and increased structural strength. Because the benefits of lightweight design are great, designers and ECMs have been working on more ways to reduce the overall weight, including the electronic components themselves.
Challenges in Lightweight Design
There are several challenges that the aerospace industry faces when working toward a more lightweight and efficient electronic device design. The aerospace industry is highly regulated with stringent standards, and navigating these regulations can present a significant challenge to manufacturers attempting to innovate with new materials, methods, and designs. Finding the balance between new technologies and strict standards can be a challenge. Still, as the industry advances, more of these new innovations are proven safe and effective.
Another challenge has been supply chain disruptions, which can impact the availability of necessary components needed for lightweight manufacturing. The events of the past several years have highlighted the vulnerability of supply chains. Still, during that time suppliers began the necessary work to build more resilient supply chains to mitigate the disruption risk.
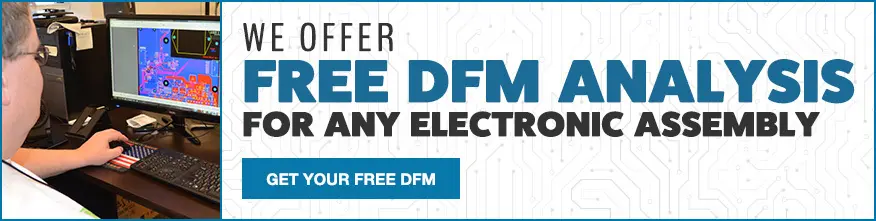
How to Achieve Lightweight Design
Since lightweight design is essential for reducing weight, finding new ways to optimize design has been the focus of many aerospace engineers. The main principle of lightweight design is to use less material with lower density. Reducing density is 3-5 times more effective than increasing stiffness or strength. Most weight reduction can be achieved with material selection. However, structural optimization is another way to reduce weight.
Structural optimization distributes materials more effectively to reduce the material necessary while enhancing structural performance with increased strength, higher stiffness, and better vibration tolerance. Most structural optimization techniques focus on size, shape, and topology. A DFM (Design for Manufacturability) analysis is essential to make sure that optimal material selection and structural decisions are considered before design completion. Using flex PCBs allows for more freedom in component placement, further aiding the advanced design methods that can help reduce overall weight.
Lightweight Materials That Hold Up
Working with lightweight materials when manufacturing electronic components while still ensuring that these components can hold up to the performance requirements is the biggest factor in reducing overall weight. Selecting aerospace materials impacts many aspects of aircraft performance, including reliability, lifecycle cost, structural efficiency, energy consumption, flight performance, and payload.
High-strength metals, especially aluminum alloy, have been the standard materials for many years and still dominate most designs. Aluminum alloys have a lighter weight than other metal options and offer many benefits and a relatively low cost.
Composite materials, however, have shown great success in recent developments. Carbon fiber has quickly become a popular choice in material selection, but fiber-reinforced polymer and fiber metal laminates have also been noted as quality options for lightweight materials. While these materials can offer a significant advantage in reducing weight, they are also more expensive options when compared to the traditional materials that have proven reliability and performance. The challenge is finding the right balance when working to reduce weight without impacting performance. As technology advances, particularly in the development of composite materials, the options for lightweight materials will continue to increase.
Advanced Manufacturing Techniques Make it Possible
When reducing weight and enhancing performance is the priority for an aerospace PCB, advanced techniques can be used along with lightweight materials. Multi-layer boards and surface mount components are used to help miniaturize PCBs. The smaller the electronic component, the more the weight can be reduced.
Additive manufacturing, foam metal, and advanced metal forming can enable the application of advanced materials while also relaxing constraints, allowing for multiscale structural optimization’s flexibility.
Designers, engineers, and electronic contract manufacturers are committed to continuous improvement in the aerospace industry. The more that weight can be reduced, the less the environmental impact and the greater the efficiency of the aircraft, which is what every manufacturer strives for.
Levison Enterprises, with AS9100 certification from NSF-ISR, is here to support your project with industry experience and innovative design assistance. Our knowledgeable team and on-site engineers are ready to help you bring a high-quality, dependable device to market. Let’s build a partnership to move your project forward with confidence. Contact us today to learn more about what we can achieve together.
Start Your Quote Now!