Precision Manufacturing Techniques for Aerospace Electronic Devices
The aerospace industry is known for innovation, engineering excellence, and high-level functionality. For electronic components, precision is not an option. Whether its circuit boards controlling flight systems or sensors monitoring critical equipment, manufacturing techniques must achieve exacting standards. Partnering with an experienced manufacturer like Levison Enterprises ensures that your intellectual property is protected and your devices meet the stringent demands of aerospace applications.
Why Precision Matters in Aerospace Manufacturing
Aerospace electronic devices operate in extreme environments where failure is not an option. Precision in manufacturing ensures devices maintain functionality under high pressure, extreme temperatures, and heavy vibrations. For printed circuit boards (PCBs) and other electronic components, tight tolerances are essential to achieving reliability and longevity. Even minor deviations can lead to catastrophic failures, making precision-driven manufacturing a cornerstone of the aerospace industry.
Modern aerospace designs often include compact and complex geometries that require highly skilled manufacturing techniques. A manufacturing partner must demonstrate mastery of these advanced processes while adhering to industry regulations, such as AS9100 certification, which ensures consistent quality in aerospace manufacturing.
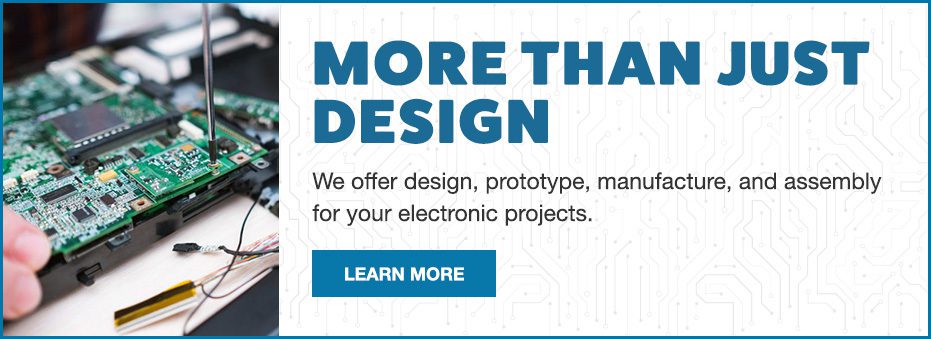
Advanced Materials in Aerospace Electronic Industry
Materials used in aerospace electronic devices offer high performance without adding unnecessary weight. This delicate balance has driven the adoption of advanced materials, including lightweight composites, high-strength alloys, and specialized polymers.
- Composites and Alloys: Aerospace-grade aluminum and titanium provide excellent strength-to-weight ratios, critical for components that need to withstand harsh conditions while minimizing mass.
- Nanomaterials: Innovations like carbon nanotubes and graphene are improving electrical conductivity and thermal management in PCBs, ensuring devices can handle increased workloads without overheating.
Precision Techniques for Tight Tolerances
To meet the rigorous demands of aerospace, precision machining is key. Techniques like CNC (Computer Numerical Control) machining, laser cutting, and advanced lithography ensure that components achieve tolerances measured in microns.
- CNC Machining: With computer-guided precision, CNC machines can create intricate geometries for enclosures, connectors, and other device components. These machines are indispensable for producing consistent results across large volumes.
- Laser Drilling and Cutting: Laser-based methods offer unmatched accuracy, ideal for creating microvias in PCBs or shaping delicate components.
- 3D Printing for Prototyping: Additive manufacturing allows engineers to rapidly prototype complex designs. By identifying and solving potential issues early, this technology reduces costly production delays.
These techniques not only enhance precision but also improve production efficiency, allowing aerospace manufacturers to meet tight deadlines without compromising quality.
Thermal Management and Electrical Reliability
One of the biggest challenges in aerospace electronic manufacturing is thermal management. Devices often have to operate in conditions where heat dissipation is critical. Precision manufacturing addresses this challenge by integrating advanced thermal management systems into the design and fabrication process.
- Heat Sinks and Thermal Via Structures: Proper placement of heat sinks and thermal vias on PCBs ensures that heat is effectively dissipated, prolonging device lifespan.
- Conductive Materials: Incorporating highly conductive materials like copper and graphene improves heat distribution and reduces the risk of thermal damage.
Electrical reliability is equally important. Components must remain stable in high-frequency environments and maintain signal integrity. Techniques like controlled impedance routing ensure circuits perform reliably even in challenging conditions.
Assembly Processes for Complex Aerospace Devices
The assembly process is where precision manufacturing truly shines. Aerospace electronic devices often require multi-layered PCBs, fine-pitch components, and high-reliability solder joints. Automated assembly techniques can reduce errors and ensure uniformity.
- Surface Mount Technology (SMT): SMT allows for the precise placement of components on PCBs, enabling compact designs without compromising functionality.
- Automated Optical Inspection (AOI): AOI systems use high-resolution cameras to verify solder connections and component placement, ensuring every device meets exact specifications.
- Conformal Coating: To protect devices from moisture, dust, and chemicals, conformal coatings are applied. These coatings are critical for aerospace applications where environmental exposure is a constant concern.
The ability to handle complex assemblies is what sets apart experienced manufacturers like Levison Enterprises. Their turnkey services—from design to final delivery—streamline the production process, saving time and reducing risks.
Quality Assurance and Regulatory Compliance
Meeting aerospace standards requires rigorous quality assurance (QA) processes. From design validation to final inspection, every step must comply with industry regulations. AS9100 certification, for example, demands traceability and stringent control over manufacturing processes.
At Levison Enterprises, QA isn’t just a step—it’s an integral part of our manufacturing philosophy. Every component undergoes exhaustive testing to ensure it performs as expected in real-world conditions.
Statistics illustrate the importance of quality in aerospace manufacturing. Research shows that the cost of a product recall in the aerospace industry can reach millions of dollars, making upfront investment in QA essential. By partnering with a manufacturer committed to quality, you can avoid costly failures and ensure long-term reliability.
The Role of Testing in Aerospace Electronic Manufacturing
Testing is a vital part of the manufacturing process for aerospace electronics. Devices must perform flawlessly in environments that simulate real-world conditions, such as extreme temperatures, vibration, and pressure changes.
- Environmental Stress Screening (ESS): ESS subjects devices to thermal cycling and vibration to identify potential weaknesses.
- Functional Testing: Every device is tested for functionality under simulated operating conditions to ensure it meets performance requirements.
- X-Ray Inspection: X-rays verify solder joints and internal connections, especially in multi-layer PCBs where visual inspection isn’t feasible.
Comprehensive testing not only confirms that devices are ready for deployment but also instills confidence in their long-term reliability.
Trust the Leaders in Precision Manufacturing
Precision manufacturing is more than just a process—it’s a promise. For aerospace electronic devices, this promise ensures that every component functions as intended, every time. As you look for a manufacturing partner, consider their ability to protect your intellectual property, deliver on tight tolerances, and provide turnkey solutions tailored to your needs.
Levison Enterprises is uniquely positioned to meet these challenges. Our experienced team, advanced technology, and commitment to quality make us an ideal partner for your aerospace electronic contract manufacturing. With Levison Enterprises, you gain not only a partner but also a trusted advisor who understands the complexities of your industry.
Let Us Help You Bring Your Designs to Life
Manufacturing aerospace electronic devices demands precision, innovation, and reliability. Choosing the right partner ensures your designs will meet the highest standards of quality. Contact us today to get a free quote and discuss how we can support your next aerospace project.
Start Your Quote Now!