PFMEA: Evaluate and Optimize Your Electronic Manufacturing Process
As an electronic manufacturer, we like to think failure isn’t an option-even though that’s easier said than done. This means manufacturers must go the extra mile to protect their products and can be accomplished by employing a process referred to as a PFMEA, or Process Failure Mode Effects Analysis.
What is PFMEA?
Process Failure Mode and Effect Analysis (PFMEA) is a proactive tool used to identify, evaluate, and prioritize potential weaknesses or failure modes in any given system. From its early stages of development with NASA, the PFMEA has evolved into an industry-accepted methodology used across a variety of fields from pharmaceutical, to military, to automotive.
Process Failure Mode Effects Analysis (PFMEA) is used by manufacturers to detect potential failures that are rooted in the physical process of producing a part. Each step of the process is carefully analyzed to identify every possible thing that could go wrong.
How Does PFMEA Benefit You?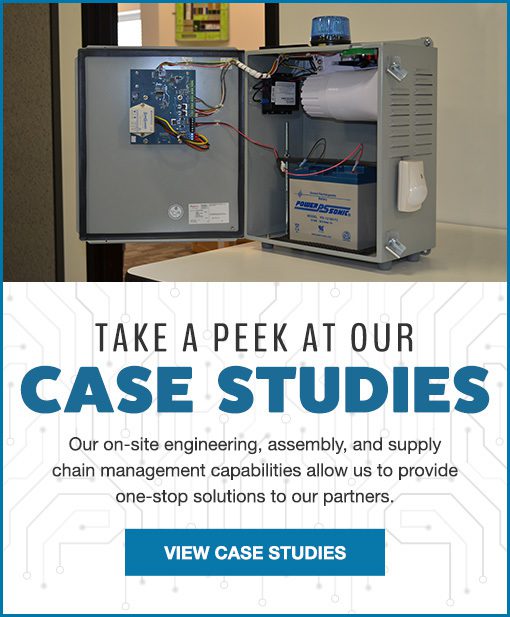
Process Failure Mode and Effects Analysis takes a close look at every step of the manufacturing process. The goal of it is to identify possible errors and risks from various sources. These sources can be considered the 6 M’s:
· Man
· Methods
· Material
· Machinery
· Measurement
· Mother Earth (Environment)
By following this methodology, all parts of the manufacturing process are analyzed. The following variables are given a score between 1 and 10, 1 being the least of concern:
· Severity – This examines the impact of an error in the process. A 1 has the lowest safety concern and a 10 is the most dangerous.
· Occurrence – This assesses the chance of a failure occurring. 1 would be the lowest chance and 10 represents the highest.
· Detection – This looks at the chance of a failure being detected. 1 represents the highest chance of detection and 10 represents the lowest chance.
· Risk Priority Number – This is an equation that calculates the severity, occurrence, and detection. When the resulting numbers are too high, corrective action is needed.
An effective PFMEA starts before production begins and continues on throughout the entire process of the manufacturing phase of your build.

Why use a PFMEA?
All steps of the PFMEA carefully analyze and identify every possible thing that could go wrong during manufacturing. This helps electronic manufacturers build in safeguards and plan for potential failures in all scenarios. It is especially helpful in avoiding errors during:
· Changes in an existing manufacturing process.
· When utilizing new technology and equipment.
· Relocating manufacturing to a new facility.
The PFMEA method allows electronic manufacturers to adequately plan for potential failures and put preventative measures in place. This will save time and money by avoiding errors and responding quickly in the case of any unforeseen circumstances.
Let Our PFMEA Work for You
No one sets out to fail, but planning to fail by not planning ahead is a major mistake.
Challenges arise every day in electronic manufacturing. Process Failure Mode and Effects Analysis (PFMEA) services provided by your manufacturing partner temper the impact of those challenges and lessen the effect on you and your product.
Levison Enterprises can help you discover the value of a PFMEA process. We always plan ahead and eliminate process errors where and when they can be identified. We pass the benefits of that on to you with affordability and respectable timelines. Contact our team today to see how Levison and its PFMEA services can benefit your next electronic manufacturing project.
Start Your Quote Now!