Optimal Strategies for Wire Harness Design and Assembly
Wire harnesses play a key role in various industries, acting as the central nervous system for electrical systems in everything from automobiles to aerospace equipment. Their design and assembly require meticulous attention to detail to guarantee functionality, safety, and durability. By adhering to best practices in routing, securing, labeling, and incorporating safety considerations, manufacturers can optimize wire harnesses for diverse industries and applications.
Laying the Foundation: Routing and Planning
Effective wire harness design begins with detailed planning. Proper routing is essential for ensuring the wires are organized and accessible for maintenance and repairs. Designers must map the most efficient paths, avoiding sharp corners and areas prone to heat or abrasion. Strategic routing minimizes wire strain, reducing the likelihood of wear and tear over time.
Computer-aided design (CAD) tools have revolutionized wire harness planning. With these, engineers can visualize layouts, simulate real-world conditions, and identify potential issues before production. This proactive approach allows efficient routing, reduces material waste, and accelerates assembly.
Securing the System: Fastening and Protection
Once routed, wires need to be properly secured to prevent movement and damage. Harnesses are typically anchored using clamps, cable ties, and brackets designed to withstand environmental factors like vibration, moisture, and extreme temperatures. Choosing the right securing materials is important; for instance, high-performance plastic ties work well in automotive applications, while metal clamps might be more appropriate for aerospace environments due to their heat resistance.
Another important element in securing is the integration of protective coverings, like braided sleeves or shrink tubing. These components shield the wires from environmental threats like abrasion, chemicals, and UV exposure, enhancing the overall longevity of the harness.
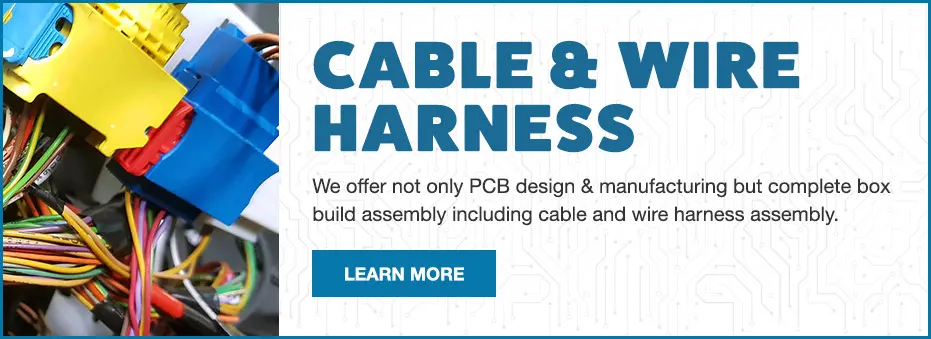
Labeling: Simplifying Installation and Maintenance
Precise and accurate labeling is a cornerstone of wire harness design. Each wire within the harness should be marked with unique identifiers to help with ease of installation and maintenance. Mislabeling or omitting labels can lead to costly troubleshooting or repair delays.
Modern wire harness assemblies often incorporate digital labeling systems, allowing for precise, durable markings that resist fading and smudging. Some manufacturers also include color-coded wires to further enhance clarity and organization. These measures simplify the installation process and reduce the potential for human error during repairs or upgrades.
Prioritizing Electrical Safety
Electrical safety is paramount in wire harness design, as failures can damage equipment and endanger lives. Designers must consider current-carrying capacity, insulation integrity, and temperature limits to mitigate risks. Using wires with appropriate gauge sizes confirms they can handle the expected electrical load without overheating.
Additionally, proper grounding and shielding techniques help prevent electrical hazards. Grounding provides the safe discharge of excess electrical energy while shielding protects the harness from external electromagnetic interference (EMI). These measures not only enhance safety but also improve the system’s overall performance.
Achieving Electromagnetic Compatibility
Electromagnetic compatibility (EMC) is a vital consideration for wire harnesses, particularly in environments where multiple electrical systems are operating nearby. Unchecked EMI can cause malfunctions or signal disruptions. Designers often incorporate shielding materials like aluminum or copper foil into the harness to achieve EMC.
The physical arrangement of wires also impacts EMC. Separating high-voltage and low-voltage lines minimizes interference. Twisting specific wires together, a technique known as twisted pairing, can further reduce susceptibility to EMI. By addressing these concerns during the design phase, manufacturers can ensure reliable operation in demanding environments.
Designing for Environmental Protection
Wire harnesses are frequently subjected to tough environments, where they endure extreme temperatures, humidity, and exposure to various chemicals. To guarantee durability, designers select materials that meet the specific environmental requirements of the application. For instance, thermoplastic insulation is often used in automotive harnesses due to its resistance to oil and grease, while aerospace harnesses may require flame-retardant materials.
Sealing connectors and joints is another key strategy for protecting harnesses in wet or dusty environments. Waterproof gaskets and seals prevent moisture ingress, which can lead to corrosion or short circuits.
In applications where harnesses face extreme heat, like engine compartments, heat-resistant materials and thermal insulation sleeves are essential. By tailoring materials and protective measures to the environment, manufacturers can enhance the reliability and lifespan of wire harnesses.
Streamlining Assembly for Efficiency
Efficient assembly processes are essential for meeting production timelines and maintaining quality. Prefabricated components, like modular connectors or pre-crimped terminals, can significantly speed up assembly. Manufacturers often rely on jigs or fixtures to hold wires in place during assembly, ensuring precision and consistency.
Automation is also becoming increasingly prevalent in wire harness manufacturing.
Machines can accurately perform tasks like wire cutting, stripping, and crimping, reducing labor costs and minimizing human error. However, skilled technicians remain essential for final inspections and adjustments, ensuring the harness meets all specifications.
Testing and Validation
Every wire harness should undergo comprehensive testing to confirm its functionality and safety before leaving the factory. Continuity testing guarantees electrical connections are intact, while insulation resistance testing checks for potential leaks and short circuits. Advanced diagnostic tools can also simulate real-world conditions to identify potential issues before deployment.
Validation is particularly important in aerospace and medical equipment industries, where harness failures can have severe consequences. Thorough testing guarantees adherence to industry standards and assures end users of the product’s safety and reliability.
Looking Ahead: Innovations in Wire Harness Design
As technology advances, the wire harness industry continues to evolve. Lightweight materials, like aluminum and advanced polymers, are gaining traction in aerospace and automotive applications to reduce weight and improve fuel efficiency. Similarly, the rise of electric vehicles and renewable energy systems drives demand for specialized harnesses that can handle higher voltages.
Smart wire harnesses, equipped with embedded sensors, represent another exciting development. These harnesses can monitor their condition and provide real-time feedback on performance, enabling predictive maintenance and reducing downtime.
Embracing Future Trends in Wire Harness Design
Optimal wire harness design and assembly require a delicate balance of precision, safety, and adaptability. By prioritizing proper routing, securing, and labeling techniques while addressing factors like electrical safety, EMC, and environmental protection, manufacturers can create reliable, high-performance harnesses for a wide range of applications.
As the industry continues to innovate, adopting advanced materials and innovative technologies will further enhance the capabilities of wire harnesses, paving the way for more efficient and sustainable electrical systems.
Make sure your wire harnesses are designed and assembled with precision, safety, and reliability. At Levison Enterprises, we combine innovative techniques with rigorous quality control to deliver solutions tailored to your industry’s exacting demands. Ready to elevate your systems with precision-crafted wire harnesses? Contact Levison Enterprises today to learn how we can support your next project.
Start Your Quote Now!