Mitigating Common PCB Assembly Challenges
The desired outcome in printed circuit board (PCB) manufacturing is to deliver a fully assembled and functional circuit board in the least amount of time. It may sound simple enough, but unfortunately there are many opportunities for mistakes and problems to occur during the PCB assembly process. You can reduce your risk of a mishap occurring by choosing the right assembly team for your project. Look for an ECM partner that has the experience and knowledge needed to eliminate common PCB assembly challenges.
Supply Chain Issues
One of the most common problems in PCB assembly is supply chain issues. When your design is completed without considering the availability of parts, you’re taking some major risks, like higher prices, low stock, and counterfeit components.
Reduce your risk of running into supply chain issues by partnering with the right ECM partner. This benefits you in more ways than one because a proactive ECM partner offers vetted suppliers they can trust for counterfeit mitigation and accurate part forecasting. They likely have a well-developed network of suppliers to work through any supply chain issues that might arise.
Irregular Size or Shape of Board
If the size or shape of your board is irregular, this could lead to a longer timeline and an increase in cost.
Avoiding this common problem is easily solvable by hiring an ECM partner with an on-site engineering team who can streamline and optimize your design to incorporate standard components, ultimately saving you time and money.
Engineers understand that your PCB components should be designed with manufacturing in mind and can quickly identify potential issues and make necessary adjustments and modifications to your design as it moves through the stages.
Inaccurate Solder Paste Application
A solder paste printing process is incredibly detailed and complex, requiring special attention. The solder paste printing must be precise to ensure lasting quality. The volume of solder and alignment are critical and difficult to maintain as PCB components have changed and the solder paste is increasingly hidden from view.
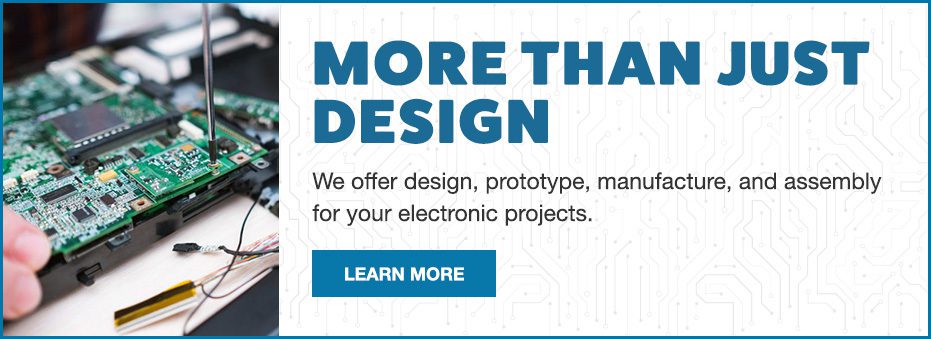
Due to the complexity of the process, defects in solder joints are an all-too-common problem in PCB manufacturing. However, you can eliminate the occurrence of an inaccurate solder paste application by relying on expert inspections from a skilled PCBA team. They can detect defects like high or low paste volume and clogged stencil apertures before the component placement process to avoid expensive reworks. The cost of rework to fix faults post reflow is much higher than the cost of fixing these faults before reflowing, so it’s much more effective to have a highly skilled inspection team on your side from the start.
Manufacturing Defects
Manufacturing defects are another common reality with PCB assembly, so it’s important to choose an ECM partner who uses automated optical inspection (AOI).
Automated optical inspection uses an autonomous camera to scan devices for defects, including missing components or quality issues. This method of automated visual inspection is preferred because it’s non-contact and can be implemented anytime throughout the assembly process. Until recently, AOI was assigned to post-production to identify faulty PCBs so they could be reworked, but now AOI is available at any stage of PCB assembly.
Many visual inspections that AOI scans for, such as scratches, incorrect or missing components, inaccurate soldering, and stains can also be detected by manual human inspection, however, the AOI does it faster and with more accuracy.
Choosing a Qualified Assembly Team is the Best Way to Eliminate Mistakes
Choosing a qualified assembly team with decades of experience is your best defense in eliminating mistakes. You can trust the experts at Levison Enterprises to deliver precise designs for a seamless manufacturing process. Contact us for a quote on your next PCB assembly.