Integrated Systems in Aerospace: Electronic Contract Manufacturing for Modern Aircraft
The aerospace industry is reaching new heights, with integrated electronic systems playing a critical role in modern aircraft and spacecraft design. These systems aren’t just components—they’re the backbone of cutting-edge capabilities, from reliable communication and data handling to robust power supply and propulsion. Working with an electronic contract manufacturer (ECM) equipped to meet the industry’s exacting standards can be transformative. With ECM experience, you’re not just adding electronics; you’re enhancing every function, allowing your designs to meet the demands of extreme environments and high-stakes missions. Together, these innovations open up possibilities that continue to elevate aerospace engineering and redefine what’s achievable.
Unique Challenges in Aerospace Electronic Manufacturing
All industries have their unique challenges in integrated systems. The primary goal in aerospace electronic contract manufacturing is to create aircraft systems that are more efficient, safer, and more advanced than those that came before.
With an increased focus on reducing carbon footprints, one of the challenges the aerospace industry has faced in recent years is developing more efficient systems that require less fuel and energy without a reduction in performance. Using lightweight materials and optimized design with integrated systems has helped aerospace engineers achieve these goals.
Another challenge is the high regulation in the industry. It is no surprise that this industry has stringent standards, as any failure has the potential to be catastrophic. Electronic contract manufacturers who work with these integrated aerospace electronic systems understand the regulations and have testing and quality control measures in place to make sure they are compliant.
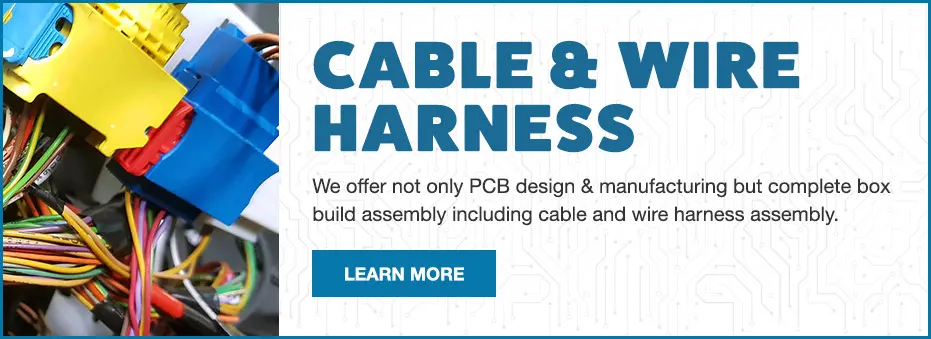
Cable and Wire Harness Systems
Cable and wire harness assemblies create a path from one PCB to another, connecting several points with breakouts moving in different directions. Cable and wire harness systems have had some safety risks when used in aerospace engineering due to the potential to fail with an electronic malfunction. However, new developments in cable and wire harness systems have undergone rigorous testing, demonstrating they are now safe to use in many aerospace environments. The wire harness design will strictly follow procedures from electric design, geometric routing, and configuration within the aircraft. Because there is a lot of complexity when installing cable and wire harness systems for use in aerospace technology, having an experienced electronic contract manufacturer is essential to meet the vast number of requirements that address potential safety and functionality issues. Mechanical, structural, and electrical issues must be addressed.
Box Builds for Integrated Systems
Box builds involve assembling multiple PCBs that will be connected via wiring and enclosed to protect the electronic components. Box builds include the fabrication of the PCBs, the installation of PCBs into the enclosure, and the connection of all components to form a complete system for the aircraft.
Box builds are designed to minimize weight and the structure of the components can reduce safety risks to nearly zero. The box build assembly serves as a protective enclosure for the electronic components to shield the PCB from external contamination which can come from dust and moisture that may damage the device. Custom enclosures can be efficiently designed to enhance functionality and protection; therefore, precision in box builds is paramount, particularly in integrated systems in aerospace electronic devices.
Microelectronic Systems
Microelectronic systems combine sensors, actuators, and controllers to create intelligent devices, making them essential in the aerospace industry. By enhancing the computational power of these systems, the development of smart technologies becomes easier, and unlocks new capabilities.
They’re especially well-suited for optical and sensory systems, both of which are heavily relied on in aerospace applications. Designed for harsh environments like extreme temperatures and high vibrations, microelectronic systems offer significant advantages in navigation, reducing size, weight, and operational costs compared to traditional systems. In flight control, they improve aerodynamics by reducing drag, enhancing turbine and compressor performance, and opening up new possibilities in aerospace engineering.
Choosing the Right Aerospace Electronic Contract Manufacturer
The right electronic contract manufacturer is key to quality aerospace electronic PCB assembly, especially with integrated electronic systems. First, the electronic contract manufacturer you look to partner with should have the appropriate certifications, including AS9001, as this will ensure the team working on your electronic systems will have testing and quality assurance practices in place. It is best to look for a domestic, turnkey ECM partner with a team of on-site engineers experienced in DFM analysis and in developing working prototypes to check durability, functionality, reliability, and optimal design. A domestic facility, instead of using an overseas ECM, will have the right processes to meet your strict regulations. In addition, these ECMs can help provide an optimized design that will be durable for the harsh operating environments that your device is likely to face. Choosing a turnkey facility with onsite engineers ensures that there will be a reduced risk of errors in communication throughout the process and that any design issues can be handled promptly.
Working with an ECM experienced in implementing integrated electronic systems can help take aerospace engineering to the next level. When the electronic system is designed to the highest standards, it will meet all necessary requirements and regulations. These systems can handle vibration and extreme temperatures while using an efficient design that can help reduce the carbon footprint of the aerospace industry.
As an experienced ECM, Levison Enterprises is AS9100 certified by NSF-ISR. Our vast industry knowledge and on-site engineers bring a lot to the table. Our innovative design assistance can help you bring an exciting, reliable device to market. Contact us today to learn more about how we can help you get your current project over the finish line.
Start Your Quote Now!