How to Start Your Reverse Engineering Project
There is no need to scrap a product that doesn’t work properly or is obsolete. Give it new life with reverse engineering. Reverse engineering is a way to duplicate a product, subassembly, or component and find out what once made it tick. This is especially handy when you don’t have documentation or original drawings for your PCB assembly.The process involves deconstructing the product to reveal its design and discover what makes it work. It is also a great way to check the design and prototype of a brand new product you hope to bring to market. Of course, like with any other project, you need to know where to start. Here are some tips to get you on your way with reverse engineering:
Check the Basics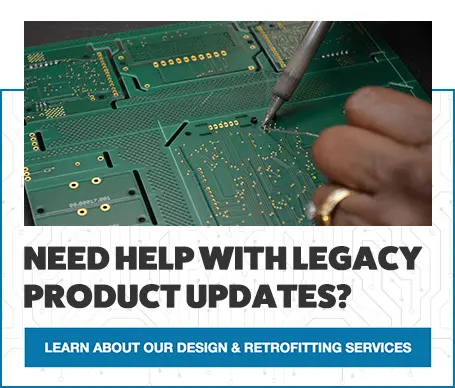
Occam’s Razor states: “The simplest solution is almost always the best.” It is wise advice, but easily overlooked. Start your reverse engineering with the basics. Look at your wiring and connections to make sure the proper amount of power is sent to the proper places. If too much power is being directed, it could overload your circuit. Also check to see that you are getting power. Are your batteries dead? Seems silly to ask, but it’s easy to miss the obvious when you’ve worked hard on a product and now it doesn’t work. Reverse engineering gives you another way to look at your project, and sometimes a fresh perspective is all it takes.
Know Your Intent
You need to determine what you want to achieve as you begin the reverse engineering process. Start with identifying the product’s end-use and work from there. The reverse engineering process becomes very lengthy and tedious when you don’t keep the end-use in mind. You may not need to capture and re-create every little component, but focusing on what it will be used for can shorten and simplify the reverse engineering process. The key here is efficiency.
Check for Changes
Knowing ahead of time if any changes need to be made to your project will affect your approach to reverse engineering. There are different methodologies for different circumstances. If no changes to the product are planned, you can move forward without any worries, however, if changes are planned you must take extra care in the modeling process. You need to make allowances for modification and/or additional features. With reverse engineering, all of the components flow together to get to the source of the problem. When you don’t allow room, it can mess up the sequence when you make changes. This is where mistakes can easily be made and destroy the entire reverse engineering process. This may result in starting over from square one, and costing you valuable time and money.
Email SalesSweating The Small Stuff
Some of these steps may seem small, but a small thing can hold back your design. Sweating the small stuff will ensure your design is the best it can be. If you’ve done all of this and you are still stuck, it might be time to gather your files and find a second set of eyes take a look at it. Be sure to seek out an ECM that has certifications, on-staff engineering, project management, and treats you like a partner. The right ECM will be able to use reverse engineering to create a 3D CAD (Computer Aided Design) model for use in your design system.
If you are in need of a top-notch ECM, look no further than Levison Enterprises. Our experienced team of experts can reverse engineer your project and find the solutions you need to make it successful. The dedication to our high-quality certifications and standards sets us apart as an electronic contract manufacturer and is reflected in our partnerships with our customers. Contact Levison Enterprises today.