How to Mitigate Risk and Save Money on PCBA
More companies are turning to outsourcing electronic contract manufacturing (ECM) to save money and reduce time to market. However, this decision shouldn’t result in compromising quality.
As part of the newest revision of the quality management system, risk-based thinking asks companies to consider what risks they face in various manufacturing processes. This includes planning phases for both the company and for products and services and during management processes such as corrective actions. Risk-based thinking asks companies to examine what triggers action.
Identifying risks is a job for risk management. Where risk-based thinking involves an approach to the whole business, risk management focuses on identifying risks, determining actions that will mitigate those risks, and then tracking those actions. Risk-based thinking has not eliminated risk management. Instead, it has expanded the areas businesses might consider risks as an overall quality management system.
To ensure you’re choosing the proper electronic contract manufacturer to partner with, consider these factors:
Holding Certifications
Certifications are proof that an ECM has a high expectation for quality. Working with a manufacturing partner that has taken the time to earn and maintain industry certifications ensures your electronic project will meet or exceed your industry standards. Only certified ECMs will have the space, equipment, and skills required for high-quality electronic manufacturing.
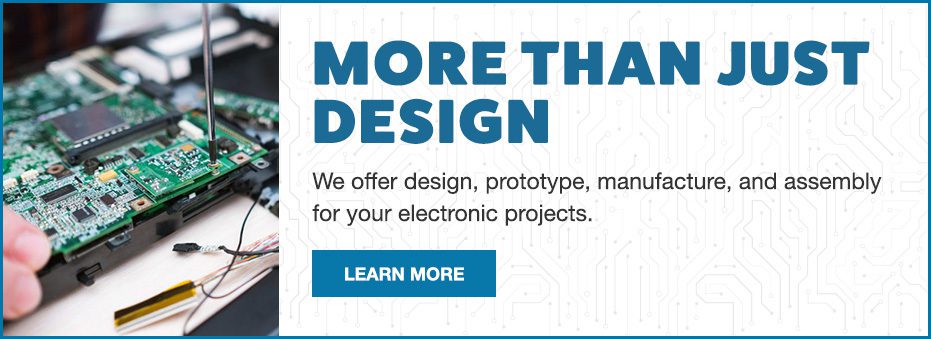
Practicing Counterfeit Parts Mitigation
Since counterfeit parts can be difficult to distinguish from legitimate components, it’s essential to partner with an ECM who has an established mitigation process already in place. This means they developed policies and procedures for avoiding counterfeit components, including how to:
- Avoid purchasing suspected counterfeit parts
- Handle and track incoming and outgoing parts
- Manage and dispose of suspected counterfeit parts
A reliable ECM partner implements counterfeit avoidance and management training programs, including:
- How to inspect parts and identify counterfeit components.
- Training to all employees handling parts.
Communicating directives efficiently ensures everyone understands the problem to adequately address it, including employees that order, receive, handle, inspect, and ship parts, and management.
PFMEA
Process Failure Mode and Effect Analysis (PFMEA) is a proactive tool to identify, evaluate, and prioritize any system’s potential weaknesses or failure modes. From its early stages of development with NASA, the PFMEA has evolved into an industry-accepted methodology used across many fields, from pharmaceutical to military to automotive.
Manufacturers use Process Failure Mode Effects Analysis (PFMEA) to detect potential failures rooted in the physical process of producing a part. Each process step is carefully analyzed to identify everything that could go wrong.
Vetted Supply Network
Having a vetted supply network at your disposal is essential to ensuring a quality product. If you use non-vetted suppliers, you risk parts being incorporated into your product that is low quality and possibly counterfeit. Partnering with an ECM with a vetted supplier network will help with parts procurement, ensuring all components have been tracked through an established supply-chain management process. With a vetted supply network, you can feel confident the parts are legitimate and of high-quality.
Design Capabilities
An ECM partner offering a complete lineup of design services and capabilities from a team of in-house engineers provides a quick turnaround for time-sensitive projects without sacrificing quality. This allows streamlined designs even for the most complicated projects. Designs can be incorporated into high-speed multi-layer boards. The right engineers are experienced in CAD modeling and various industries, including medical devices, defense, food safety, aerospace, and government projects. DFM analysis is crucial for delivering the most cost-effective, streamlined, and efficient design. You need engineers who understand how to incorporate DFM into your PCB design for the highest level of quality.
Turnkey Shop
A turnkey partner, or one overseeing your project from design to delivery, is the best choice. Having your project completed under one roof minimizes the chances of something getting missed, overlooked, or lost in communication during the project. The risk of human error is the highest when the project passes from stage to stage, so keeping the stages in one facility reduces this risk.
Domestic Partner
Choosing the cheapest option will almost always cost you more in the long run. Cutting corners means materials may not come from vetted suppliers, standards might not be met, and the experts you counted on might disappoint you. Using overseas outsourcing could expose you to communication pitfalls, security challenges, incorrect certifications, missed deadlines, manufacturing errors, counterfeit parts, and more, so it’s not worth the risk. Instead, looking for a domestic ECM partner for a more seamless process and reliable supply chain is best.
Start Your Quote Now!Choose Your ECM Partner Carefully
Finding a partner who is merely able to complete part of your project isn’t enough. Finding a turnkey, domestic ECM partner dedicated to completing government projects and prepared to handle any special requirements is the right partner for your project. If ever there was a time to be selective, this is it. Contact Levison Enterprises today for a quote.