How to Improve PCB Manufacturing Lead Times With an Electronic Manufacturer
As the saying goes, “time is money” and that’s certainly the case when talking about manufacturing lead times. Design engineers are being asked to design and bring to market more new products in less time. One way to combat shrinking design cycles is to outsource the fabrication and assembly of the printed circuit boards (PCBs) to an experienced electronic manufacturer, as PCB’s are a core element found in nearly all electronic products.
As engineers continue to design smaller, more complex PCBs, it is nearly impossible to produce boards in-house anymore. However, hiring the wrong ECM partner to handle this critical component can cause significant delays and increase project costs.
Your project’s overall lead time has many factors:
- Component lead time. Component shortages persist, affecting common components like capacitors and resistors, as well as specialized ICs for automotive systems. Designers will be aware of the component availability and lifecycles.
- Material lead time. It is always essential to optimize material selection for your board, which should be based on PCBA design types. However, due to supply chain delays, this includes recognizing when a standard material like FR-4 that is more readily available can suffice.
- Process lead time. Finally, your ECMs process can influence how long it takes to manufacture your boards. If you use a separate fabricator and assembler instead of a turnkey manufacturer, you are responsible for sourcing and procuring components and managing the logistics of the manufacturing stage, and this can create delays.
Look for an ECM Who Has What You Need
You can improve your PCB lead times by hiring a turnkey ECM partner who provides all services from start to finish. However, not all ECM partners are created equal, so it’s essential to hire an ECM who has what you need.
Design Services
Look for an ECM offering PCB design services. An experienced turnkey ECM includes in-house design and engineering teams focusing on collaboration with clients to create functional, efficiently designed electronic products. They should offer robust design capabilities using the latest cutting-edge software, applications, and equipment.
Design for Manufacturing (DFM) Strategies
Proper Design for Manufacturing (DFM) analysis requires competent and thorough testing, and access to the latest prototyping technologies and analytical tools. The end goal of DFM analysis is to find a product design involving the least amount of complexity in the manufacturing of the different components. Modern electronic devices are extremely complex, so a DFM analysis can help identify ways to trim excessive materials, producing better streamlined products at a lower price point.
Engineering Team On-Site
Having in-house engineers is beneficial for PCB design and manufacturing. An extra set of eyes on your PCB design can help streamline the design and improve on your ideas. Look for an ECM with in-house engineers on-site from the onset to help in mechanical design, electronic design, and software design.
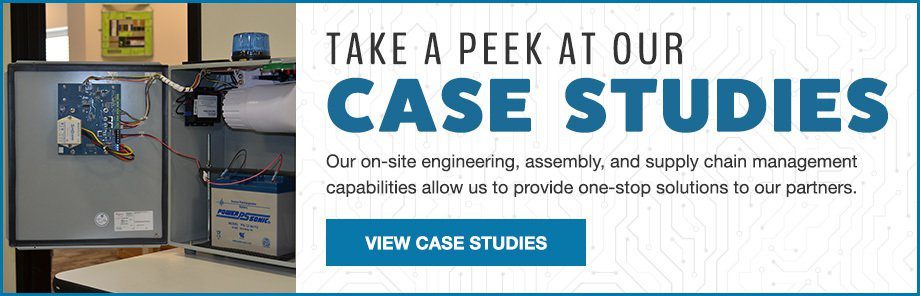
Prototyping Capabilities
Rapid electronic prototyping helps clients create cost-effective designs with minimal chance of needing to redesign or redo, which can impress potential investors with innovative ideas. Prototyping is a necessary stage of the manufacturing process, as it’s after design and before production, so there is a window where you, along with your ECM can take a thorough look at the design and components of your project. A prototype allows your project to move from the theoretical to concrete stage and is your opportunity to identify and address potential problems.
Broad Industry Experience
The best ECM partner is one with an extensive history in the industry or industries like yours. An established turnkey shop produces quality work. Having on-site engineers, using vetted suppliers, holding relevant certifications, and understanding the intricacies to provide complete turnkey service from start to finish are all things you will find in an good experienced electronic design and manufacturing partner.
Established Counterfeit Parts Mitigation Processes
A counterfeit electronic component is an imitation, unauthorized, or modified electronic component that is sold and presented as a legitimate component. It can also be a used component that’s been altered to look new. Counterfeit parts are often subject to product malfunction and failure, including the possibility of short circuits, electrical shocks, fires, and equipment failure. Counterfeit parts can be detrimental to your company’s reputation as they often don’t work as designed. Therefore, when choosing an ECM, it’s imperative they have an established counterfeit parts mitigation process in place to prevent counterfeit components from infiltrating your final product.
A PFEMA (Process Failure Mode and Effect Analysis) Tool
In electronic contract manufacturing, it’s nice to think failure isn’t an option, though that’s easier said than done. The right ECM goes that extra mile to protect your products by employing a process called a PFEMA or Process Failure Mode and Effect Analysis. PFEMA is a proactive tool to identify, evaluate, and prioritize potential weaknesses, or failure modes, in any given system. It’s used by manufacturers to detect potential failures rooted in the physical process of producing a part. Each step of the process is carefully analyzed to identify every possible thing that could go wrong.
Why Choose Levison Enterprises?
When you partner with Levison Enterprises, you will notice the difference in quality, flexibility, and savings that comes from working with a single, turnkey electronic contract manufacturer. Let the experts at Levison Enterprises put our experience and commitment to client satisfaction to work for you. Contact us today for a quote.
Start Your Quote Now!