How DFM Can Affect Your Bottom Line
Design for Manufacturing (DFM) involves optimizing parts and component design to ease manufacturing and assembly. This approach to product design aims to minimize manufacturing costs while maintaining or improving product quality, functionality, and reliability. DFM merges the design requirements of a product with its production method, resulting in custom-molded, close-tolerance parts that meet or exceed industry standards.
This part of the product development cycle can take days or weeks, depending on the complexity of the design. DFM should be implemented early in the development process. Neglecting this part of the process results in not catching manufacturability in time, leading to multiple design repetitions, increased expenses, and product flaws.
In highly regulated industries, like medical technology, DFM is essential. Even a minor tweak to a product after launch can take months to implement because it must comply with stringent industry regulations. DFM presents ways to optimize manufacturing before it begins.
How Can DFM Save You Money?
One of the most significant benefits of design for manufacturing is reduced cost of production. DFM simplifies manufacturing processes, reduces material costs, improves efficiency, minimizes prototyping iterations, and enhances product quality and reliability. By incorporating DFM principles, manufacturers can achieve cost savings and deliver high-quality products more effectively.
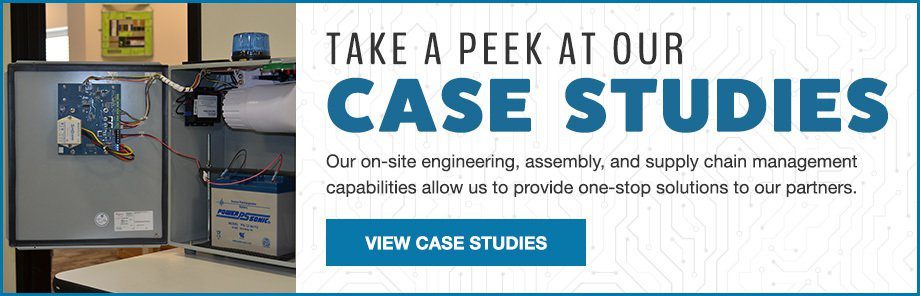
Streamlined Design for Fewer Parts
An optimized design may reduce the processing steps, eliminate redundant design features, simplify assembly, and lower the number of connectors or fittings needed for the finished product.
It is essential to choose your parts when designing electronics carefully. First and foremost, the manufacturing process will be much easier if you streamline your design and use fewer parts. This will also reduce the risk of errors and save you money.
Standardize Parts for Better Parts Accessibility
You can also increase your design success and save money by using standardized parts for better parts accessibility. They are much less expensive than custom components, and much easier to source. In addition, using standard parts will make your design easier to update and reproduce in the future.
Tracking the availability of your components while designing is also a good idea. Parts obsolescence can make even the most carefully crafted design useless. Forecasting the risk of a part becoming discontinued and estimating when that will happen can prevent a pause in manufacturing and give your design firm time to fabricate a custom component or redesign it altogether to avoid further interruptions.
Easier to Manufacture
Design for Manufacturing focuses on making the manufacturing process more streamlined. By eliminating super-specialized or overly complex processes, DFM helps reduce manufacturing costs and minimizes the occurrence of errors.
When DFM is implemented, the design is optimized to ensure that it can be easily produced using standard manufacturing techniques and equipment. This eliminates the need for costly and specialized processes that may require specialized machinery, extensive training, or additional resources.
Simplifying the manufacturing process not only reduces costs but also decreases the likelihood of errors or quality issues. By eliminating overly complex steps or intricate designs that are prone to errors, manufacturers can achieve higher levels of consistency, efficiency, and overall product quality.
Less Assembly Required
DFM includes fewer fasteners and less assembly required. Part of easier manufacturing is optimizing material and labor. If a product can be designed with fewer screws, fasteners, and adhesives, your time and production costs go down.
Design for manufacturing includes fewer hands. Every time a part must be touched, turned, flipped over, etc., it slows down. Symmetrical parts and other design elements added during DFM can limit these touch points.
If possible, the DFM process will make it so your assembly only has to move your product in one direction. This is determined by how parts can be added to your product, so carefully considering this will keep your manufacturing process moving smoothly.
Fewer Compliance Issues
Design for manufacturing results in fewer compliance issues. Standard, tested parts and an eye on the end product’s needs (including compliance) all lead to a better, more efficiently produced product. Ultimately, this is the goal of design for manufacturing.
Less Time to Market
All the above leads to less time to market. Since the design for manufacturing catches and removes mistakes before production, the result is a higher quality product that gets to market sooner.
Start Your Quote Now!Why Choose Levison Enterprises?
It is always tempting to dive headfirst into the manufacturing of your product. Design can feel tedious and even unnecessary, but design for manufacturing can result in lowered costs, time, and compliance issues.
Levison Enterprises uses design for manufacturing as part of our range of services to bring our customers quality products with the highest built-in efficiency. Contact us to discuss how we can help you build a better device.