FDA Regulations and Electronic Manufacturing for Medical Devices
The healthcare industry continuously evolves, with technological advancements pivotal in enhancing medical treatments and patient care. Electronic medical devices, from diagnostic tools to life-saving equipment, have become indispensable in modern healthcare. Yet, the development and production of these devices are regulated by stringent guidelines established by the United States Food and Drug Administration (FDA). For electronic manufacturing companies like Levison Enterprises, ensuring compliance with these regulations is paramount to producing safe and effective medical devices. In this article, we’ll delve into the key FDA regulations that impact electronic manufacturing for medical devices and explore how Levison Enterprises navigates these regulations to deliver high-quality products to market.
Understanding FDA Regulations for Medical Devices
The FDA oversees medical devices to guarantee their safety, efficacy, and quality. For electronic medical devices, the regulations are particularly rigorous due to the complexity of their design and functionality. The regulatory framework for medical devices encompasses various stages of development, manufacturing, distribution, and post-market surveillance. Key regulations that electronic manufacturers must adhere to include:
- Quality System Regulation (QSR): QSR, commonly referred to as Good Manufacturing Practices (GMP) for medical devices, sets forth criteria for the procedures, facilities, and controls employed in the design, production, packaging, labeling, storage, installation, and maintenance of all finalized medical devices. Adhering to QSR guarantees the consistent production and management of electronic medical devices under established quality criteria.
- Premarket Notification (510(k)) and Premarket Approval (PMA): Medical device manufacturers might need to send in a premarket notification or get premarket approval before they can sell the device in the US, depending on its classification. The 510(k) clearance is applicable for moderate-risk devices substantially equivalent to a legally marketed predicate device. Meanwhile, PMA is necessary for high-risk devices with a notable risk of illness or injury.
- Unique Device Identification (UDI) System: The UDI system requires labeling medical devices with unique identifiers to enhance traceability and facilitate adverse event reporting, recalls, and post-market surveillance. Compliance with UDI requirements helps improve patient safety and streamline device identification and tracking across the supply chain.
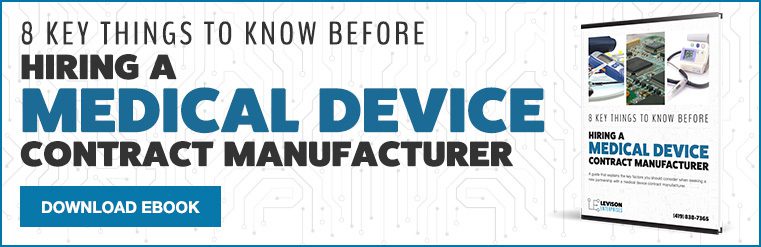
Levison Enterprises’ Continual Commitment to Compliance
At Levison Enterprises, adherence to FDA regulations is ingrained in our quality management system (QMS) and manufacturing processes. As an electronic manufacturing services (EMS) provider specializing in medical devices, we prioritize regulatory compliance to meet the highest safety and reliability standards. Here’s how we ensure compliance with FDA regulations:
- ISO 13485 Certification: Levison Enterprises is ISO 13485 certified by NSF-ISR, underscoring our commitment to maintaining a robust QMS tailored to the specific requirements of the medical device industry. ISO 13485 certification demonstrates our adherence to quality standards and regulatory requirements throughout the product lifecycle.
- Robust Quality Management System: We have implemented a comprehensive Quality Management System (QMS), encompassing procedures for design control, risk management, document control, supplier management, and corrective and preventive actions. Our QMS ensures that every manufacturing process step is meticulously documented and executed to meet FDA requirements.
- Cross-Functional Collaboration: We foster collaboration among multidisciplinary teams comprising engineers, quality assurance specialists, regulatory experts, and manufacturing personnel. This collaborative approach allows us to integrate design controls, risk management, and software validation seamlessly into the product development lifecycle, ensuring compliance while promoting innovation and efficiency.
- Comprehensive Documentation: We thoroughly document our manufacturing processes, quality control procedures, and regulatory compliance measures. Documentation is essential for demonstrating compliance with FDA regulations and facilitating audits and inspections by regulatory authorities.
- Supplier Quality Management: We collaborate with trusted suppliers and vendors who adhere to FDA regulations and uphold quality standards in their manufacturing processes. Our supplier quality management program ensures that components and materials used in medical devices meet stringent requirements for safety, performance, and reliability.
- Regulatory Experience: Our team includes regulatory affairs professionals who stay abreast of evolving FDA regulations and industry best practices. By staying informed and proactive, we navigate regulatory challenges effectively and ensure timely compliance with new requirements.
- Continuous Monitoring and Improvement: Maintaining compliance with FDA regulations is a perpetual endeavor, and we consistently monitor shifts in regulatory standards to adjust our practices accordingly. We invest in employee training and professional development to ensure our team remains abreast of the latest regulations and industry standards. Additionally, we conduct regular internal audits and assessments to identify areas for improvement and implement corrective actions proactively.
- Validation and Testing Protocols: Before commercial release, all our electronic medical devices undergo rigorous validation and testing procedures to verify their safety, efficacy, and performance. Per FDA guidance and industry best practices, we conduct thorough risk assessments, usability studies, and software validation tests. By validating our products comprehensively, we mitigate risks and ensure regulatory compliance.
In the world of electronic manufacturing for medical devices, compliance with FDA regulations is non-negotiable. Levison Enterprises recognizes the importance of adhering to these regulations to uphold medical device safety, efficacy, and quality. We surpass regulatory standards by utilizing our ISO 13485-certified quality management system, thorough documentation practices, risk management techniques, supplier quality oversight, and regulatory proficiency. By prioritizing compliance and quality, we empower healthcare innovators to confidently bring life-saving technologies to patients worldwide.
Why Partner with Levison Enterprises?
Are you seeking a reliable partner for the electronic manufacturing of medical devices while ensuring compliance with stringent FDA regulations? Look no further than Levison Enterprises. We provide a comprehensive answer to your manufacturing needs, supported by our demonstrated commitment to essential FDA regulations such as QSR, design controls, risk management, and software validation. Our robust Quality Management System, cross-functional collaboration, and commitment to continuous improvement guarantee the delivery of safe, effective, and high-quality medical devices.
Let us be your trusted partner in navigating the regulatory landscape and bringing innovative healthcare solutions to market. Contact Levison Enterprises to explore how we can help with your electronic manufacturing needs and guarantee adherence to FDA regulations.
Start Your Quote Now!