Ensuring Accountability Through Traceability in Medical Device Manufacturing
Some industries are more highly regulated than others. The medical and healthcare device industry is one of the most highly regulated, as medical devices, particularly those implanted in patients or worn to monitor and treat serious health conditions, must be safe and effective and cause health improvements rather than putting them at additional risk. To ensure that medical devices are safe and effective, electronic contract manufacturers who design and build PCBs and electronic components must have high-quality assurance standards and traceability in their manufacturing processes. To stay compliant with FDA regulations and industry standards, all medical devices brought to market must be traceable throughout their life cycle.
Why is Traceability So Important in Medical Device Manufacturing?
All medical devices must be manufactured to the highest standards to ensure patient safety. Medical device traceability ensures that all medical devices, materials, and components can be tracked from the initial prototyping phase through the delivery and use in healthcare settings. This will help reduce the risk of counterfeit or defective devices entering the supply chain and being used with patients. In the event of a recall or another issue with a medical device, traceability will help healthcare providers act quickly and efficiently to protect their patients.
The FDA classifies medical devices. Class II and Class III devices that require a tracking order are devices that will be implanted into a human body for more than one year, be intended to be a life-sustaining or supporting device, or will have serious adverse health consequences in the event of a device failure, such as automated or wearable defibrillators, permanent pacemakers, mechanical heart valves, or continuous ventilators. These medical devices require a written and fully detailed standard operating procedure report with the methods for following the device through distribution. This SOP must also include a quality control method that includes auditing procedures.
Accountability Through Traceability
Manufacturers have three working days to provide information about a device before distribution to a patient, including the exact location and status of the device in the distribution process. Manufacturers have ten working days to provide the information if the device has already been delivered. This traceability ensures that manufacturers can quickly and effectively respond to potential issues and take immediate corrective action. This traceability will also help medical professionals identify which patients use these devices and track any changes in their medical condition. To prepare for a recall, manufacturers must perform an audit of their traceability procedures and tracking methods every six months for the first three years and yearly for the remaining life of the device. The audit will ensure that the traceability method can efficiently and accurately collect the essential information and communicate that to all involved parties.
Documentation and Record Maintenance
The entire process of medical device manufacturing should be documented. Any high-quality ECM who works with medical devices should have an established and effective record-keeping system to demonstrate compliance at every stage of the process, including component traceability. Electronic contract manufacturers should have vetted suppliers to source the most appropriate and practical components and mitigate the risk of counterfeit components. By maintaining this documentation for every stage of the process, regulatory audits can be performed effectively, and clear, traceable evidence of compliance with FDA regulations can be ensured.
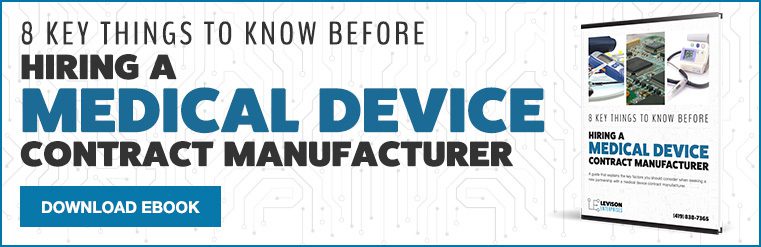
Choosing the Right Electronic Contract Manufacturer for Medical Devices PCBs
Working with a turnkey, domestic electronic contract manufacturer is paramount for ensuring accountability and regulatory compliance in medical device manufacturing. Not every electronic contract manufacturer has the same quality control practices. When choosing an ECM for a medical device, you need to ensure that the partner you choose will allow you to meet all regulatory requirements while still producing a high-functioning, reliable device. One of the first things to look for is the certifications your ECM has obtained and maintained. ISO 13485 is one of the most important for medical device manufacturers. This certification defines the quality management systems that must be in place for medical devices and equipment during the manufacturing process.
Your ECM should be knowledgeable in medical device manufacturing and understand the industry laws, regulations, and guidelines required for such a highly regulated industry. To be compliant, your ECM needs experience working in the medical device industry and will have a network of vetted suppliers that can provide component traceability throughout the entire manufacturing process. Having an on-site engineering team is essential, as they can work with suppliers to reverse engineer and design the PCB with verified, high-quality, and readily available components rather than searching for components in short supply or – worse – using components that may be counterfeit. Your ECM should be ready to answer all your questions about compliance with industry standards and regulations during your initial meetings, including component traceability.
Compliance is critical in medical device manufacturing. A practical, high-quality medical device can make a significant difference in a patient’s life facing serious health challenges, but with that responsibility comes great accountability. To ensure that medical devices are helping, rather than harming, the patients who rely on them, the electronic contract manufacturer takes on that responsibility, working with the design team to create a high-quality, highly effective device that will be safe for patient use. Finding the right electronic contract manufacturer is the key to accountability through traceability.
Why Partner with Levison Enterprises?
In medical device manufacturing, accountability through traceability is essential. At Levison Enterprises, we understand the gravity of our role in ensuring patient safety and regulatory compliance. With a steadfast commitment to thorough documentation, strict quality control, and adherence to FDA regulations, we guarantee traceability at every stage of the manufacturing process. From initial prototyping to distribution and beyond, our focus on component traceability and diligent record upkeep ensures that every device meets the highest safety and efficacy standards. Partnering with Levison means choosing accountability, reliability, and peace of mind for manufacturers and patients. Join us in safeguarding the integrity of medical devices and making a meaningful impact on healthcare outcomes. Contact us today for more information.
Start Your Quote Now!