Enhancing Efficiency and Quality in Box Build Processes
Box build assembly represents the critical stage where the components of your product come together in a finished, functional unit. While you may already be familiar with the intricacies of circuit board production, the challenge often lies in ensuring that the entire assembly process is efficient, timely, and consistently high in quality. Box builds encompass everything from wiring and subassemblies to packaging and final testing, making their optimization essential to maintain competitiveness in today’s fast-paced market.
If you’re seeking ways to improve your box build processes, you’re not alone. Businesses like yours depend on skilled manufacturing partners like Levison Enterprises to streamline production while safeguarding intellectual property and delivering top-notch products. Below, we explore strategies that can enhance efficiency and quality in box build assembly.
Optimizing Workflow Design
A well-structured workflow is at the heart of efficient box build assembly. By analyzing and refining each stage of production, you can significantly reduce lead times while ensuring quality remains intact.
- Mapping Out Processes: Begin by creating a detailed process map that outlines every step from materials handling to final testing. This helps identify bottlenecks and inefficiencies.
- Strategic Workstation Layouts: Arrange workstations to minimize unnecessary movement and facilitate a seamless flow of materials. Proximity between related tasks reduces downtime and improves communication among team members.
- Cross-Training Employees: When workers are skilled in multiple tasks, it reduces dependence on specific individuals and improves overall flexibility in the production line.
Workflow optimization doesn’t just cut down on delays. It also provides a solid foundation for implementing advanced strategies like lean manufacturing, discussed below.
Implementing Lean Manufacturing Principles
Lean manufacturing focuses on eliminating waste to enhance efficiency and reduce costs. Adopting these principles in box build assembly can have a transformative impact on your operations.
- 5S Methodology: Organize workspaces by sorting, setting in order, shining (cleaning), standardizing, and sustaining. This approach improves safety, reduces errors, and boosts productivity.
- Kanban Systems: Use Kanban boards to control the flow of materials and prevent overproduction. Matching supply to demand ensures resources are used efficiently.
- Minimizing Waste: Identify and eliminate areas of waste, whether it’s excess inventory, unnecessary motion, or idle time between tasks.
Lean strategies help streamline production without compromising on quality, creating a balanced approach to meeting deadlines and exceeding customer expectations.
Leveraging Automation in Assembly
Automation has become an integral part of modern manufacturing, allowing companies to perform repetitive or complex tasks with precision and speed. For box builds, incorporating automation can enhance consistency while cutting down on labor-intensive processes.
- Automated Testing Systems: Automated inspection and testing systems catch defects early in the process, reducing the need for rework later. A McKinsey study reports that companies embracing automation can see productivity gains of 10-20%.
- Robotic Assembly: Robotics can perform delicate tasks like wire soldering or component placement with exceptional accuracy, reducing the risk of human error.
- Material Handling Automation: Automated conveyors and robotic arms ensure components are delivered to the right place at the right time, further minimizing delays.
While automation requires upfront investment, the long-term benefits in terms of efficiency, quality, and scalability often outweigh the initial costs.
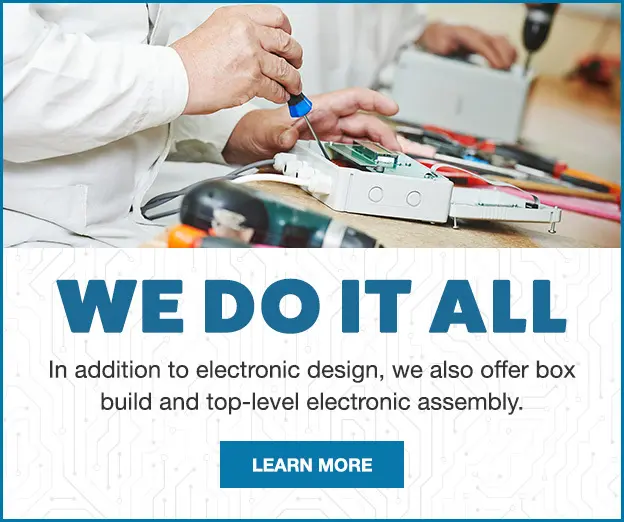
Quality Control as a Cornerstone of Success
Maintaining high-quality standards throughout the box build process is non-negotiable. Robust quality control protocols not only prevent costly mistakes but also enhance customer satisfaction and trust.
- In-Process Inspections: Conduct inspections at various stages of assembly rather than waiting until the end. This allows for quick identification and resolution of issues.
- Statistical Process Control (SPC): Use data-driven techniques to monitor process variations and ensure consistency in production outcomes.
- Error-Proofing Tools: Employ fixtures, jigs, and other tools that prevent incorrect assembly or misplacement of components. Visual aids like color-coded labels further reduce errors.
Quality assurance becomes even more critical when working with a manufacturing partner. Levison Enterprises’ turnkey approach integrates quality control into every phase of production, so you can trust that your product meets industry standards.
Reducing Lead Times Through Collaboration
Collaboration with the right partner can significantly reduce lead times in your box build processes. Effective communication and strategic alignment between your team and your manufacturing partner ensure smoother operations.
- Comprehensive Bills of Materials (BOMs): Providing a detailed BOM minimizes the risk of missing components and streamlines procurement.
- Vendor-Managed Inventory (VMI): Partnering with suppliers who offer VMI programs can reduce delays by ensuring critical components are always in stock.
- Kitting and Pre-Assembly Services: Suppliers that pre-assemble components or provide kitting services can accelerate production by delivering ready-to-use parts.
Collaborative efforts lead to better coordination and shorter turnaround times, enabling you to meet tight deadlines without sacrificing quality.
Building a Culture of Continuous Improvement
Continuous improvement is a mindset that drives innovation and efficiency in box build assembly. Encouraging feedback, analyzing performance metrics, and remaining open to change are key elements of this approach.
- Tracking Key Performance Indicators (KPIs): Measure and evaluate metrics like defect rates, cycle times, and production throughput to identify areas for improvement.
- Regular Audits: Periodic reviews of processes help uncover inefficiencies and set the stage for enhancements.
- Employee Empowerment: Encourage team members to suggest improvements and participate in decision-making. Their on-the-ground experience often provides valuable insights.
A culture of continuous improvement ensures your processes remain agile and responsive to evolving demands.
Efficiency and Quality
Partnering with a skilled manufacturer like Levison Enterprises can make a world of difference in optimizing your box build assembly. When you’re ready to elevate your box build processes, contact us for a free quote. Learn how our turnkey solutions can help you succeed.
Start Your Quote Now!