Does Your Project Need a Flexible PCB?
Though they only occupy a small percentage of total circuit boards produced worldwide, flexible printed circuit boards are on the verge of driving that percentage up. As product engineers and manufacturers push the boundaries of technology, the advantages that a flex PCB can deliver are becoming more and more apparent.
Advantages in Application
In almost any application that utilizes cutting-edge technology, a flex PCB gives designers and manufacturers the ability to capitalize on their numerous benefits. Today, you can find flexible PCBs in:
- Consumer electronics
- Motion-detecting technology
- Aerospace and avionics
- Semiconductors
- Medical devices and technology
Engineers working in these fields have discovered what flex PCB innovation can bring to a project. They have allowed them to reduce cost while simplifying design, and reduce overall weight, all while being resistant to water, shock, high temps, and corrosion.
As more manufacturers and design engineers realize these advantages, expect to find the flex PCB in more and more electronics that can benefit from their application.
Flex PCB Permutations
The innovation of the flex PCB has led to a couple of different forms, each blending the best aspects of efficiency, design flexibility, and cost-reduction.
“Flex to install” blends both flexible PCBs and their rigid counterparts to create a PCB where flexibility is necessary when installing the component only. Once in place, the flex to install unit remains stable throughout product life.
By contrast, “dynamic flex” PCBs are designed to flex and bend throughout a product’s use. While flex to install PCBs are made only with the consideration that the PCB will flex once during initial install, dynamic flex units must be designed with the knowledge that the bending and flexing could happen hundreds of times during the life of the component.
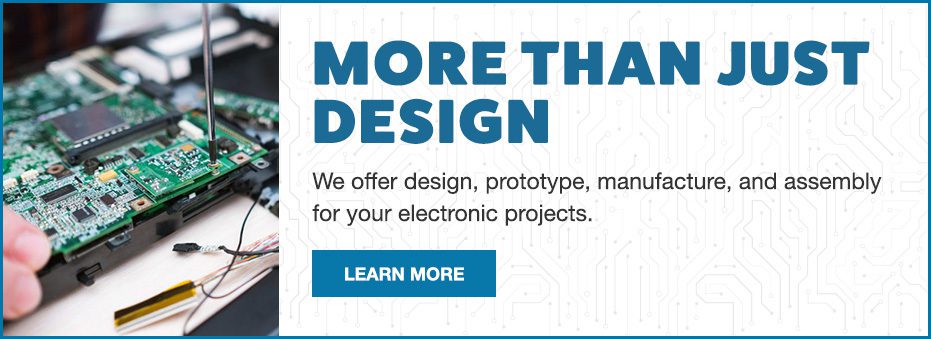
The most demanding applications call for the rigid-flex PCB, designed to withstand the most hostile of environments. While they are typically the most expensive type of flex PCB, the advantages they deliver actually make them the most cost-effective.
Rigid-flex PCBs can survive high levels of shock and vibration and survive thousands of bends or flexes, while reducing the overall product weight. Rigid-flex PCBs allow increased circuit density while decreasing necessary assembly operations that might be involved with a regular circuit board.
Across the board, flexible PCBs allow designers to design an end product to best fit its application, instead of forcing them to work the end product around the PCB. It gives engineers the freedom to design a product as optimally as possible. While flex PCBs are often more expensive than their rigid, board-based cousins, the other advantages they bring to design and manufacture can easily balance out those concerns.
At Levison Enterprises, we utilize the latest in both traditional and flex PCB technology to deliver exactly what your project needs. Contact us today to learn more about how our turnkey process can deliver for your specific ECM needs.
Start Your Quote Now!