Design for Manufacturing (DFM) in Defense Electronics: Enhancing Efficiency
In the world of defense electronics, where precision, reliability, and speed are essential, the significance of Design for Manufacturing (DFM) cannot be overstated. Design for Manufacturability (DFM) is a methodology focused on maximizing manufacturing efficiency during the product design stage, guaranteeing cost-effective production with minimal errors.
In the defense sector, where the stakes are high and margins for error are slim, implementing DFM principles is not just a best practice—it’s a necessity.
Understanding DFM in Defense Electronics
Before getting into the specifics of DFM in defense electronics, it’s crucial to understand the foundational principles that form the basis of this methodology. DFM is based on designing products to streamline manufacturing without sacrificing quality or performance. By considering manufacturing constraints and requirements early in the design phase, engineers can identify potential issues and make necessary adjustments to streamline production.
The Basic Principles of DFM
Utilizing the fundamental principles of Design for Manufacturability (DFM) can optimize your assembly processes and product quality.
- Simplify the design: Complex designs often lead to complex manufacturing processes. Simplifying the design whenever possible can reduce production time and costs.
- Minimize the number of parts: Every additional component increases manufacturing and assembly complexity. Minimizing the number of parts not only simplifies production but also enhances reliability.
- Standardize components: Standardizing components where feasible can streamline procurement and reduce lead times. It also simplifies inventory management and decreases the risk of supply chain disruptions.
- Design for ease of assembly: Considering ease during product design can notably decrease production time and labor expenses. Modular designs and standardized interfaces facilitate faster assembly processes.
- Optimize material selection: Selecting readily available, cost-effective, and suitable materials for the intended application is essential for efficient manufacturing. Additionally, optimizing material usage can minimize waste and reduce environmental impact.
The Importance of DFM in Defense Electronics
In the defense sector, where precision and reliability are non-negotiable, DFM is critical in ensuring that electronic devices meet the rigorous standards demanded by military applications. Here’s why DFM is essential in defense electronics:
Cost-Effectiveness
Defense projects often operate within tight budgets, and cost overruns can have profound implications. By optimizing the design for manufacturing, defense contractors can minimize production costs without compromising quality. This is especially crucial for large-scale projects where even small savings per unit can translate into significant overall cost reductions.
Rapid Prototyping and Iterative Development
The iterative nature of defense projects demands rapid prototyping and quick iteration cycles. By incorporating DFM principles during the initial stages of the design phase, engineers can accelerate prototyping and shorten development timelines. This agility is essential for responding promptly to evolving threats and requirements.
Reliability and Durability
In defense applications, reliability and durability are critical. Electronic devices must withstand harsh environmental conditions, extreme temperatures, vibration, shock, and electromagnetic interference. By designing for manufacturing, engineers can ensure that components are securely mounted, connections are robust, and the overall design is rugged enough to withstand the rigors of military use.
Supply Chain Resilience
The defense industry is highly dependent on complex and often fragile supply chains. Disruptions in the supply chain can delay projects and compromise national security. By standardizing components and optimizing material selection, defense contractors can reduce their reliance on specialized suppliers and mitigate the risk of supply chain disruptions.
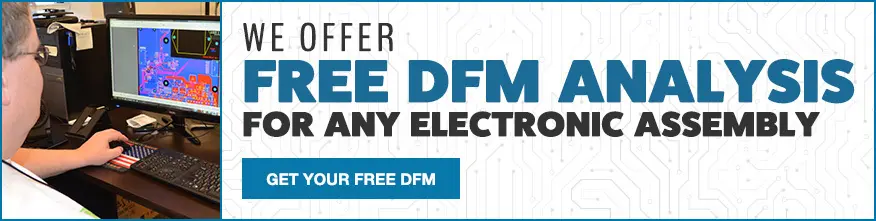
Unique Challenges in Defense Electronics Manufacturing
While the principles of DFM are universal, defense electronics manufacturing presents some unique challenges that require special consideration:
Compliance and Certification
Defense electronics must adhere to stringent regulatory standards and certifications. Compliance with standards such as MIL-STD-810 and ITAR (International Traffic in Arms Regulations) is non-negotiable. Designing for manufacturing involves ensuring that the final product meets all relevant regulatory requirements without compromising performance or reliability.
Security and Confidentiality
Defense projects often involve sensitive and classified information. Protecting intellectual property and preventing unauthorized access to proprietary technology is a top priority. Designing for manufacturing involves implementing robust security measures throughout the supply chain to safeguard sensitive information and prevent data breaches.
Long-Term Support and Maintenance
Unlike commercial electronics, which may have relatively short lifespans, defense systems are expected to remain in service for decades. Designing for manufacturing involves considering long-term support and maintenance requirements, including the availability of spare parts, repairability, and upgradability.
Conclusion
In defense electronics, where precision, reliability, and efficiency are crucial, Design for Manufacturing (DFM) is indispensable. By integrating DFM principles in the design phase, defense contractors can enhance manufacturing, cut costs, speed development, and ensure military-grade standards for electronic devices. With the ongoing evolution of technology and the increasing complexity of threats, the significance of DFM in defense electronics will inevitably escalate. Embracing DFM is not just about enhancing efficiency—it’s about safeguarding national security.
Why Choose Levison Enterprises?
As you navigate the complexities of defense electronics manufacturing, you must have a partner you can rely on to deliver excellence at every step. Levison Enterprises is that partner. With our expertise in defense-specific Design for Manufacturing (DFM), we’re dedicated to assisting you in efficiently achieving your objectives.
Utilize our cutting-edge manufacturing capabilities, industry-leading expertise, and dedication to quality to streamline production, lower costs, and guarantee superior reliability and performance for your defense electronic devices.
Don’t let manufacturing challenges hold you back. Move towards success by teaming up with Levison Enterprises. We’d love to discuss the specifics of your project and explore how we can tailor solutions to meet your requirements. You can count on Levison Enterprises to be your trusted partner. Contact us today to learn more.