Best Practices for Designing Efficient Box Build Assemblies
In the electronic manufacturing industry, efficiency is not just a desirable trait; it’s a critical component that can make or break the success of a project. Nowhere is this more evident than in box build assemblies, where the integration of various electronic components into a final enclosure occurs. Designing these assemblies for optimal efficiency requires careful consideration of several factors, including component placement and enclosure design. This article, will explore some best practices for designing efficient box build assemblies.
Understanding Box Build Assemblies
Before getting into best practices, it’s essential to grasp the concept of box build assemblies. A box build assembly integrates electronic components, such as printed circuit boards (PCBs), cables, connectors, and other hardware, into a final enclosure or “box.” This final product could be anything from a consumer electronics device to industrial machinery or medical equipment.
Best Practices for Designing Efficient Box Build Assemblies
Creating efficient box build assemblies requires a thorough understanding of how component placement, enclosure design, and manufacturing processes interact intricately. From early collaboration to leveraging advanced technologies, discover how these best practices for crafting streamlined and optimized box build assemblies can elevate the efficiency and effectiveness of your assembly processes.
Early Collaboration and Communication
Efficient box build assembly design begins with early collaboration and communication among all parties, including design engineers, manufacturing engineers, procurement specialists, and suppliers. By including everyone from the start, possible issues can be spotted and dealt with in the initial design stages, avoiding costly delays and revisions later.
Design for Manufacturability
Designing for manufacturability (DFM) is crucial for optimizing box build assembly efficiency. This involves designing components and assemblies with the manufacturing process in mind, considering factors such as component placement, ease of assembly, and access for testing and maintenance. Implementing Design for Manufacturability (DFM) principles can simplify the assembly process, reducing the likelihood of errors or defects.
Optimized Component Placement
Strategic component placement is critical to efficient box build assemblies. By organizing components logically, assembly technicians can minimize the time and effort required to assemble the final product. Additionally, thoughtful component placement can improve airflow, thermal management, and overall system performance.
Modular Design Approach
Adopting a modular design approach can enhance box build assembly efficiency by breaking the assembly into smaller, more manageable modules or subassemblies. This allows for parallel manufacturing processes, reduces assembly time, and simplifies troubleshooting and repair. Additionally, modular design facilitates more effortless scalability and adaptability, enabling swift adjustments to accommodate evolving project requirements or technological advancements.
Enclosure Design Considerations
The enclosure design plays a significant role in the efficiency of box building assembly. Enclosures should be designed with ample space for components, connectors, and wiring, allowing easy access and assembly. Additionally, consideration should be given to factors such as material selection, durability, EMI shielding, and environmental protection.
Standardization of Components
Standardizing components wherever possible can streamline the assembly process and reduce the need for excess inventory and tooling. Manufacturers can achieve economies of scale and simplify procurement, assembly, and maintenance processes using standard components across multiple products or projects. Moreover, standardizing components encourages better compatibility and smooth integration across different systems and platforms, ensuring they work well together.
Utilize Advanced Manufacturing Technologies
Leveraging advanced manufacturing technologies, such as automated assembly equipment, robotics, and additive manufacturing, can significantly improve box build assembly efficiency. These technologies can automate repetitive tasks, increase throughput, and enhance precision, resulting in faster production cycles and higher-quality products.
Continuous Improvement and Optimization
Box build assembly efficiency is not a one-time endeavor but an ongoing continuous improvement and optimization process. It’s essential for manufacturers to consistently assess their assembly processes, pinpoint opportunities for enhancement, and make adjustments to boost efficiency, quality, and cost-effectiveness.
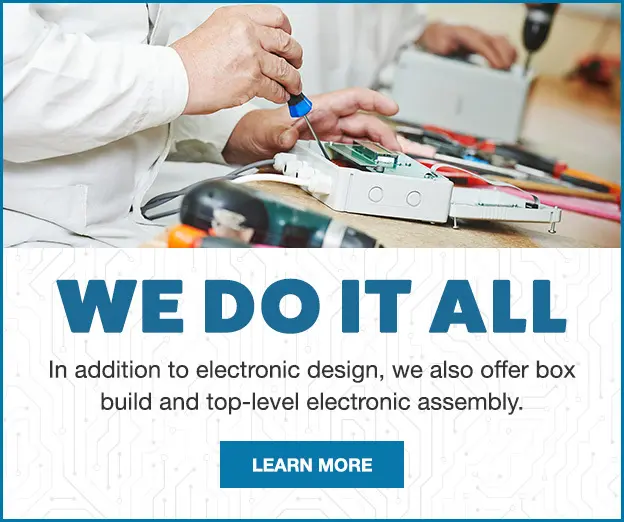
In Conclusion
Efficient box build assembly design is essential for maximizing productivity, minimizing costs, and quickly delivering high-quality products to market. By following best practices such as early collaboration and communication, designing for manufacturability, optimizing component placement, adopting a modular design approach, considering enclosure design, standardizing components, leveraging advanced manufacturing technologies, and embracing continuous improvement, manufacturers can achieve optimal efficiency in their box build assembly processes. Ultimately, this results in faster time-to-market, greater customer satisfaction, and a competitive advantage in the vastly evolving electronics industry.
Why Partner with Levison Enterprises?
Are you ready to take your box build assembly efficiency to the next level? Look no further than Levison Enterprises. With years of experience in electronic manufacturing services (EMS), Levison Enterprises offers a comprehensive range of solutions designed to optimize your assembly processes and drive success.
At Levison Enterprises, we understand the unique challenges of box build assembly and are committed to delivering customized solutions that meet your needs. From the first design consultation to the final product assembly, our proficient team collaborates closely with you at each phase to ensure a seamless and efficient process.
Our state-of-the-art facilities are equipped with cutting-edge technologies, such as automated assembly equipment and advanced robotics, enabling us to manage projects of any size or complexity. Our unwavering focus on excellence, reliability, and customer satisfaction establishes us as a dependable partner in electronic manufacturing.
If you’re striving to streamline your assembly process, cut costs, or enhance overall efficiency, Levison Enterprises has the expertise and resources to support you in achieving your goals.
Contact us today to learn how we can help your box build assembly needs and take your business to new heights. Let’s work together to make your vision a reality.