Avoid Supply Chain Challenges by Reverse Engineering Legacy Designs Through an Electronic Manufacturer
All manufacturers are struggling to meet the demands of their customers while dealing with supply chain concerns, which are impacting every industry. Choosing a domestic electronic manufacturer with on-site engineers is your best option to work through these disruptions through reverse engineering. By reverse-engineering your legacy designs, you can save time and money by not starting from scratch.
What is Reverse Engineering?
Reverse engineering is the process of taking a product apart in reverse order to study how it was put together, how it works, and why it works. Engineers can learn about the product’s build by “unbuilding” it. After the product is deconstructed, engineers can put the product back together and improve the design and functionality.
How Can the Reverse Engineering Process Help with Supply Chain Challenges?
Component shortages are a real concern right now. Supply chain challenges can completely derail your project, frustrating you and your customers. If your project is in PCB development and the components you need are no longer available, you may wonder if you need to start over. This is where reverse engineering can save your project. Reverse engineering has long been used to solve problems with function and design for print circuit boards.
As companies merge and legacy products are added to current production lines, prints and designs are often lost in the shuffle. Typically, you would use reverse engineering for a legacy product that is malfunctioning, but still has a life and the need for a complete redesign is unnecessary.
Sometimes fixing a legacy product is easier than trying to source parts for a newer design. This helps you combat the parts shortage by fixing your legacy products instead of waiting for the manufacture of projects that are still on hold due to supply chain issues.
Other Benefits of Reverse Engineering
In addition to handling the supply shortage, reverse engineering is always a good idea for legacy products. In older products, reverse engineering can help recreate design data and help the engineers understand how the product was initially designed.
While your legacy product may still work, reverse engineering allows the design team to help your legacy products improve and grow with the advances in parts and technology. Building a design from scratch is a time-consuming and expensive process, but reverse engineering can get you the benefits of a new product from the blueprints of an older tried and true one.
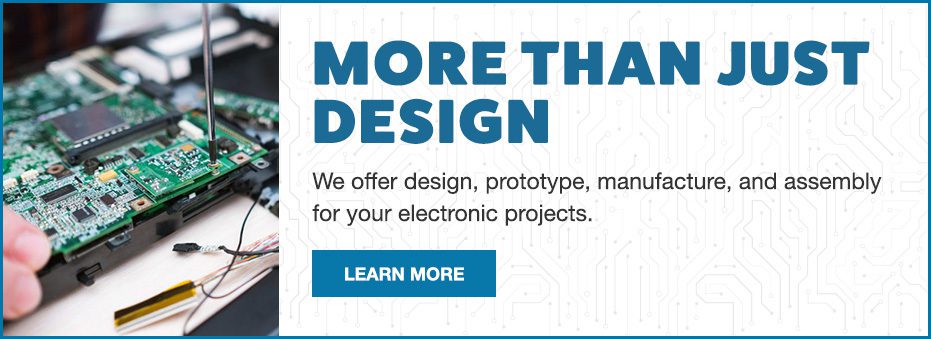
Having the engineers available in-house is critical to successful reverse engineering. When you are looking for an ECM partner to keep your project on track during parts shortages, finding a domestic, turnkey ECM is vital. These partners understand the supply chain concerns and how to protect your project development. The on-site engineers can step in and use their reverse engineering skills to ensure that your PCB can still be functional with the parts that are currently available, and in many cases, can even make your product function better than before.
Levison Enterprises is a turnkey, domestic printed circuit board manufacturer with a dedicated and experienced engineering team on site. Our vast industry knowledge and decades of experience lend well to challenging supply chain issues like those we are currently experiencing.
Our skilled team can help you design and build your product from the ground up. Have questions about which route is best for you? We can help with that too. Contact us to discuss your next project ideas with us today.