Applications and Advantages of Flexible PCBs in Medical Devices
Flexible PCBs are seeing increased use in electronic medical device manufacturing. Many medical devices now include printed circuit boards, and technological advancements have made these devices even more desirable among patients and the healthcare industry. Electronic contract manufacturers skilled in medical device manufacturing have been using flexible PCBs to streamline design, reduce weight, and increase the effectiveness of these medical devices.
What are the Most Common Applications in Medical Device Electronics?
With the advancement of medical technology, more devices are available to help patients manage their conditions. Flexible PCBs are used in medical wearables, such as health monitoring systems, such as devices intended to monitor blood sugar, activity tracking systems that can also monitor heart rate, respiration, and overall fitness, devices that can be implanted directly into the body, such as pacemakers, hearing-assist devices that can allow a microphone, battery, and DSP to be assembled into a compact package that will fit snugly and discreetly behind the ear, and diagnostic equipment such as the electronic components of CT scanners, MRIs, and ultrasound equipment, along with many other advancing applications. While some of these applications have been around for many years, advancements in technology provide increased accuracy, reliability, and functionality while reducing the device’s overall size.
Why the Move from Rigid PCBs?
Rigid printed circuit boards are the most cost-effective option for manufacturing, so they can be the desired choice when reducing the cost, which is the most crucial consideration. However, while the board is the right choice for other applications, its rigidity is not ideal for devices with size constraints or requiring greater movement during application. Many advanced medical device requirements are simply impossible when using rigid PCBs. Rigid-flex PCBs can be the right solution for specific medical devices, where the components can be mixed to allow the board to be folded or bent to fit into tight spaces and are more compact than true rigid PCBs. Still, even these boards cannot always meet the needs of many medical devices, specifically wearable ones.
Wearable Medical Devices Benefit From Flexible PCBs
One of the most essential components of designing a wearable medical device is getting the design small while not losing functionality. This can be a challenge for PCB manufacturers. In the past, size and flexibility were not significant considerations when developing medical electronics. Still, design changes must be made now that medical devices are miniaturized for easier wear. Using flexible PCBs can address this problem by allowing electronic contract manufacturers to reduce the device’s size and create a compact wearable that can provide the necessary health monitoring or assistance. Flexible PCBs work well with medical devices, as they can move alongside the device as it expands and contracts. With the advancements in flexible PCBs, medical devices can evolve to be more compact without losing functionality.
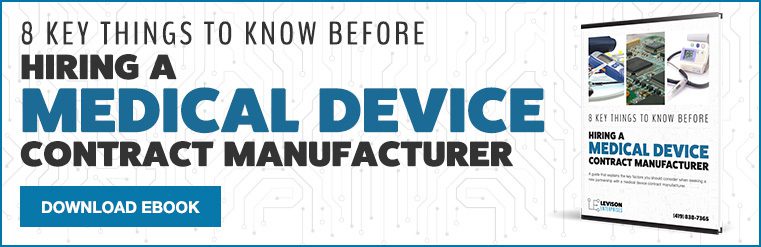
Flexible PCBs Save on Space and Weight
Small size is desired when it comes to medical devices. Increased weight is difficult in a wearable medical device and can be cumbersome in other electronic medical devices. Flexible PCBs can help, as they use thinner copper layers for insulation. While these thin layers provide the necessary flexibility, they have the added advantage of significantly reduced weight. Smaller and lighter devices that do not compromise quality, reliability, or functionality are an excellent benefit of using flexible PCBs. Implantable medical devices, hearing assist devices, and monitoring devices must be small for maximum patient comfort.
Flexible PCBs Have a High Degree of Reliability and Functionality
Medical devices must be reliable and function as designed, without room for error or failure. While failure in an electronic device is never considered a good thing, failure in an electronic medical device can be catastrophic for the patient. The highest potential point for failure in an electronic medical device is typically the point of connection. Using a flexible PCB minimizes connection points and simplifies the assembly of the device, significantly reducing and even eliminating the chances of interconnecting defects in the joints. The materials used for flexible PCBs are resistant to various environments and operations, minimizing the impact of shock or vibration. Some of what makes a flexible PCB more reliable are the uniform material thickness, uniform trace width, and spacing, as well as improved constants in connection points.
Finding an Electronic Contract Manufacturer with Experience in Medical Device Manufacturing and Flexible PCBs
During the development of a new or redesigned medical device, it is essential to partner with an electronic contract manufacturer with the right experience working with flexible PCBs in medical electronic manufacturing. When you are looking for an ECM with which to partner, look for a domestic, turnkey facility with on-site engineers with the proper certifications. Experience with flexible PCBs in similar applications to yours is critical for success.
The lightweight, reliable, and compact medical devices have given patients many benefits, and flexible PCBs have made those advancements and benefits possible. Working with a highly skilled and experienced team of engineers and manufacturers can help make the best use of flexible PCBs that still provide the highest quality, functionality, and reliability. Finding a team committed to high-quality electronic manufacturing with flexible PCBs can make many medical devices possible.
Why Partner with Levison Enterprises?
As you navigate the ever-evolving medical device manufacturing industry, consider Levison Enterprises’ expertise and commitment. We specialize in harnessing the potential of flexible PCBs to enhance your medical devices’ design, efficiency, and functionality. Our turnkey solutions and a domestic facility staffed by certified engineers ensure that your project meets and exceeds industry standards. Choose Levison Enterprises as your partner in innovation—where your vision for smaller, lighter, and more reliable medical devices becomes a reality. Contact us today to discuss how our experience with flexible PCBs can bring your next medical device project to the forefront of healthcare technology.
Start Your Quote Now!