Sustainable Approaches in Aerospace Electronic Manufacturing
The aerospace industry, long associated with cutting-edge technology and innovation, is increasingly focused on sustainability. As global concerns over climate change and resource depletion grow, this sector has embraced green practices to reduce its environmental footprint. This shift is particularly evident in aerospace electronic manufacturing, where companies are rethinking processes, materials, and technologies to align with sustainability goals.
Reducing Energy Consumption in Manufacturing
Energy efficiency is a key focus in aerospace manufacturing, particularly electronics production, which has historically involved energy-intensive processes. Companies adopt energy-saving measures at every stage, from design to final assembly. Advanced simulation tools allow manufacturers to optimize electronic designs to minimize energy loss. Meanwhile, facilities are increasingly powered by renewable energy sources like solar or wind to reduce their carbon footprint further.
In addition, manufacturers are leveraging automation and innovative factory technologies to improve production efficiency. These systems reduce energy consumption and waste by ensuring precise assembly and testing. For instance, smart sensors in production lines can identify inefficiencies in real-time, helping manufacturers refine their processes and make swift adjustments.
The Shift to Sustainable Materials
The choice of materials significantly impacts sustainability. In aerospace, electronic manufacturers are turning to eco-friendly options, like recyclable metals and biodegradable polymers, for components and packaging. These materials lessen the environmental burden and align with regulatory requirements for greener products.
Innovations in science have enabled the development of lightweight yet durable materials, which are vital for reducing aircraft weight. Lighter planes consume less fuel, directly lowering greenhouse gas emissions. This shift benefits the aviation industry and military and space applications, where weight reduction leads to better performance and cost efficiency.
Manufacturers are also exploring using conflict-free minerals and materials sourced through ethical supply chains in electronic systems. These practices guarantee sustainability is embedded in the manufacturing process and throughout the product lifecycle.
Designing for a Circular Future
One of the most transformative shifts in aerospace electronic manufacturing is adopting circular economy principles. This approach emphasizes designing products for longevity, repairability, and eventual recycling. Making components last longer and easier to upgrade helps cut down on waste in manufacturing.
For example, modular designs are becoming more prevalent, allowing individual components to be replaced or upgraded without discarding the entire system. This approach not only reduces waste but also lowers costs for aerospace operators, making sustainability a win-win.
Recycling programs can reclaim valuable materials like rare earth metals from decommissioned electronic devices at the end of a product’s lifecycle. Recovered materials can be reused in manufacturing, cutting the need for new resources and lowering the overall environmental impact.
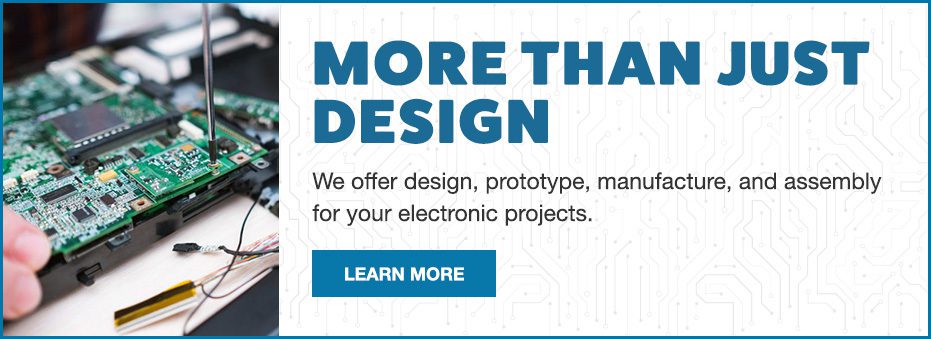
Green Technologies in Production
The integration of green technologies is reshaping how aerospace electronic devices are manufactured. One game-changing innovation is 3D printing, also known as additive manufacturing, which has rapidly grown in popularity. This technology allows for precise production with minimal material waste, making it an ideal prototyping and large-scale manufacturing solution.
Another breakthrough is using environmentally friendly adhesives and coatings, essential in protecting electronic components. Traditional chemical-based solutions often contain harmful volatile organic compounds (VOCs), but newer options are water-based or derived from renewable sources, ensuring a lower environmental impact.
The industry is exploring innovative cooling techniques for electronic systems. Conventional cooling methods rely on energy-intensive processes, but advancements like liquid cooling and phase-change materials offer more efficient and sustainable alternatives.
Waste Reduction Initiatives
Minimizing waste is another pillar of sustainable manufacturing. Aerospace electronic manufacturing involves rethinking everything from production scraps to packaging materials. Many companies are adopting lean manufacturing principles, which focus on eliminating inefficiencies and maximizing resource utilization.
Scrap reduction programs aim to repurpose leftover materials, like circuit board offcuts, into other products or processes. Similarly, digital manufacturing techniques, like computer-aided design (CAD) and computer-aided manufacturing (CAM), enable more precise material usage, drastically reducing waste.
Packaging is also receiving a sustainability overhaul. Recyclable and biodegradable packaging materials replace traditional plastics, aligning with broader corporate sustainability goals. By rethinking packaging, manufacturers are not only reducing waste but also enhancing their environmental credibility.
Working Together for a Greener Future
The move toward sustainability in aerospace electronic manufacturing isn’t happening in isolation. Achieving meaningful progress relies heavily on strong collaboration throughout the supply chain. Companies work closely with suppliers, customers, and regulatory bodies to set and meet sustainability standards.
Organizations like the International Aerospace Environmental Group (IAEG) are instrumental in fostering industry-wide collaboration. Sharing best practices and developing standard sustainability metrics help manufacturers align their efforts and accelerate innovation.
Additionally, partnerships with research institutions are driving breakthroughs in sustainable technologies. These collaborations, from developing new materials to optimizing energy efficiency, pave the way for a greener aerospace industry.
Meeting Regulatory and Consumer Expectations
Sustainability is no longer just a choice—it’s an expectation. Stringent environmental regulations require aerospace manufacturers to reduce emissions, manage waste, and ensure the responsible use of resources. Following these standards is key for entering the market and boosting brand reputation.
Consumers and stakeholders increasingly value sustainability. Airlines, for example, are under pressure to demonstrate their commitment to greener practices, which extends to the electronics and systems they deploy. Manufacturers prioritizing sustainability gain a competitive edge by aligning with these evolving expectations.
A Sustainable Future for Aerospace Electronics
The aerospace industry’s progression toward sustainability is profoundly reshaping electronic manufacturing. Manufacturers reduce their environmental impact by embracing energy-efficient processes, sustainable materials, and innovative technologies while driving operational excellence.
The commitment to green practices will grow stronger as the industry continues to evolve. By working together, fostering innovation, and aligning on a sustainable future, the aerospace electronics manufacturing sector is on track to build a greener, more responsible world.
Levison Enterprises for Sustainable Aerospace Solutions
Levison Enterprises combines sustainable practices with cutting-edge technology to design high-performance electronic systems tailored to your aerospace manufacturing needs. Our energy-efficient methods and innovative use of materials provide reduced environmental impact without compromising quality.
Let us help you meet your innovation goals with sustainable practices in your aerospace manufacturing. Contact us today to build a greener, more efficient future.
Start Your Quote Now!