Ensuring Patient Safety: Quality Control Measures in Medical Device Manufacturing
Your reputation is on the line every time a medical device with your name reaches a patient. You’ve poured time, effort, and resources into its development, only to feel a twinge of uncertainty when it’s time to partner with an electronic contract manufacturer (ECM). Will they uphold your standards? Will their processes meet the rigorous quality requirements necessary to protect patient safety?
It’s a tough decision, especially when you know the risks of cutting corners in this industry. The last thing you want is a product that compromises patient health—or your company’s trustworthiness. That’s why finding an ECM with a proven track record of precision, thorough quality control, and a commitment to continuous improvement isn’t just ideal—it’s essential.
Patient safety is paramount in medical device manufacturing. There is no use in bringing a product to market quickly if that product will be risky for patients. This is why finding an ECM that prioritizes quality control measures is key.
You want an ECM partner that understands and exceeds the stringent requirements of medical device manufacturing. It’s not enough for them to follow the basics; they must implement rigorous internal quality checks and adopt best practices at every step.
Every detail matters, from sourcing high-quality components from reliable suppliers to meticulous design, prototyping, and comprehensive testing. A partner committed to continuous improvement will ensure that each element is crafted with patient safety as the top priority, giving you confidence in the quality and reliability of your end product.
Design for Manufacturing is Critical at the Earliest Stages
Often, those who design medical devices aren’t concerned with manufacturability. When you choose an ECM that gets engineers involved from the beginning of the design process, the overall quality of the finished product will improve. The engineering team will take the device through a DFM (Design for Manufacturability) analysis and look at the parts, specifications, functionality, and tooling to make sure that the device is designed in a way that will make it successful. If an issue arises during the prototyping phase, on-site engineers will be well-versed in the design and can quickly make the necessary adjustments to keep the project on track.
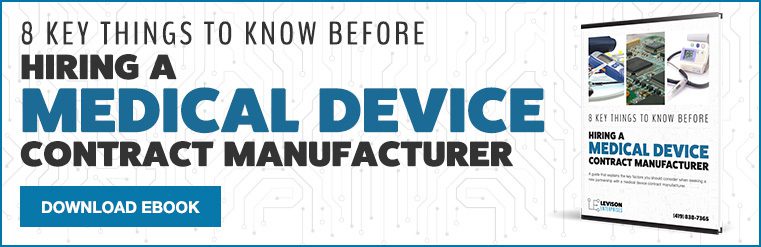
Quality Control Tools and Techniques
Failure mode and effects analysis, often called FMEA, reviews the components and assemblies to identify potential failures and their effect on the final product. The failure modes and effects are documented and used in a qualitative analysis for each component in the assembly. FMEA is often performed during the design and prototyping stage of the process, which will allow for any necessary adjustments to be made before a full-scale run. Having on-site engineers overseeing this process and making the required design adjustments is essential to quality control.
Quality Standards and Certifications
Electronic manufacturers are not required to hold any certifications. Anyone with the right equipment can set up shop as an ECM, and unless you are working with a highly regulated industry, you may wonder if it even matters. But if you want a quality product, especially a medical device where patient safety is a concern, you need to care about certifications. You will know that you have chosen a partner who holds themselves accountable, chooses high-quality suppliers, uses high-quality parts, has high organizational efficiency, and understands the regulatory requirements of every industry they manufacture for. Obtaining and maintaining these certifications shows a commitment to excellence. When choosing an ECM, look for one who holds various certifications. This can include:
- AS9100 – a commitment to maintaining a high-quality environment with product traceability–essential when vetting suppliers.
- ISO 9001 – ensuring customer satisfaction with a customer-centric approach to quality management.
- ISO 13485 – advanced capability in medical device manufacturing.
- IPC and J Standard Certification – soldering cables and circuit board assemblies experience.
- FDA Registration – adherence to the quality control necessary for FDA-approved devices.
Challenges in Ensuring Quality in Electronic Manufacturing for Medical Devices
In an ideal world, there would be no challenges to producing a high-quality device for medical use. Supply chain issues and cost constraints can create a roadblock during manufacturing. As mentioned above, when you have an ECM that uses DFM analysis during the prototyping stage, you can be well-positioned to avoid many of these challenges, as they will factor the supply chain into the design to make sure that all components come from vetted suppliers. DFM can work around supply chain issues and adjust product designs to fit your parameters. An ECM with onsite engineers who perform a DFM analysis can help you overcome many challenges you can potentially encounter during medical device manufacturing.
Benefits of a Domestic Turnkey Facility in Medical Device Manufacturing
Outsourcing electronic manufacturing overseas can offer many cost-saving advantages, but these can come at a hefty price. There are many drawbacks to partnering with an overseas manufacturer. Communication may be challenging due to time zones and language barriers, suppliers can be more difficult to vet, and product traceability can become an issue. Domestic partners understand medical device regulations and the importance of quality control, patient safety, and documentation of every product stage. In a domestic, turnkey facility, everything will be completed in one facility with no potential for quality measures to slip through the cracks.
We understand that quality control isn’t just a priority—it’s a responsibility, especially when lives depend on the products we manufacture. Our certified, domestic, turnkey electronic manufacturing services are built to deliver the reliability, precision, and safety your products demand. Partner with Levison Enterprises to guarantee your product is manufactured with the highest standards of quality and care. Contact Levison Enterprises today to learn how we can help you bring your vision to life with confidence and peace of mind.
Start Your Quote Now!