Big Benefits in Small PCBs: Innovation in Wearable Medical Devices
Wearable medical devices have seen incredible advancements over the past few years. Whether monitoring a chronic condition or tracking fitness, wearable medical devices can provide healthcare professionals with data to help them understand and treat their patients.
Real-time healthcare data and continuous monitoring can make a real difference in the healthcare industry, and manufacturers of this technology are working hard to keep up with the demand by miniaturizing the PCBs used in these devices.
Miniaturization can be achieved by using multi-layered flex PCBs made of lightweight materials. The advancement in wearable medical devices is directly related to advancements in PCB technology. As PCBs evolve, the possibilities for their use evolve with them.
Innovations in Wearable Medical Devices
Wearable medical devices include anything that patients can attach to themselves to collect health and fitness data. This can include activity trackers, implantable devices like pacemakers, blood pressure monitoring devices, biosensors, ECG monitoring devices, blood sugar measurement and tracking devices, insulin pumps, sleep monitoring devices, and hearing aids. Some of these devices are marketed directly to consumers interested in monitoring their health and fitness data.
In contrast, other devices are sold to medical professionals to provide them with a solution for gathering the data needed for a treatment plan. As wearable medical devices become more popular, manufacturers are working to make them more marketable to end users. It is usually about reducing the size, weight, and impact the device will have on daily life. The smaller and lighter a device can be, the more desirable it is to the wearer. Much of the device’s size depends on how small the electronic components can be while remaining functional, reliable, and effective.
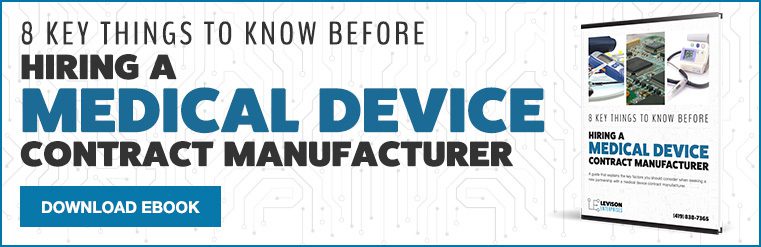
What Attributes are Needed?
Wearable medical devices, compared to other electronic medical devices, have their own distinct attributes that will make them both functional and efficient. Not only will they need to adhere to all regulatory requirements of medical devices, but they also need to function effectively while meeting the needs of a wearable device. This includes:
-
Flexibility
Flexible PCBs have exceptional bending and flexing ability. Because a flexible PCB can handle the expanding and contracting of a wearable medical device, it is ideal for this application. The flexible material can withstand the constant impact and vibration of human movement that rigid PCBs may not be able to handle.
-
Size
Before medical devices were designed to be wearable, size was generally not a concern. Early medical monitoring devices tended to be larger and more rigid than what is desired today. Compact size is key for a wearable medical device to be widely used today.
-
Weight/Comfort
In addition to a compact size, wearable medical devices must be extremely lightweight for the user’s comfort. Innovations in materials have allowed devices to meet these requirements. Thinner copper layers have allowed PCBs to be lighter and adapt to tighter spaces. In addition, the flexible material does not generate the same amount of heat as other PCBs, which also increases comfort for the wearer.
-
Safety
The safety of any medical device is paramount during design. There should be no potential for harm in any wearable medical device, including risks from a rigid board, a device that can overheat, or a device that may fail.
-
Communication
Since a wearable medical device will need to communicate with either the user or someone monitoring the data, all wearable medical devices include some form of communication within the design, which also will need to be adapted to the small size.
-
Environmental Resistance
A wearable medical device will be exposed to the same environmental elements as the user. Therefore, wearable devices need to be able to handle cold, heat, and water. While not every device will need to be submerged, exposure to moisture needs to be considered, and many wearable PCBs will need to be sealed or coated for water resistance.
-
Versatility
Depending on the use of the device, wearable medical devices need to be versatile and handle many different conditions.
Challenges in Manufacturing Wearable Medical Devices
The biggest challenge in manufacturing wearable medical devices is getting the device small enough to be comfortable for the wearer while retaining all the reliability, durability, and functionality necessary to be useful as a monitoring device. In addition, wearable medical devices are subject to significant regulatory requirements to ensure they are safe for use by patients. After navigating the size and weight restrictions and regulatory requirements, devices must be easy enough for consumers to use effectively. In the manufacturing process, all of these considerations must be addressed.
How Flex PCBs are Contributing to Innovations
Flex PCBs have solved many challenges when manufacturing wearable medical devices. As flex PCBs are smaller and lighter than rigid boards, they can meet many size and weight requirements without impacting the functionality. Flex PCBs can handle irregular and complex shapes with clever component placement and flexible circuits that will move with the user.
Small PCBs are making a big difference in advancing wearable medical devices. Many electronic contract manufacturers work with flexible PCBs to make innovations possible and avoid the design challenges associated with wearable medical devices. When looking for an ECM to manufacture your PCB for a wearable device, look for one with experience and certifications in medical device manufacturing to avoid headaches with regulatory bodies later on. If you’re looking for an ECM to partner with, we can help. With ISO 13485 certification from NSF-ISR and extensive expertise in medical device manufacturing, we’re equipped to give your medical device the competitive advantage it needs. Contact Levison Enterprises today for a personalized quote and let’s take the next step together.
Start Your Quote Now!