Continuous Improvement Initiatives in Electronic Manufacturing
An electronic contract manufacturer with a continuous improvement culture will always strive to enhance processes, product quality, and customer satisfaction. A commitment to continuous improvement can be demonstrated in how an electronic contract manufacturer monitors their policies, procedures, and growth. While state-of-the-art equipment is undoubtedly beneficial for a high-quality result, it is ultimately the overall culture of the facility and the dedication of those working on that equipment and technology that will genuinely drive excellence. When choosing an electronic contract manufacturer look into their continuous improvement initiatives to see their priority on growth.
Challenges in Continuous Improvement
Every electronic contract manufacturer should strive to have a culture of continuous improvement, and nearly all claim that they do. However, there are challenges to this culture that can be difficult to overcome. Cost constraints, supply chain issues, and other outside influences can occasionally make even an organization dedicated to quality assurance struggle. When outside influences pose challenges, high-quality electronic contract manufacturers are prepared to face them by implementing Design for Manufacturability analysis and prototyping phases, both of which can allow engineers to work around supply chain issues and budget constraints by altering designs to function well with readily available components that can fit any budget. Taking care of these potential issues early in the manufacturing process can help avoid the possible roadblocks that can compromise quality later in the process.
PDCA Cycle Can Drive Improvement
The PDCA cycle – for Plan-Do-Check-Act – is part of the assessment for obtaining AS9100 certification. Still, it is a simple model many organizations use to drive change and improvement consistently. Implementing this cycle can keep organizations from becoming complacent, particularly with issues that have arisen repeatedly. In a continuous model, ignoring potential matters is far less likely. When an organization implements this cycle, the likelihood of high-quality processes, procedures, self-checks, and results is increased. Process improvements will not happen only when someone has come in to evaluate but all the time. This model is the definition of continuous improvement. In the planning stage, potential risks are accounted for alongside a plan for what will be done. In the doing stage, solutions are tested, and data is gathered to demonstrate outcomes. In the checking stage, the first two stages are looked at more closely to see if the problems were there, if they could be resolved, and what might be changed in the future. This stage drives improvement, forcing the team to look carefully at the actions and results. Finally, necessary changes are implemented in the acting stage based on the data and the questions answered. This process will continue to repeat, creating the ultimate culture of continuous improvement.
Internal Quality Audits Keep Your Electronic Contract Manufacturer Accountable
Relying on outside oversight for quality assurance is a flawed strategy. When an electronic contract manufacturer only focuses on best practices when attempting to obtain a certification or meet someone else’s requirements, it becomes evident that the culture is not one of continuous improvement. In an internal quality audit, the electronic contract manufacturer is accountable only to themselves and their clients. While an outside organization may conduct the audit, the outside organization has no vested interest in the results, which the electronic contract manufacturer uses to identify areas where there may be gaps in policy, procedure, and other issues. Internal audits may focus on specific processes but on the process as a whole and what a client can expect to experience. After the findings are analyzed, the electronic contract manufacturer can take any areas of weakness, defect, uncertainty, or non-conformities and apply corrective action to address them. Even minor issues, when unchecked, can lead to major problems down the road, so identifying, remedying, and rechecking these potential issues is crucial to keep the standards high. With regular internal quality audits, the focus can be on identifying and adjusting quality control best practices to meet the desired outcomes.
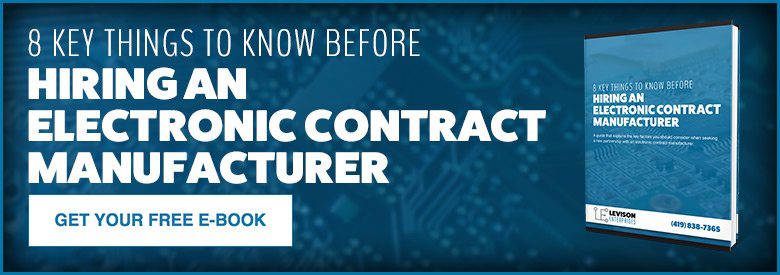
Choosing an Electronic Contract Manufacturer Who Makes Continuous Improvement a Priority
When you are in the market for an electronic contract manufacturing partner, look for an organization with a culture of continuous improvement. When discussing the project plan, begin by asking about certifications. Obtaining and maintaining these certifications demonstrates the ability to meet and exceed standards in policy and procedures. Beyond the certifications, look into the company policies on quality assurance practices, the frequency and results of internal audits, and the continuous improvement practices implemented. When an electronic contract manufacturer has a culture of continuous improvement, they can provide you with clear guidelines, data, and policies that reflect their commitment to maintaining the highest standards and quality assurance practices. During this initial meeting, it will be clear how high of a priority the electronic contract manufacturer makes their commitment to continuous improvement.
The highest quality organizations strive to hold themselves accountable rather than waiting for an outside organization to step in and force their hand. An electronic contract manufacturer who understands the industry’s challenges and plans to face them performs internal quality audits, and implements the Plan-Do-Check-Act cycle which holds itself to the highest quality standards. When you partner with an organization consistently challenging themselves to do better, you will know your project will succeed.
Why Choose Levison Enterprises?
In a landscape where electronic contract manufacturers strive to uphold the highest standards, Levison Enterprises stands out with its unwavering commitment to continuous improvement. As you navigate the complexities of choosing the right partner for your electronic manufacturing needs, consider the pivotal role of a culture prioritizing growth and excellence. At Levison Enterprises, our dedication to the PDCA cycle ensures that every phase of your project undergoes rigorous assessment and refinement, guaranteeing superior quality and reliability. By conducting regular internal quality audits and embracing a culture of perpetual enhancement, we hold ourselves to the highest standards, ensuring your project’s success. Choose Levison Enterprises for a partnership rooted in continuous improvement, where your vision meets unwavering dedication to excellence. Contact us today to learn more.