Cost-Efficiency: Strategies in Aerospace PCB Manufacturing
Technology in aerospace electronics is advancing rapidly, and keeping up with innovations during manufacturing is a challenge for many designers as they struggle to stay cost-efficient while still ensuring that these innovations function as designed. Aerospace electronics must be able to function in harsh environments, and failure can be catastrophic, so balancing high-quality manufacturing that meets all regulatory requirements with cost-efficiency can be a challenge.
Stay Cost-Effective by Optimizing Your Aerospace PCB Design
Optimizing the design of your PCB for aerospace applications is the primary key to reducing costs. All fundamental aspects of materials, circuit structure, and production process can be optimized in the design stage. A design for manufacturability (DFM) can be performed at this stage to ensure that the necessary components are readily available, the design can be optimized for the most efficient number of layers, and all specific performance requirements can be considered. A DFM analysis will be able to factor the cost of components into the design and consider the number of layers and connections that can drive up the material and manufacturing costs. In addition, complex designs often result in defects during the process, which can cause product delays and increased costs. A DFM analysis by a team of engineers experienced in aerospace PCB design and manufacturing can anticipate these issues and tweak the design to avoid them.
Prototyping Can Be a Cost-Efficient Way to Ensure Performance
The next stage after a DFM analysis should be a prototyping run. Developing a working prototype can quickly and effectively identify any current or potential design and functionality issues, which can be remedied before a full-scale production run. Having an on-site team of engineers to do the initial optimized design and then thoroughly test and inspect the working prototype will allow the engineers to make any design, layout, material, or functionality adjustments quickly at a relatively low cost. A combination of visual inspection and X-ray inspection can help identify surface defects, anomalies in thickness and warping, and the integrity of the inner layer circuits. Comprehensive testing on a working prototype is far more cost-effective than testing after a full-scale run.
Consider Volume and Delivery Time to Stay Cost-Efficient
Once the prototyping stage and any adjustments needed are made to the design, materials, and layout, the volume of the production run will impact cost. The larger the quantity in the full-scale run, the lower the cost per unit. When the testing is completed during the prototyping stage, the risk of potential errors compromising a large-scale run is significantly reduced, and mass production can occur with lowered concerns. Rather than producing in multiple batches, the economies of scale can be leveraged to reduce overall costs. In a similar vein, delivery time should also be considered. Rapid turnaround services have become more popular as many designers want to see their products to market as quickly as possible, but this comes at an increased cost. Planning the project well ahead of time can allow for reduced costs at slightly longer turnaround times.
Supply Chain Management is Crucial for Staying Cost-Efficient
Counterfeit mitigation is critical in all PCB manufacturing, but even more so in highly regulated industries such as aerospace electronics. Inadvertent use of counterfeit components can result in serious issues with functionality, longevity, and durability, and in the highly regulated aerospace industry, these issues can be catastrophic. Having a trusted and vetted supplier for all components can help mitigate the risk of counterfeit components. Still, during component shortages, this can drive up the materials cost and extend project timelines, which also increases the project’s overall cost. When combined with optimized designs, supply chain management can help the project stay cost-efficient by anticipating component needs and designing PCBs to use readily available components. Finding an electronic contract manufacturer who understands the need for supply chain management and has a robust system will help keep costs manageable without incurring any additional risk of counterfeit components.
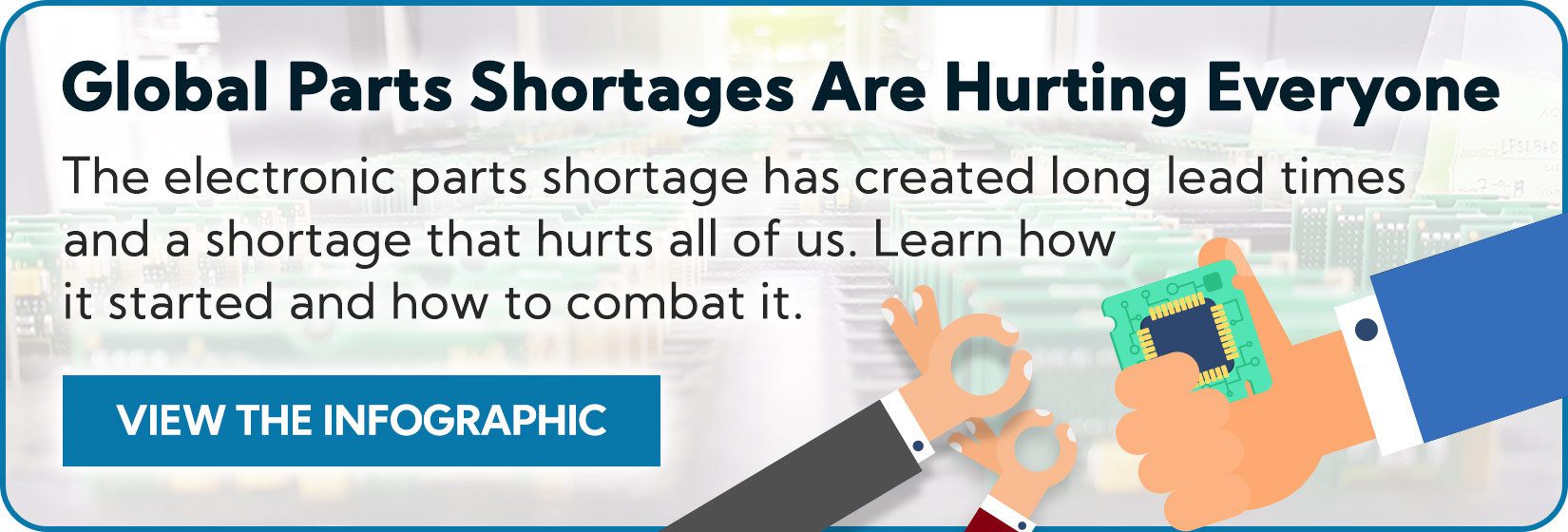
Find the Right Electronic Contract Manufacturer Who Will Not Compromise on Quality in Aerospace PCB Manufacturing
Staying cost-efficient is essential, but never at the cost of quality. Opting for the lowest bid can cost more in the long run if there are functionality, durability, and longevity issues. While it may be tempting to outsource PCB assembly overseas for a lower initial cost, this can also increase overall costs when factoring in shipping costs, lowered quality, and the risk of counterfeit components that cannot be easily managed. To stay cost-efficient without compromising on quality, choosing a domestic, turnkey, and certified electronic contract manufacturer with the right equipment, engineers, certifications, and testing capabilities to manufacture aerospace electronics that can be relied on to function safely in any environment is crucial.
The aerospace industry is highly regulated, and rightly so. Quality, functionality, reliability, durability, and longevity are critical to aerospace electronics’ success and safety. While cost is always a concern, it is important to consider value over the bottom line and choose an electronic contract manufacturer who can help optimize design, develop a working prototype, use materials from a vetted supplier, and perform the proper testing. There are many significant technological advancements in the aerospace electronics industry, which rely on electronic contract manufacturers who can produce quality devices while respecting the cost-efficiency needed to make the process accessible.
Why Partner with Levison Enterprises?
Levison Enterprises invites aerospace designers and manufacturers to join us in revolutionizing cost-efficient PCB manufacturing for the aerospace industry. Through meticulous design for manufacturability (DFM) analyses and thorough prototyping, we ensure your product meets rigorous standards while minimizing costs. Leverage our expertise to navigate supply chain challenges and mitigate risks, safeguarding against counterfeit components and production delays. With a focus on value and reliability, not just the bottom line, partner with Levison Enterprises to propel your aerospace electronics safely into the future. Contact us today to start the journey.