Design for Manufacturability: Optimizing PCBs for Aerospace Electronic Devices
Aerospace technology demands unparalleled precision, reliability, and performance from electronic devices. Among the critical components that play a pivotal role in these devices are Printed Circuit Boards (PCBs). The Design for Manufacturability principles (DFM) ensures that these PCBs meet the strictest requirements of aerospace applications. Keep reading to learn the significance of DFM in optimizing PCBs for aerospace electronic devices exploring how it contributes to manufacturability, reliability, and overall performance.
Understanding Design for Manufacturability (DFM)
DFM is a systematic approach to designing products to facilitate efficient and cost-effective manufacturing. DFM becomes even more crucial in aerospace electronic devices due to the complex nature of these applications. The objective of DFM is to streamline the manufacturing process, reduce production costs, and enhance the overall quality and reliability of the final product.
The Importance of Quality Control in Aerospace Electronic Manufacturing
Quality control is the cornerstone of aerospace electronic manufacturing, beginning with the design phase. The reliability and safety of aerospace devices are paramount, and any failure in electronic components can have severe consequences. Design for Manufacturability (DFM) takes a pivotal role in quality control by detecting and resolving potential issues at the design stage.
Meeting Unique Needs of Aerospace and Defense
Aerospace and defense applications have unique requirements that set them apart from other industries. Electronic design firms specializing in aerospace understand these distinctive needs and tailor their approach accordingly. DFM becomes a key enabler in aligning electronic designs with these specific requirements, ensuring that the final product meets the highest standards.
Impact of DFM Analysis on Electronic Devices
Performing a DFM analysis is a proactive measure that can significantly impact the outcome of electronic devices. A DFM analysis can influence electronic devices, helping identify potential manufacturing challenges, such as issues with materials, components, or assembly processes. By addressing these challenges early in the design phase, manufacturers can avoid costly revisions and ensure a smoother production process.
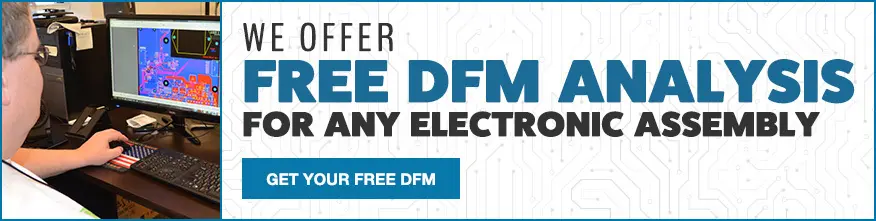
Principles of DFM in Aerospace PCB Design
Below are the specific principles of DFM as they apply to the design of PCBs for aerospace electronic devices:
Materials Selection
Material selection is crucial in aerospace applications when it comes to PCBs. DFM involves selecting materials that meet the stringent requirements of the aerospace industry, including temperature resistance, durability, and reliability. The materials must also adhere to industry standards and regulations to guarantee the safety and optimal performance of the electronic device.
Component Placement and Layout
Efficient component placement and layout are essential for optimal signal integrity, thermal management, and manufacturability. DFM principles guide designers in strategically placing components to minimize signal interference, reduce heat generation, and simplify assembly. Thorough attention is dedicated to the layout to guarantee its alignment with the precise specifications of aerospace applications.
Thermal Management
Aerospace electronic devices often operate in extreme temperature conditions. DFM addresses thermal management by incorporating heat sinks, thermal vias, and proper spacing between components. Ensuring effective heat dissipation is vital to prevent overheating and maintain the reliability of the PCB in demanding environments.
Design for Testing (DFT)
DFM extends to Design for Testing (DFT), where the PCB is designed with testing and inspection in mind. Aerospace electronic devices undergo rigorous testing procedures, and DFT principles help develop testable designs. This includes incorporating test points, boundary scan features, and other elements that facilitate efficient testing and debugging during manufacturing.
Assembly Process Considerations
The assembly process is a critical stage in manufacturing aerospace electronic devices. DFM principles guide designers in selecting assembly methods that optimize efficiency and minimize the risk of defects. This includes surface mount technology (SMT) vs. through-hole technology, automated assembly processes, and advanced soldering techniques.
Compliance with Industry Standards
Aerospace electronic devices must adhere to stringent industry standards and regulations. DFM ensures that the PCB design complies with these standards, covering electromagnetic compatibility (EMC), safety, and environmental requirements. Non-compliance can lead to costly delays and rework, making adherence to standards a fundamental aspect of DFM.
Conclusion
Designing PCBs for aerospace electronic devices requires a meticulous and comprehensive approach. The Design for Manufacturability (DFM) principles are pivotal in optimizing these designs for manufacturability, reliability, and performance. Integrating DFM from the early stages of design is not just a best practice but a necessity in the aerospace industry.
By addressing materials selection, component placement, thermal management, design for testing, assembly process considerations, and compliance with industry standards, designers can create PCBs that meet the unique demands of aerospace applications. Proactively incorporating Design for Manufacturability (DFM) principles not only improves the efficiency of the manufacturing process but also adds to the overall success and safety of aerospace electronic devices.
In an industry where precision and reliability are non-negotiable, DFM emerges as a guiding principle, ensuring that the electronic devices powering aerospace technologies are crafted to withstand the challenges of the skies.
Partner with Levison Enterprises Today
Are you ready to take your aerospace electronic designs to new heights? Levison Enterprises is your trusted partner on this journey, offering:
- Expert Guidance: Benefit from Levison’s wealth of expertise in aerospace electronic design. Work with a team that understands the unique challenges and can customize solutions to meet your needs.
- Innovation Catalyst: Leverage Levison’s commitment to innovation. Transform your designs with cutting-edge Design for Manufacturability principles (DFM) and set a new standard in aerospace technology.
- Proven Success: Join forces with a company that values quality control, meets aerospace requirements, and understands the transformative impact of DFM. Your success is the priority at Levison Enterprises.
- Strategic Collaboration: Forge partnerships that go beyond traditional client relationships. Experience a collaborative journey where your goals align with Levison’s dedication to excellence.
Take the first step by contacting Levison Enterprises now, and let’s turn your aerospace electronic designs into a success story together!