Design for Manufacturability: Key Principles for Successful Electronic Product Development
In the frequently evolving world of electronic product development, the significance of Design for Manufacturability (DFM) cannot be overstated. Design for Manufacturability is a set of principles and guidelines to optimize the design process to enhance manufacturability, streamline production, and reduce costs. Integrating manufacturability into the design phase is crucial for the success of electronic products.
The Foundation of Design for Manufacturability
At the heart of DFM lies the recognition that efficient manufacturing starts at the design stage. By considering manufacturing constraints and requirements early in the development process, engineers and designers can pave the way for a smoother transition from design to production. This proactive approach minimizes the likelihood of design flaws, costly rework, and production delays.
The core principles of DFM encompass various aspects of product design, from material selection to assembly processes. One fundamental aspect is the choice of materials. Designers must carefully evaluate the availability and cost-effectiveness of materials, ensuring that the selected materials align with the product’s functionality and can be easily sourced for mass production.
Streamlining Production Processes
One of the primary objectives of DFM is to streamline production processes, which involves optimizing the design for efficient manufacturing, assembly, and testing. Component placement, ease of soldering, and modular design are crucial in enhancing the manufacturability of electronic products.
Modular design allows for the creation components that can be easily assembled and disassembled. This simplifies the manufacturing process and facilitates more manageable maintenance and upgrades. Manufacturers can respond more effectively by designing products with modularity in mind to changing market demands and technological advancements.
Reducing Costs Through Design Optimization
Cost reduction is a crucial driver behind the implementation of DFM principles. When products are designed with manufacturability in mind, there is a significant potential for cost savings throughout the entire product lifecycle. This begins with the initial manufacturing phase, where efficient processes lead to reduced labor costs and minimized waste.
In addition, DFM enables the identification and elimination of unnecessary features or complexities in the design that may contribute to increased production costs. Designers can create cost-effective and more appealing products by prioritizing simplicity without compromising functionality.
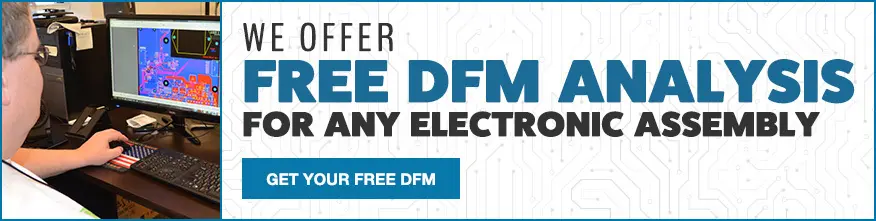
Design Collaboration and Rapid Electronic Prototyping
Successful Design for Manufacturability (DFM) implementation relies on the crucial elements of efficient communication and collaboration between design and manufacturing teams. By fostering a collaborative environment, designers can gain valuable insights into the practical aspects of manufacturing. Collaboration helps identify potential challenges early in the design phase, allowing for rapid electronic prototyping and refinement.
Rapid electronic prototyping is a crucial component of DFM, enabling designers to test and validate the manufacturability of a product through multiple iterations. This cost-effective approach identifies and resolves issues before mass production begins, minimizing the risk of costly redesigns or recalls.
Conclusion
Design for Manufacturability is a cornerstone of successful electronic product development. By integrating manufacturability into the design phase, companies can achieve streamlined production processes, reduce costs, and enhance the overall success of their products in the market.
The principles of DFM encompass material selection, modular design, and efficient assembly processes, all geared toward optimizing the manufacturing workflow. Good collaboration between design and manufacturing teams and rapid electronic prototyping guarantees early detection and resolution of potential issues in the development cycle.
As the electronic industry advances, embracing DFM becomes increasingly critical for staying competitive and delivering high-quality products to consumers. By adopting a proactive approach to design that considers manufacturability from the outset, companies can confidently and efficiently navigate the complexities of electronic product development.
Are you ready to revolutionize your electronic product development and elevate your manufacturing processes to new heights? Levison Enterprises is your trusted partner in embracing Design for Manufacturability (DFM) principles for unparalleled success.
Experience the Power of DFM Expertise
At Levison Enterprises, we understand the pivotal role that DFM plays in determining the success of electronic products. Our seasoned experts specialize in integrating manufacturability into the design phase, ensuring your products are innovative and optimized for efficient manufacturing.
Collaborate for Success
Experience the synergy of collaboration between our skilled design and manufacturing teams. Leverage our industry-leading knowledge to identify and address potential challenges early in the development cycle. By fostering open communication, we work hand in hand with you to create products that stand out in the market.
Streamline Production and Reduce Costs
Witness a transformation in your bottom line as we streamline your production processes. Levison Enterprises is committed to minimizing costs through careful design optimization, efficient assembly techniques, and strategic material selection. The result? A product that exceeds expectations and does so with cost-effectiveness at its core.
Rapid Prototyping for Perfection
Our commitment to excellence extends to the prototyping process. With Levison Enterprises, you can test and refine your designs before mass production begins. Proactively using rapid electronic prototyping helps minimize risks, ensuring that your products adhere to the highest standards of quality and reliability. It lets you see your prototype faster, viewing and comparing several prototypes to determine the best fit for the production run.
Future-Proof Your Products
Stay ahead of the curve by embracing modular design principles. Levison Enterprises helps you future-proof your products with standardized connectors and modular components, allowing for easy upgrades and adaptability to evolving market demands. Your products won’t just keep up; they’ll lead the way.
Seize the Opportunity
Don’t let the complexities of electronic product development hold you back. Take the opportunity to transform your vision into reality with Levison Enterprises. Contact us today to get started on a journey where innovation meets manufacturability and success becomes the standard.
Why Partner with Levison Enterprises on Your Next Project?
Unlock the future of electronic product development with Levison Enterprises! Our Design for Manufacturability (DFM) expertise ensures your products are innovative and optimized for efficient manufacturing. Collaborate with our skilled teams to streamline production, reduce costs, and rapidly prototype your designs for perfection. Future-proof your products with modular design principles, staying ahead of market demands. Don’t let complexities hold you back. Contact Levison Enterprises today and revolutionize your approach to electronic product development.
Start Your Quote Now!