Your Surface Mount Technology Questions Answered by Experienced Electronic Manufacturers
When looking at Surface Mount Technology, or SMT, you may have questions about whether or not it is the right process for the job. If you are not sure which mount is right, looking to an experienced electronic manufacturer with questions about SMT may give you the answers you are looking for.
What is Surface Mount Technology?
Surface Mount Technology (SMT) helps reduce manufacturing costs and increase efficiency, making it possible to build highly complex electronic circuits in smaller assemblies with automated methods. SMT is an assembly and part packaging technology used to place and solder components to the surface directly.
What are the Benefits of SMT?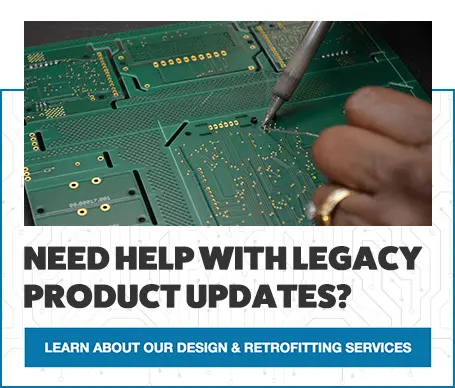
There are many benefits of SMT assembly, including:
· Fewer holes to be drilled, which saves on time. Fewer holes also means better performance due to a smaller loop area.
· Low initial cost set up.
· Fit more mass production and automation.
· Small components that are of higher component density per unit area.
· Components can be placed on both sides of the circuit board.
· Small errors are corrected automatically.
· Better mechanical performance under vibrating conditions.
· Predictable high-frequency performance.
What is the Process Used in SMT Assembly?
The process of SMT has several steps.
· Design Phase: the various components are selected and designed using a software platform. All the design features and layouts are defined.
· Machine Programming: the machine is set up for the manufacturing process. CAD generated data is developed.
· Solder Paste Priming: the solder paste printer is programmed to apply the solder paste via stencils to the pads of the printed circuit board. This is a critical process that must be done carefully to eliminate any potential defects.
· Solder Paste Inspection: some solder paste printing machines come with automatic inspection capabilities, and others have a separate inspection machine. These machines use 3D technology to enable a thorough inspection and will inspect the paste volume per pad and not simply within the print area.
· Pre-reflow Automated Optical Inspection: this ensures and verifies that components are placed in the right place. An AOI machine checks component presence, value, and polarity.
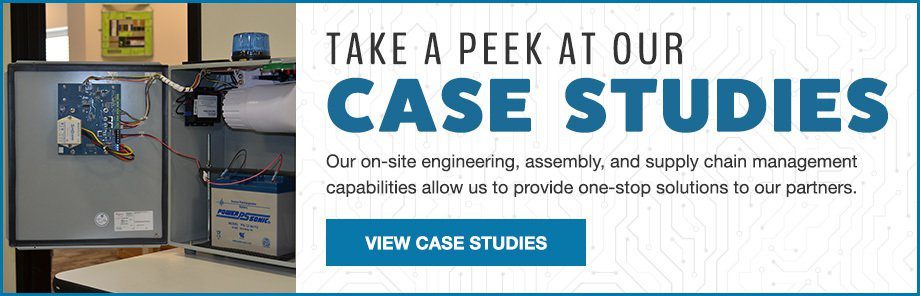
· Reflow Soldering: after all electrical solder connections are formed between the components, reflow soldering is done by heating to a sufficient temperature for the solder joints.
· Reflow Soldering Inspection: an optical inspection is done first to ensure no mistakes exist, and then the process is verified using x-ray inspection.
What are the Different Testing Services Done During SMT Assembly?
During SMT assembly, the following tests are done:
· X-Ray Testing
· In-Circuit Testing
· Automated Optical Inspection
· Functional Testing
Once you understand SMT and the benefits it can have, it makes the decision of determining if it is right for your project much easier. There are many reasons to go with Surface Mount Technology for your electronics project. We can help you determine if SMT is right for your project. Contact Levison Enterprises for answers to all of your printed circuit board assembly questions.
Start Your Quote Now!