Electronic Manufacturing Design and Redesign 101
Development of new electronic products is not an easy process. In fact, it can be downright daunting. It is crucial for a product design to be accurate in order for it to be manufactured error-free, which an experienced electronic manufacturer can help with.
A good electronic product design (or electronic redesign) is foundational for creating a quality and timely product. When the important basics of electronic design get glossed over or forgotten, processes get delayed, products lack specificity, and you’re likely unhappy.
Whether you are ready to develop and launch a new electronic product or searching for an engineer design group to outsource to, we’ve compiled this list of design basics to keep in mind when working on your design. These are the same elements we look for when we design or redesign a product in order to set up efficient manufacturing and a product we can stand behind.
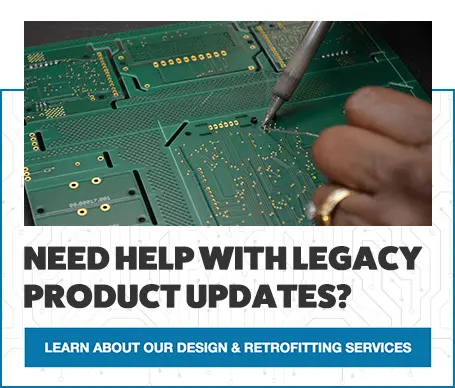
Start From The End
You must take a product’s end-use into account in order to successfully create an electronic design. If what you really need is a giant water cannon, you don’t want to waste time designing a sprinkler. Think critically, carefully, and fully about what the product will do and where it will be required to function. Knowing your destination is fundamental to understanding how you’re going to get there.
Your electronics will also need to stand up to various environmental factors when placed into the final product. This must be considered during the design stage as well. Heat, cold, dust, moisture, and temperature swings will all affect performance. Temperature fluctuations can cause damage to elements due to expansion and contraction. Oxidation, corrosion, and rust caused by moisture can result from overheating. Designing with all of this in mind can protect your product from failure.
Embrace Simple
As engineers, we can get a little too excited about creative design possibilities, but your best option for good design is typically the simplest. No need to go all the way around the block when a straight line will get you from point A to point B. Using industry-recognized notations, schematics, and dimensions will minimize errors when it is time for manufacturing.
Simple is elegant. Simple is often easier. Simple is often cost-efficient. The simplest solution is usually the best one.
Carefully Choose Components
It is important to carefully choose your parts when designing electronics. First and foremost, the manufacturing process will be much easier if you streamline your design and use fewer parts. This will also reduce the risk of errors and save you money.
You can also increase your design success and save money with standard parts. They are much less expensive than custom components and they are much easier to source. In addition, using standard parts will make your design easier to update and reproduce in the future.
Tracking the availability of your components while designing is also a good idea. Parts obsolescence can make even the most carefully crafted design useless. Forecasting the risk of a part becoming discontinued and estimating a timeline of when that will happen will prevent a pause in manufacturing, and give your design firm time to fabricate a custom component, or redesign to further avoid interruptions in the process.
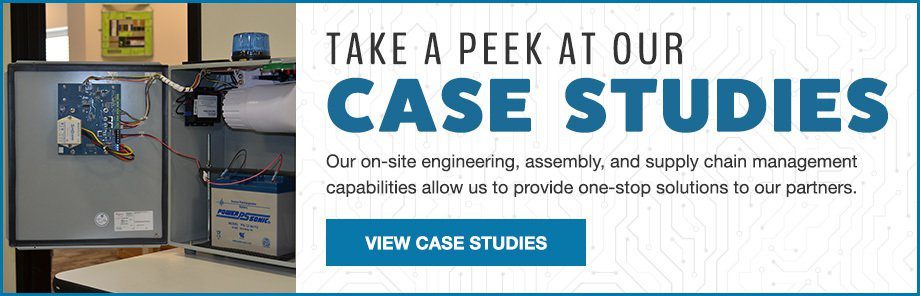
Strive for Complete Clarity
A good design should not create questions. It should answer them. The more clearly you spell out your goals and how you’d like to reach them, the easier it will be to put your designs into motion. Without going overboard, the design should include a comprehensive technical data package (Bill of Materials, Schematics, Mechanical drawings… etc.) that clearly addresses each major facet of the desired end product. All of these elements should directly align with your intended goals for your end product.
A big problem with electronic manufacturing is when files, blueprints, and other necessary information is incomplete or missing. You must have a complete outline of everything that needs to be done, including how and where every component needs to be placed, how big and where each hole must be drilled, and what tool will be used. The manufacturing process can and will fail without all of this information.
Bill of Materials
A bill of materials (BOM) can be generated as your electronic design develops. Every part must be listed, along with the quantity, manufacturer part number, and PCB footprint for each component. This information is critical because it tells your manufacturer how many of each part is needed, explains the size of each part for area estimations, and describes each circuit element used for purchasing, inventory, and substitution. An accurate BOM provides details on all the parts required to build a shippable product.
The BOM must be kept up to date with the design at all times. When information is omitted from the BOM, it can mess up manufacturing. If components are not listed by how your product should be assembled, you risk it being built slowly, incorrectly, or not at all.
Remember the Manufacturing
Part of having your eye on the end-goal is keeping the entire process in mind as you design. Some amount of attention should always be given to the product’s manufacturing and its operational environment. You can create a perfect design but if the product won’t be able to function in its intended environment, the design is basically junk.
Make It Complete
Without going overboard, the design should include a comprehensive technical data package (BOM, schematics, mechanical drawings, etc.) that clearly addresses each major facet of the desired end product. All of these elements should be directly aligned with the intended goals for your product.
Design for Manufacturability
Part of having your eye on the end-goal is keeping the entire process in mind as you design. Some amount of attention should always be given to the product’s manufacturing and its operational environment. You can create a perfect design but if the product won’t be able to function in its intended environment, the design is basically junk.
A design for manufacturability (DFM) analysis can do a lot to make sure your design is optimized. A DFM is an effective way to determine if your design meets the requirements of the manufacturing process to actually produce a successful product. It will detect design issues and that could lead to manufacturing problems.
Avoiding Mistakes
Design mistakes will always lead to an increased cost of production. This is why it is so important to have a DFM analysis done, hire a design engineer group, or partner with an electronic manufacturing service with engineering in-house who can look over your design for you.
If you design your own electronics, you might also consider having a review from an engineer design group before prototyping. An independent design review could help you avoid hidden mistakes that could torpedo your design during manufacturing and send you back to the drawing board.
Get It Done
There is a saying that perfection is the enemy of done. It’s also the enemy of progress, profitability, and most importantly, sanity. It’s so tempting for a designer to spend tons of time on details that, ultimately, don’t matter. Stay focused on getting it operational and call that done. There will be plenty of opportunities to revisit and make enhancements to the design if necessary or desired.
Although verification is integral to each stage of the design process, we’ll always undertake a complete product verification against the original specification before a product is released for production.
Making the Decision to Outsource
Sometimes designing your own electronics isn’t feasible. You may turn to an outside engineer design group for assistance. Outsourcing has some clear advantages including efficiency, lower costs, and gaining specialized knowledge, abilities, and processes of seasoned design experts.
Outsourcing makes a lot of sense in this time where technology moves at a rapid pace. By the time your team is up to speed on the latest innovations, the electronics industry is on to the next new discovery. Outsourcing to an engineer design group brings you the latest and best technological advances without the learning curve. Working with the right partner can speed up the design process and bring your products to market much faster.
Specifications of Design
This is the only way to truly know when you are “done” with your design. Your complete specifications need to be agreed upon by all parties. Only then can you be certain that the end users will be satisfied.
The Bottom Line
Take the time to really think through and really plan your electronic design. Once you’ve got it all spelled out, go back and make sure you haven’t accidentally contradicted yourself or left questions unanswered. Double check that your goals and processes are clearly articulated.
You do not want someone doing guesswork on your product. You also do not want your electronic manufacturing and or electrical assembly held up by questions you could have answered from the beginning.
When you put the time into your electronic product design, you are investing in something that will more likely stay in its timeline and be completed to your specifications.
Start Your Quote Now!Design and Redesign at Levison Enterprises
Levison Enterprises is an engineering design group that can bring your idea or concept to a fully functional, compliant, and tested product ready for production. The design basics listed above are the exact same ones we use when we put our design team to work on your project. We believe in these basics because we know they work.
Years of assisting our customers with forward-thinking and clear designs have helped us see what’s truly essential and what can be cut away to save your project in both time and money. But we never take away anything that would jeopardize your project’s quality. That always remains our number one priority.
The next time you are designing or redesigning a product, keep these basics in mind to put together a complete and clear design package. Or bring your design to us and we can work together to quickly and efficiently create a design that will meet your goals and possibly exceed them. We would love to add our team’s years of experience and design expertise to your next project. Contact Levison Enterprises today to see what we can do for your next design or redesign.
This post was originally published JUNE 14 2018 and updated for April 2021.