6 Things That Might Be Missing From Your Medical Device Electronics Design
An effective medical device design addresses a medical need and offers a solution. It is also compliant with healthcare regulatory mandates and delivers functionalities that satisfy the end user’s needs. However, electronic medical devices are only as useful as their design dictates. Before the manufacturing of your medical device, it’s a good idea to have a Design for Manufacturability (DFM) analysis done on your electronic design to make sure it’s optimized for manufacturing.
You may find there are some critical information gaps in your medical device electronics design that must be filled in order to move on to production. Electronic design and manufacturing must be precise, yet there are some common areas that tend to be overlooked when companies select a contract manufacturer and prepare to move forward with assembly.
1. Through-Hole or SMT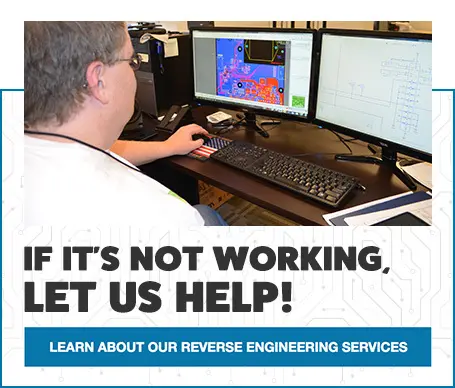
While on a prototype it might be easier to mount your medical device components via through-hole technology, surface-mount technology (SMT) is probably a wiser choice for your production run. Complex designs typically call for SMT. Through-hole can be a proof of concept, but the actual design and product would be a different layout. Sometimes the parts are available for SMT, but not for through-hole.
2. Component Placement
An often-overlooked part of medical device electronics design is the placement of the components. Manufacturing costs can rapidly increase if the design doesn’t take automated assembly into consideration. Components situated at odd angles or too close to the edge of a board can cause expensive retooling before production can begin.
3. Component Sensitivity
It is also important to consider the environment your final product will be exposed to in terms of heat, weather, or other stimuli. Your medical device electronics design should reflect this. Will the components you list in your Bill of Materials hold up in various conditions? Does your project need a special coating or some unique treatment in order to assure longevity? It is not easy to avoid moisture and temperature sensitive components. So, it’s important to work closely with your manufacturing partner if components need to meet any special requirements and/or if any extraordinary assembly methods might be needed.
4. Component Sourcing
Electronic design and manufacturing are under close scrutiny by federal regulators. You’ll want vetted suppliers to make sure there are no counterfeit or imperfect parts being used in your product. Traceability can give you the assurances you need without need for additional quality testing.
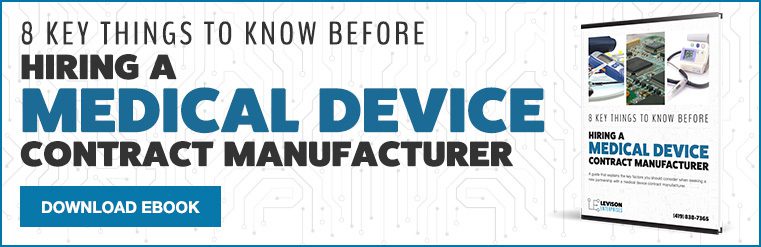
5. Testing
Testing is crucial. Make sure to find an ECM that always does testing in house and continuously tests throughout your production. That way if troubleshooting is needed, they can do so on the fly. This saves time and money.
6. In-House Engineering
You know your product, and it’s awesome. However, a second set of eyes never hurts. This is why having an ECM with in-house engineering is extremely important. Plus, knowing that they can troubleshoot at any given moment and have ideas before they even contact you is a huge bonus.
Levison Enterprises wants to help you turn your electronic medical device design from a vision to a reality. We offer in-house engineering and testing that can take your product from concept right through the supply chain to end-user. We want to help your medical device innovation serve patients worldwide. Contact Levison Enterprises today to see how we can assist you with your next electronic medical device design and manufacturing.
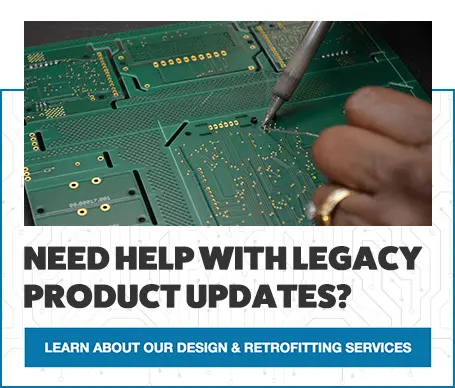