5 Tips to Optimize Your PCB Design for Manufacturability
You and your team work hard to bring a product to market. However, overlooking one tiny detail can mean the difference between a printed circuit board’s success and sending your PCB back to the drawing board. A Design for Manufacturability (DFM) analysis will take the worry out of the process. Performing DFM before production starts is proven to save time and money by making sure your design meets the requirements of manufacturing processes to actually produce the PCB.
Design for Manufacturability is a critical part of your product development process. You want to make the most of it. Luckily, there are additional steps you can take to optimize your DFM.
Use an ECM with Vetted Supplier Network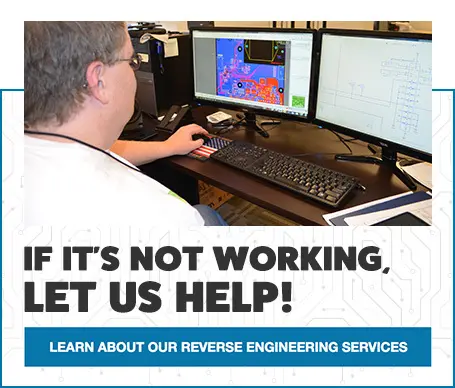
Counterfeit parts are a huge problem in electronic manufacturing. You can eliminate this concern when you partner with an ECM that has a vetted supplier network. When your ECM has a trusted network of vendors, you reduce the risk of knockoffs and poor quality parts being used in your build. Using only the highest quality parts and materials will make a big difference in the performance of your PCB.
Find an ECM with Quality Certifications
There should be no question over quality when it comes to your design and assembly. Compliance is key. This is why it’s important to work with a manufacturing partner that can and will provide you with its ISO or AS9100 certifications.
Working with a quality certified ECM ensures your PCB will meet or exceed industry standards.
Reduce the Number of Parts
Complicated design leads to complicated assembly. Streamlining your design and reducing the number of components used in it will make the manufacturing process simpler. It will also reduce the risk of errors. In addition, using fewer parts leads to cost savings. You don’t have as many components to buy. You don’t need to test them and you have less parts to inventory, store, and manage.
Choose Standard Parts
There is a clear advantage to using standard components in your PCB. First and foremost, standard parts are much less expensive than their custom counterparts. You can also get your hands on them more quickly, thus avoiding production delays. Using standard parts also reduces the risk of errors being made during assembly. Plus, using standard parts will make your PCB easier to update and reproduce in the future.
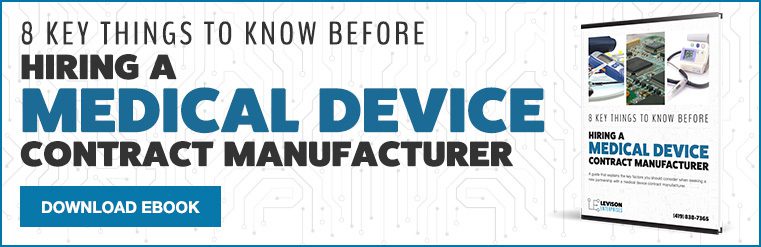
Utilize In-House Testing to Reduce Production Errors
You want to make sure your product can stand up to the job it’s being made for. An ECM with in-house testing will not only put your product through its paces, but will also be able to quickly and efficiently identify and correct problems that arise. Multiple experiments and testing cycles will be used during all stages of production to be sure your PCB functions properly and will continue to do so during its real-world application.
Let Levison Enterprises guide you through the DFM stage of development. We will make suggestions on design tweaks and parts alternatives to eliminate a rework, saving you time and money. Levison Enterprises is AS91100D certified, ISO 9001 certified, IPC and J Standard certified, U.S. SBA certified, as well as ITAR registered. Contact Levison today to see how we can assist with your next PCB project.
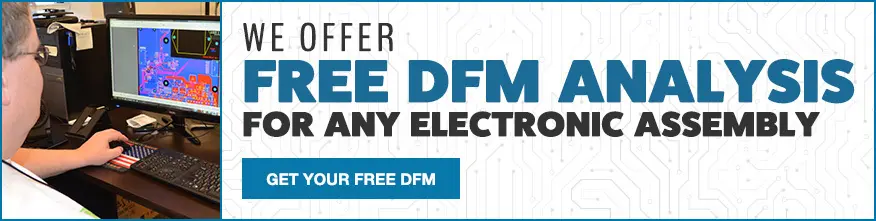