5 Principles of Design for Electronic Manufacturing Which Lead to 10 Levels of Savings
Design for Manufacturing or DFM is a process an electronic manufacturer uses to make parts, components, and products less expensive by easing their manufacturability. It’s how you avoid getting a very pretty part that cannot function properly. It’s how you avoid manufacturing an outdoor part for your Northern Michigan operation that cannot operate in freezing temperatures.
It’s how project managers can avoid a lot of avoidable headaches.
Incidentally, design for manufacturing is also a way an electronic manufacturer builds cost savings and efficiency into your product or projects.
What is Design for Manufacturing or DFM?
Design for Manufacturing operates on five key principles that are critically considered during the design phase of any project. These principles are process, design, materials, environment, and compliance. A design for manufacturing cross-functional team will look at a design and eliminate all the possible flaws and inefficiencies as well as coordinate all the ways it can be optimized.
Effectively, the electronic engineering team is looking to tear apart the design in order to make it better and stronger. They’ll look and re-look at the drawings. They’ll talk about the users and who has already created a similar product for those users. They’ll ask each other questions about ways to make the product better, more competitive, more reliable. They’ll focus in on the five key areas of design for manufacturing.

Process
You want an electronic manufacturing process that’s going to get the job done well and for the lowest cost. During design for manufacturing, the team will analyze what will meet those two criteria best for your project. You don’t want to use a highly-specialized process for a product that could be done cheaper another way while still giving you the same quality.
Part quantity, materials, and potential subsequent processes are all part of considering alternative manufacturing processes for your project.
Design
When analyzing your design, your team will look at how well your drawings conform to accepted manufacturing principles, given the manufacturing process that was determined for your product. This design should include notations for all the specifications that are relevant to your manufacturing process.
Materials
Here again, it is possible to have a little overkill with expensive materials that do not necessarily have to be in your design. You want your product to perform correctly and withstand the conditions it will need to withstand, but there may be less expensive materials you can use.
Your team will examine how strong the materials need to be in your product, how heat resistant it needs to be, and how it needs to respond to electricity. Additionally, your product may have color, thermal, or other properties that need to be checked against the selected material.
Environment
Not only does your product need to be constructed of appropriate materials, but it needs to be designed so that those materials can perform under its likely conditions. A part that will always be in climate-controlled buildings is going to naturally have a very different design than one that will need to function at the bottom of the Atlantic Ocean.
Even if your environment isn’t too extreme, your product will be examined to ensure that all of it is prepared to withstand the conditions where you need it to perform.
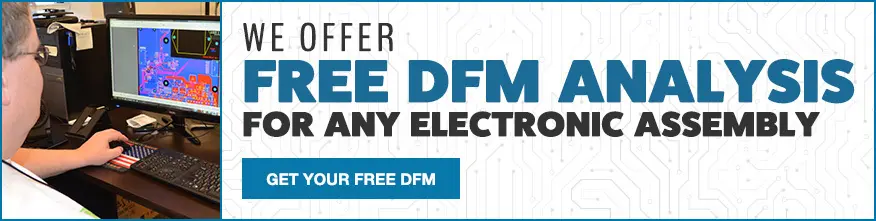
Compliance
Every product has to pass a certain amount of testing. They might be general safety or quality standards. Or, you might have industry standards or even those that your organization requires. Whatever standards your product must meet, it’s important that they are considered before the product goes to the manufacturing stage.
By taking this important step in the design for manufacturing process, the team digs out all the unnecessary bulk and bakes in any possible savings. What may seem like an extra step, actually has a lot of potential to save time and money in the manufacturing process of your product.
10 Levels of Potential Savings from Design for Manufacturing
1. Fewer parts are used. Materials, assembly, engineering, shipping. All areas of manufacturing are impacted when your design for manufacturing process decreases the number of parts in your product.
2. Fewer specialized parts. Custom parts are expensive and often become unnecessary when DFM is applied and quality standard parts are subbed in for custom.
3. More multi-function parts. When a part can do multiple things, it saves you time and money versus creating parts for every little process. DFM looks for opportunities to use multi-function parts.
4. More multi-use products. If you can create multiple products to use the same parts, now your getting double the savings on standardize or multi-function parts. DFM looks for these opportunities.
5. More multi-use designs. Design modules help you decrease your design cost and time on future products that use standard components and drawings.
6. Easier manufacturing. When your DFM process roots out super-specialized or tight processes, your manufacturing costs go down (and probably the errors).
7. Fewer fasteners. Part of easier manufacturing is optimizing material and labor. If a product can be designed with fewer screws, fasteners, and adhesives, your time and production costs go way down.
8. Fewer hands. Every time a part has to be touched, turned, flipped over, etc., it slows down. Symmetrical parts and other design elements added during DFM can limit these touch points.
9. Only one direction. If possible, your DFM process will make it so your assembly only has to move your product in one direction. This is determined by how parts can be added to your product so a careful consideration of this will keep your manufacturing process moving smoothly.
10. Fewer compliance issues. Standard, tested parts and an eye on the end product’s needs (including compliance) all lead to a better, more efficiently produced product. Ultimately, this is the goal of design for manufacturing.
As doers, it’s always tempting to jump right into the manufacturing of your product. Design can feel tedious and even unnecessary. But keep an eye on what all goes into design for manufacturing and what it can yield to you in lowered costs, time, and compliance issues.
Levison Enterprises uses design for manufacturing as part of the range of our electronic manufacturing services we offer to bring our customers quality products with the highest built-in efficiency. Contact us to discuss our design for manufacturing process and how it can benefit your next product.