5 Factors That Influence Military PCB Design in Electronic Manufacturing
Aerospace and military-grade printed circuit boards must be as tough and reliable are those who use them in the field. There is no room for error and your electronic manufacturer is counted on to be mission ready. This makes PCB assembly and manufacturing for the military unique. Knowledge and understanding of what must be done to create a circuit board with high reliability that contributes to the long service life of electronic products under extreme conditions is a must. Therefore, it’s important to find an electronic manufacturer that has the quality standards, certifications, and experience to handle the demands of these kinds of projects.
1. Construction Materials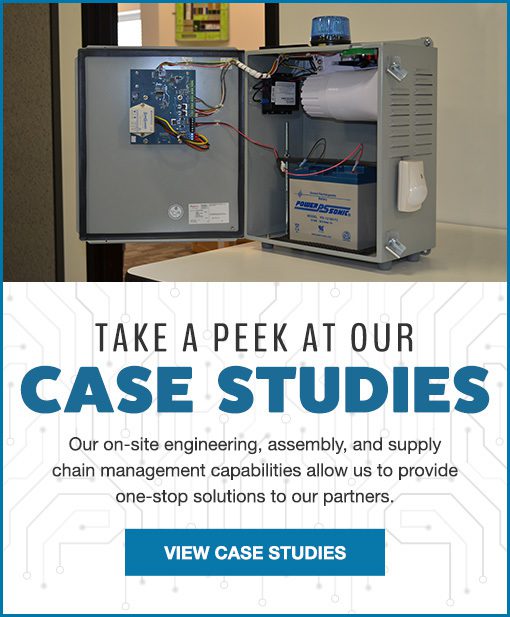
Military grade PCBs must be built to withstand extreme conditions and high temperatures. A contract manufacturer able to tackle aerospace and military PCB assembly will have in-depth knowledge of different composites, materials, and substrates. Aluminum and copper are often use because they can withstand extreme heat. Anodized aluminum is also used at times in order to minimize the effects of heat induced oxidation.
2. Coating and Surface Finishes
Special surface finishes and coatings are required during PCB Assembly for military and aerospace applications. This is due to harsh environmental working conditions, including heat, humidity, water and vibration. Thermal compounds will insulate components, protect them from heat and reduce vibration that can crack solder. Boards are often coated with high quality acid or acrylic-based sprays. However, other surface finishes, including immersion silver, are also an option.
3. Through-Hole PCB Assembly
Durability, reliability and strength are major considerations that must be made during military and aerospace PCB assembly. Your contract manufacturer must be willing and able to minimize vibration when mounting components. This is why through-hole technology is the best method of mounting during PCB assembly. Boards manufactured with through-hole technology are extremely durable. This is because soldering from both the top and bottom of the board creates very strong physical bonds between the components and the board.
4. Counterfeit Parts Mitigation
Counterfeiting can be a big problem is PCB assembly. It leads to product failures, as well as lost revenue for your company. It is critical that counterfeit parts are avoided at all costs when fulfilling an aerospace, military or government contract. This can be avoided when you work with a contract manufacturer that practices certified best processes and procedures, such as source assessment and fraudulent distribution avoidance. Your manufacturing partner should have a well-vetted and trusted chain of suppliers to guarantee only the bust parts go in to your PCBs.
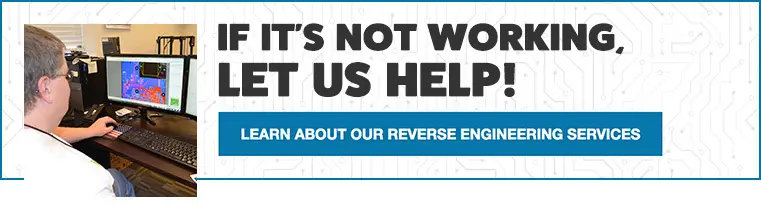
5. Qualifications
A contract manufacturer’s certifications will tell you a lot about its capability on handling your military or aerospace electronics project. Theses certifications show a CM’s commitment to quality. Take the ITAR certification/qualification, for example.
The International Traffic in Arms Regulation (ITAR) is required for military and aerospace PCB assembly. It is regulated by the Department of State and comes with regularly updated requirements to reflect changes in current technology, as well as political and security climates. ITAR restricts sensitive information relating to the design and production of military and intelligence devices, so you can trust that your drawings are being handled with the required degree of security.
Levison Enterprises has successfully earned and maintained its ITAR certification. We have already fulfilled contracts for the FAA, the Department of Defense, and several other government agencies. As a military experienced electronic manufacturer, we are ready to put our experience and expertise to work for you. Contact us today to see how we can assist with your next project.
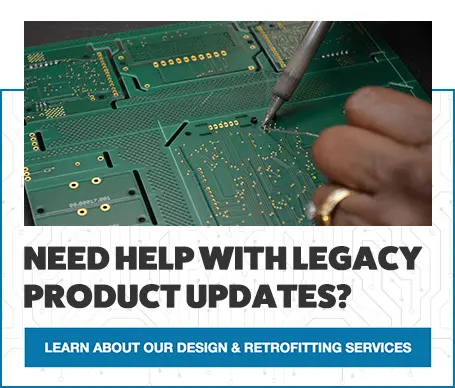