5 Advantages To Using SMT in Your Electronic Manufacturing Project
The old saying “bigger is better” just isn’t accurate in the world of electronics. This is especially true when it comes to surface-mount technology (SMT.) SMT places components directly onto the surface of a printed circuit board in order to create a circuit. It has become a preferred method of creating circuits in the electronics industry. Both surface mount technology and through-hole can be used on the same PCB. However, in many cases, SMT versions of through-hole PCB designs can be produced. Surface mount technology can make a big impact on design and development. Here are some of the advantages of using SMT in your electronic manufacturing project:
1. Small Footprint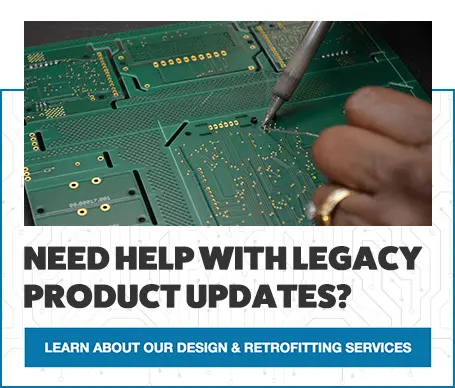
If you are dealing with a small PCB board, placing your components with surface-mount technology can keep the board small. SMT components are smaller than those used in through-hole because it has either smaller leads or no leads at all. Because of this it takes up less than half of the space a through-hole mount would take. It will also lead to a decrease in weight of the PCB. An SMT component often weighs just one-tenth of its through-hole equivalent.
2. Low Cost
That small size leads to an important advantage when using SMT in manufacturing. Once set, surface-mount technology typically requires lower production costs than through-hole placement. The size of the board is reduced, the number of drilled holes is reduced, and routing of traces is reduced. That leads to reduced material handling costs and a faster manufacturing process which, in turn, brings down the cost of the whole project.
3. Higher Density
You are able to pack more on your PCB using SMT. Because there are no holes, you can add more components per unit of area. You can also add more connections per component. And, because holes do not block routing space on inner or back-side layers, components can be placed on both sides of the circuit board. That can sometimes reduce the need for multi-layer boards.
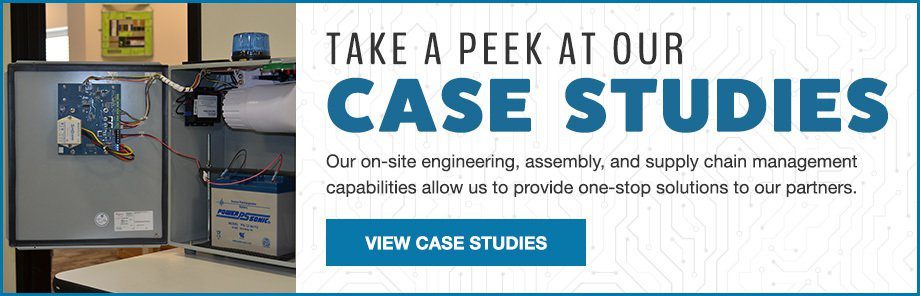
4. Quick Turn Around
Surface-mount technology is a much more streamlined manufacturing process compared to through-hole. Time is saved because components are applied using a solder paste instead of drilling holes in the PCB. The work that takes hours placing components of a through-hold board can take just five minutes with SMT.
5. In-House Engineering for Testing/Prototype
Having in-house engineering for your testing and prototyping of SMT can help during the design phase. They are able to test on the spot and/or make corrections, test new power sources, etc. You will avoid communication breakdowns that often occur when you are working with a new product team.
If you are considering surface-mount technology services for your next PCB project, turn to Levison Enterprises. Our expert team will help you determine if SMT is the appropriate method. We specialize in electronic product development and manufacturing. Let Levison work for you. Contact us today for questions on surface-mount technology.
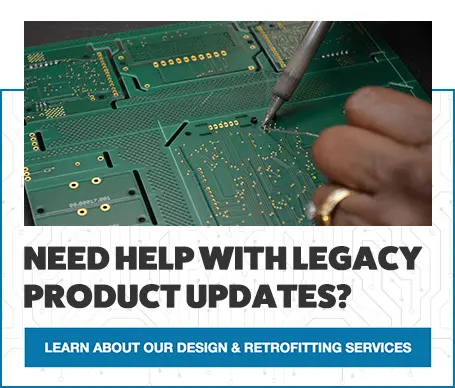